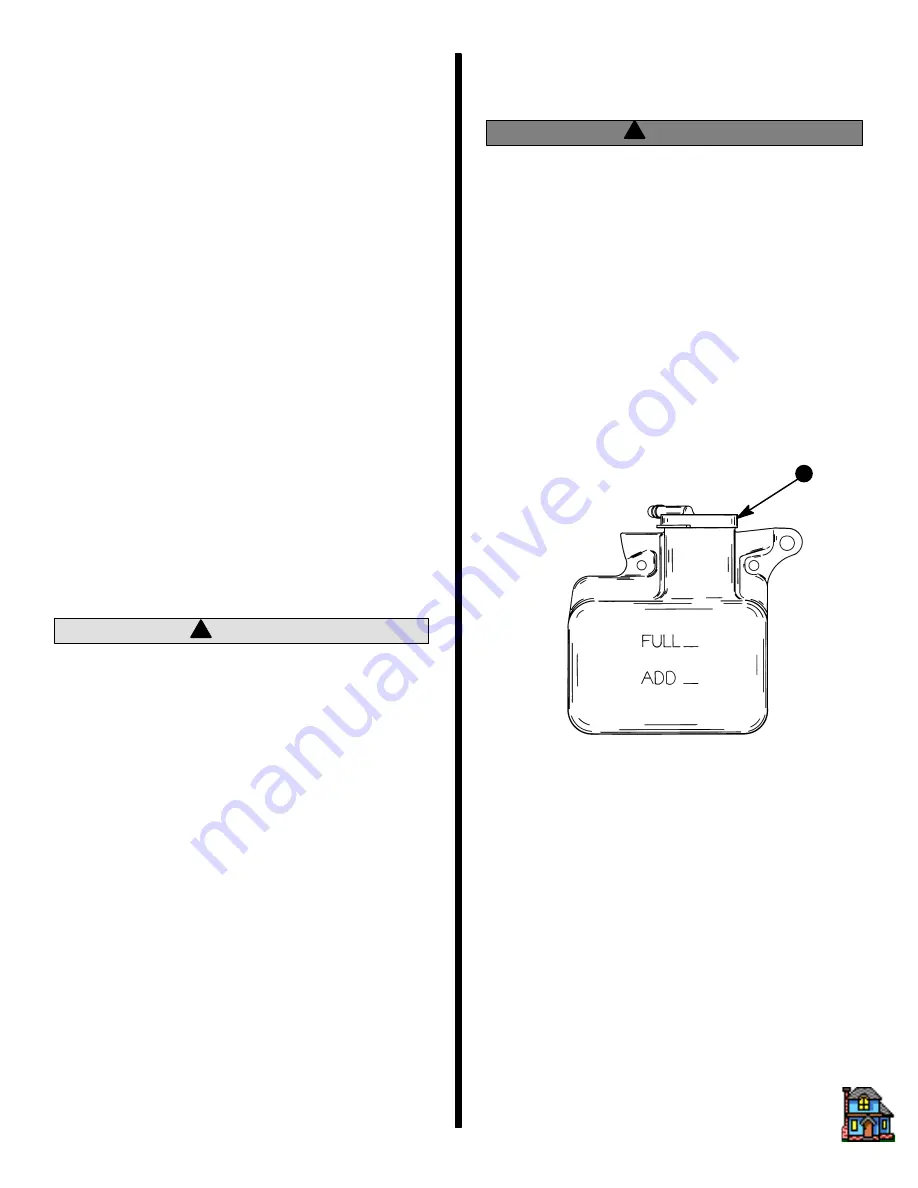
MAINTENANCE - 1B - 11
90-816462 2-695
Filling and Bleeding Power
Steering System
IMPORTANT: Power steering system must be
filled exactly as explained in the following to be
sure that all air is bled from the system. All air
must be removed, or fluid in pump may foam dur-
ing operation and be discharged from pump res-
ervoir. Foamy fluid also may cause power steer-
ing system to become spongy, which may result
in poor boat control.
1. With engine stopped, position drive unit so that it
is straight back. Remove fill cap/dipstick from
power steering pump. Add Quicksilver Power
Trim and Steering Fluid or automatic transmis-
sion fluid (ATF), Dexron, or Dexron II, as required,
to bring level up to FULL COLD mark on dipstick.
IMPORTANT: Use only Quicksilver Power Trim
and Steering Fluid or automatic transmission
fluid (ATF), Dexron, or Dexron II in power steering
system.
2. Turn steering wheel back and forth to end of travel
in each direction several times, then recheck fluid
level and add fluid, if necessary.
3. Install vented fill cap.
!
CAUTION
DO NOT operate engine without water being
supplied to seawater pickup pump, or pump im-
peller may be damaged and subsequent over-
heating damage to engine may result.
4. Start engine and run at fast idle (1000-1500 RPM)
until engine reaches normal operating tempera-
ture. During this time, turn steering wheel back
and forth to end of travel in each direction several
times.
5. Position drive unit so that it is straight back and
stop engine. Remove fill cap from pump. Allow
any foam in pump reservoir to disperse, then
check fluid level and add fluid, as required, to
bring level up to FULL HOT mark on dipstick. DO
NOT OVERFILL. Reinstall fill cap securely.
IMPORTANT: Drive unit must be positioned
straight back and power steering fluid must be
hot to accurately check fluid level.
6. If fluid is still foamy (in Step 5), repeat Steps 4 and
5 until fluid does not foam and level remains con-
stant.
Maintaining Closed Cooling
Coolant Level
!
WARNING
Allow engine to cool down before removing pres-
sure cap. Sudden loss of pressure could cause
hot coolant to boil and discharge violently. After
engine has cooled, turn cap 1/4 turn to allow any
pressure to escape slowly, then push down and
turn cap all the way off.
1. Coolant level in heat exchanger should be full (to
bottom of filler neck).
IMPORTANT: When reinstalling pressure cap, be
sure to tighten it until it contacts stop on filler
neck.
2. Coolant level should be between the ADD and
FULL marks on coolant recovery reservoir with
the engine at normal operating temperature.
193-HR
a
a - Coolant Recovery Reservoir
Flushing Cooling System
If engine is operated in salty, polluted, or mineral-lad-
en water, flush cooling system (preferably after each
use) to reduce corrosion and prevent the accumula-
tion of deposits in the system. Thoroughly flush cool-
ing system prior to storage.
Index