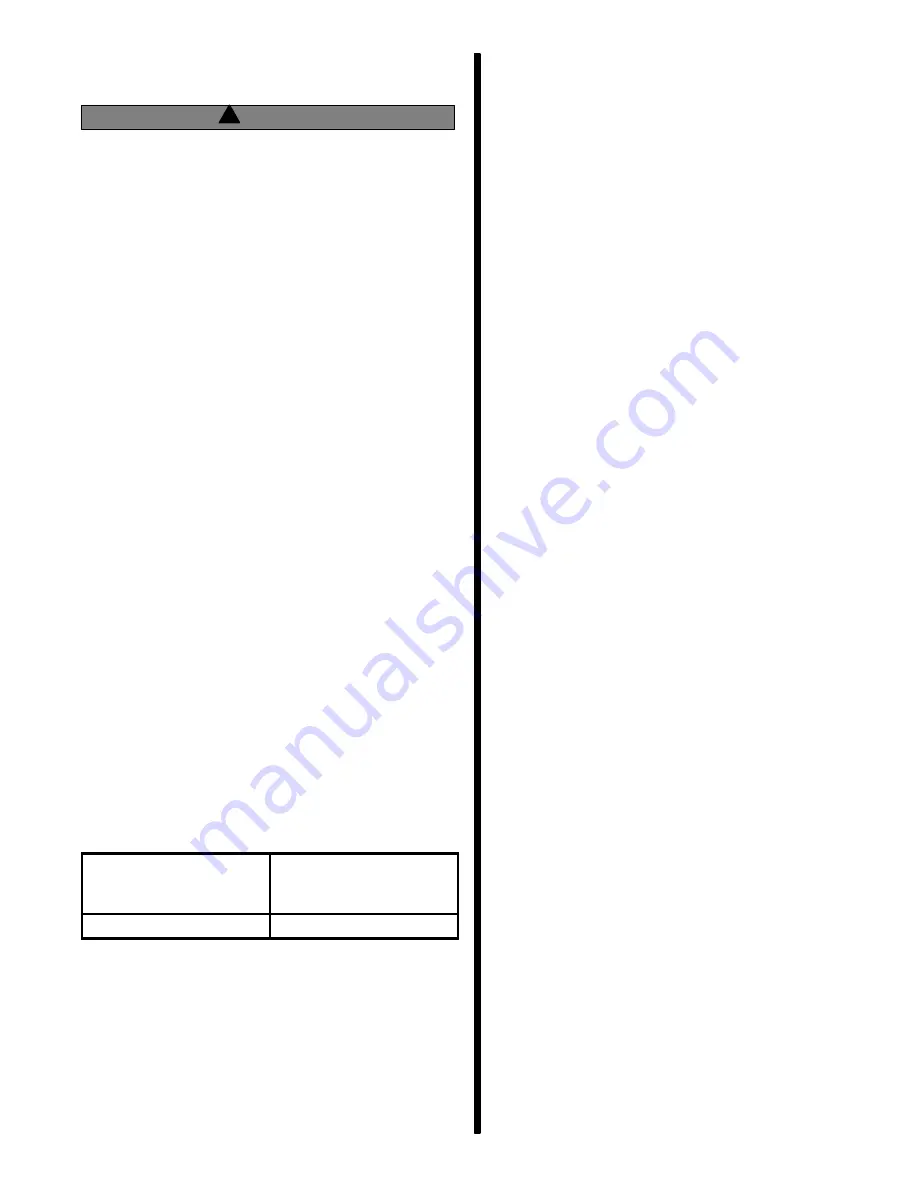
CLOSED COOLING MODELS - 6B-19
90-823225--1 1096
Pressure Testing System
!
WARNING
Allow engine to cool before removing pressure
cap. Sudden loss of pressure could cause hot
coolant to boil and discharge violently. After en-
gine has cooled, turn cap 1/4 turn to allow any
pressure to escape slowly, then push down and
turn cap all the way off.
If coolant section of closed cooling system is sus-
pected of leaking or not holding sufficient pressure,
and no visible signs of leakage can be found, perform
the following test:
1. Remove pressure cap from heat exchanger or
reservoir.
2. Clean, inspect and pressure test pressure cap,
as outlined under “Testing Pressure Cap,” to
eliminate the possibility that cap is not maintain-
ing proper pressure in system and is causing
coolant to boil over.
3. Clean inside of filler neck to remove any deposits
or debris. Examine lower inside sealing surface
for nicks or other damage. Surface must be per-
fectly smooth to achieve a good seal between it
and rubber seal on cap. Also check locking cams
on sides of filler neck to be sure that they are not
bent or damaged. If locking cams are bent or
damaged, pressure cap will not hold the proper
pressure.
4. Adjust coolant level in fresh water section to 1 in.
(25 mm) below filler neck.
5. Attach an automotive-type cooling system
pressure tester to filler neck and pressurize
closed cooling section to amount specified in
following chart, based on pressure cap rating for
your engine.
Pressure Cap Rating
Amount Of Pressure
Applied To Closed
Cooling System
14 PSI (97 kPa)
17 PSI (117 kPa)
6. Observe gauge reading for approximately two
minutes; pressure should not drop during this
time. If pressure drops, proceed with the follow-
ing steps until leakage is found.
7. While maintaining specified pressure on closed
cooling section, visually inspect external portion
of cooling system (hoses, gaskets, drain plugs,
petcocks, core plugs, circulating pump seal, etc.)
for leakage. Also listen closely for bubbling or
hissing, as they usually are a sure indication of a
leak.
