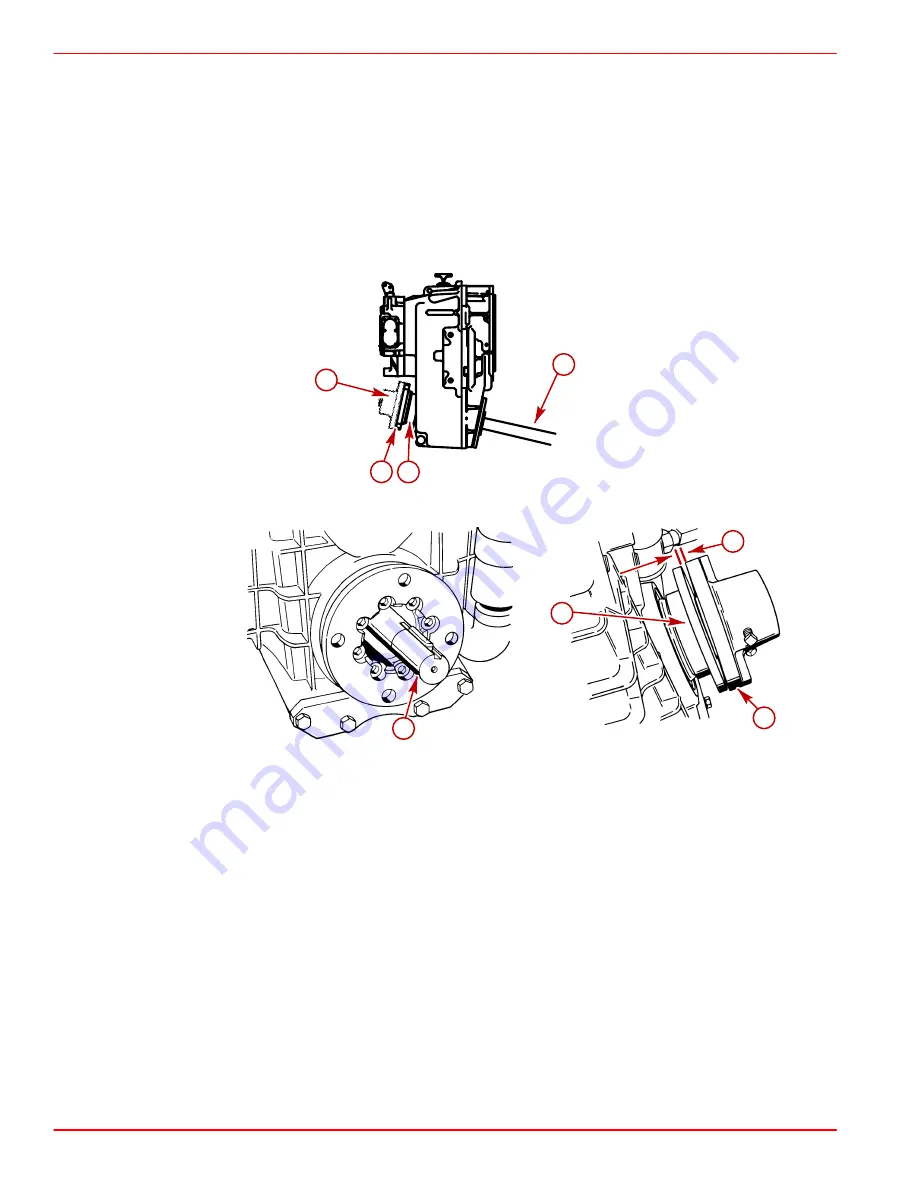
GASOLINE ENGINE 8.1 S INBOARD MODELS
Page 28 of 58
MODELS WITH V-DRIVE TRANSMISSIONS
1. Lift engine into boat and position so that enough propeller shaft protrudes through
transmission and output flange for propeller shaft coupler to be attached. Then install
coupler and position engine (no visible gap between coupling faces when butted
together). Adjust engine bed height if necessary to obtain proper alignment. DO NOT
use mount adjustments to adjust engine position at this time.
IMPORTANT: Engine bed must position engine so that a minimum of 1/4 in. (6 mm)
up and down adjustment still exists on all 4 mounts after performing final alignment.
This is necessary to allow for final engine alignment.
75534
a
b
c
d
Velvet Drive
50608
50608
a
d
c
b
ZF / Hurth 630V
a -
Propeller Shaft
b -
Propeller Shaft Coupler
c -
Transmission Output Flange
d -
No Visible Gap Allowed
2. Ensure that all 4 mounts are still positioned properly. Fasten mounts to engine bed with
3/8 in. (10 mm) diameter lag bolts (of sufficient length) and flat washers. Tighten lag bolts
securely.
3. Disconnect overhead hoist and remove sling.