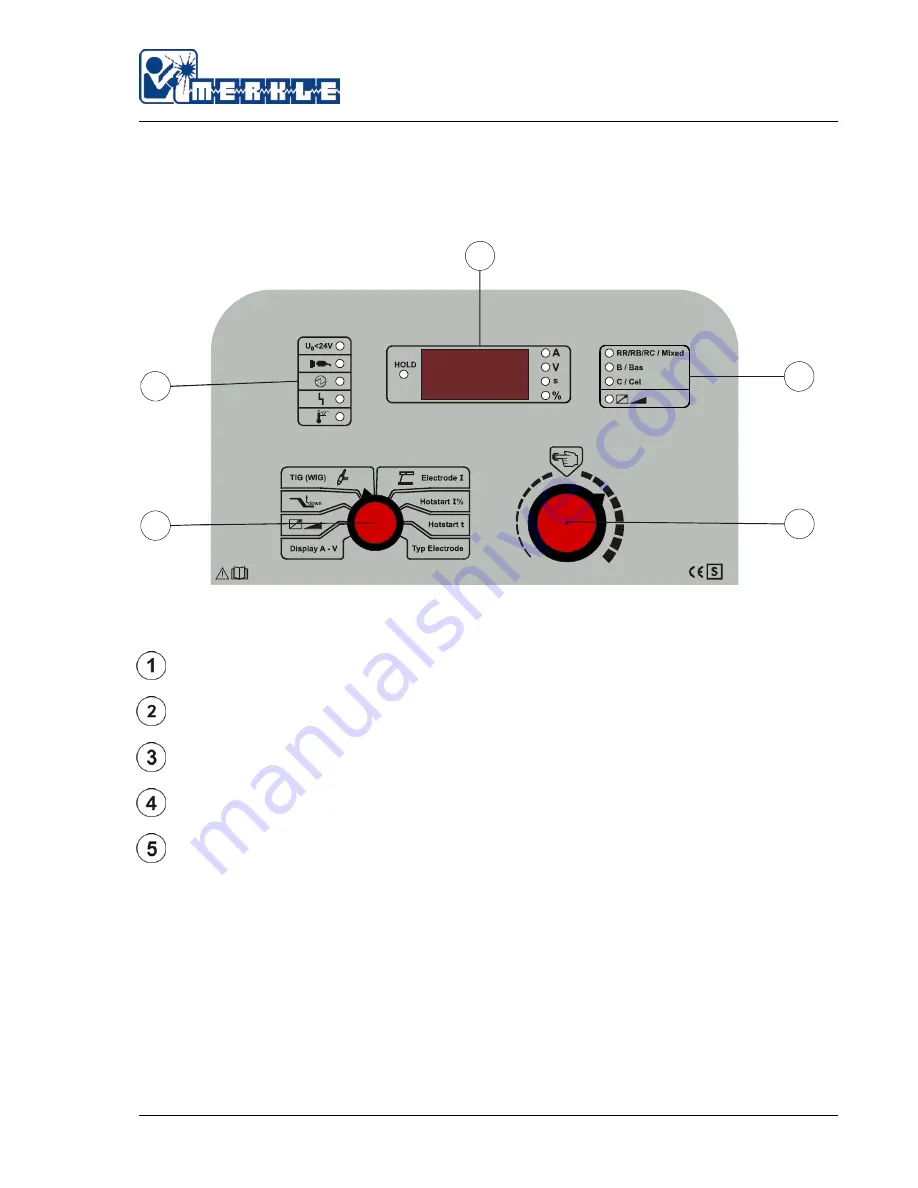
Controls
10
4.
Controls and displays
You learn in this section, the controls and the displays about their welding unit and gain a first
instruction to its handling. The following elements are present on the control panel:
1
2
3
4
5
Step switch for selection the operating mode
Status display
Operating mode display
Adjusting knob withPush Button
Multi functional display