8. Refer to “Testing Heat Exchanger” in this section
and test as outlined.
9. If no leakage could be found in above steps, en-
gine is leaking internally, and it probably is due to
one or more of the following: (1) loose cylinder
head bolts or damaged gasket, (2) loose intake
manifold bolts or damaged gasket, (3) loose ex-
haust elbow or distribution block retaining nuts or
damaged gasket, (4) cracked or porous cylinder
head or block, or (5) cracked or porous exhaust
manifold. Proceed as follows until location of in-
ternal leak is found.
a. Start engine. Pressurize system to previously
specified amount and observe pressure
gauge on tester. If needle in gauge vibrates,
compression or combustion is leaking into
closed cooling section from a leak in the com-
bustion chamber. Exact cylinders, where
leakage is taking place, sometimes can be
found by removing spark plug wires (one at a
time) while observing pressure gauge. Vibra-
tion will decrease or stop when plug wire is re-
moved from leaking cylinder. Stop engine.
b. Remove spark plugs (one at a time) from cyl-
inders and examine for presence of coolant.
A spark plug that is perfectly clean or milky
appearing is a sure indication of a leak.
c. Drain oil from engine and examine for pres-
ence of coolant. Oil usually will be milky if
coolant is present. If coolant is present, re-
move engine from boat and drop the oil pan.
With engine in the upright position, pressur-
ize closed cooling section to previously speci-
fied amount and examine internal surfaces of
engine to locate leak.
d. If no leakage can be found in above steps, en-
tire engine must be disassembled and in-
spected for leakage.
Summary of Contents for 305 CID
Page 7: ...A 1 72000 IMPORTANT INFORMATION GENERAL INFORMATION...
Page 16: ...B 1 IMPORTANT INFORMATION MAINTENANCE...
Page 59: ...C 1 IMPORTANT INFORMATION TROUBLESHOOTING...
Page 92: ...A 2 72975 REMOVAL AND INSTALLATION MCM MODELS ALPHA ONE DRIVES...
Page 103: ...B 2 70246 REMOVAL AND INSTALLATION MCM MODELS ALPHA ONE DRIVES WITH DRIVESHAFT EXTENSION...
Page 120: ...2 72580 C REMOVAL AND INSTALLATION MCM MODELS BRAVO DRIVES...
Page 135: ...D 2 70246 REMOVAL AND INSTALLATION MCM MODELS BRAVO DRIVES WITH DRIVESHAFT EXTENSION...
Page 154: ...E 2 70648 REMOVAL AND INSTALLATION MIE MODELS VELVET DRIVE TRANSMISSIONS...
Page 173: ...F 2 25280 REMOVAL AND INSTALLATION MIE MODELS HURTH TRANSMISSIONS...
Page 189: ...A 3 72615 ENGINE 5 0L 305 CID 5 7L 350 CID...
Page 192: ...3A 0 ENGINES 90 823225 1 1096...
Page 266: ...ELECTRICAL SYSTEMS STARTING SYSTEM A 72079 4...
Page 284: ...STARTING SYSTEM 4A 17 90 823225 1 1096 THIS PAGE IS INTENTIONALLY BLANK...
Page 334: ...C 4 72078 ELECTRICAL SYSTEM CHARGING SYSTEM...
Page 344: ...CHARGING SYSTEM 4C 9 90 823225 1 1096 THIS PAGE IS INTENTIONALLY BLANK...
Page 360: ...D 4 72747 ELECTRICAL SYSTEM INSTRUMENTATION...
Page 380: ...E 4 72761 ELECTRICAL SYSTEM ELECTRICAL KITS...
Page 393: ...F 4 72938 ELECTRICAL SYSTEMS WIRING DIAGRAMS...
Page 438: ...B 5 72681 FUEL SYSTEM MERCARB 2 BARREL CARBURETOR...
Page 467: ...C 5 72085 FUEL SYSTEMS ROCHESTER 4 BARREL CARBURETOR...
Page 497: ...D 5 70389 90 823224 692 5B WEBER 4 BARREL CARBURETOR FUEL SYSTEMS WEBER 4 BARREL CARBURETOR...
Page 538: ...5 71692 E FUEL SYSTEMS MULTI PORT AND THROTTLE BODY FUEL INJECTION...
Page 727: ...F 5 73662 FUEL SYSTEMS BOS SAV EMISSIONS...
Page 744: ...A 6 22381 COOLING SYSTEM SEAWATER COOLING MODELS...
Page 773: ...B 6 72987 COOLING SYSTEM CLOSED COOLED MODELS...
Page 823: ...A 7 72699 EXHAUST SYSTEM GENERAL...
Page 829: ...B 7 72695 EXHAUST SYSTEM MANIFOLDS AND ELBOWS...
Page 835: ...C 7 70593 EXHAUST SYSTEM RISERS...
Page 844: ...D 7 72737 EXHAUST SYSTEM COLLECTORS...
Page 856: ...A 8 DRIVES VELVET DRIVE IN LINE TRANSMISSION...
Page 869: ...B 8 DRIVES VELVET DRIVE V DRIVE AND WALTER V DRIVE TRANSMISSION...
Page 882: ...C 8 25280 DRIVES HURTH DOWN ANGLE TRANSMISSION...
Page 932: ...E 8 DRIVES DRIVE SHAFT PROPELLER SHAFT MODELS...
Page 947: ...A 9 72951 POWER STEERING PUMP...