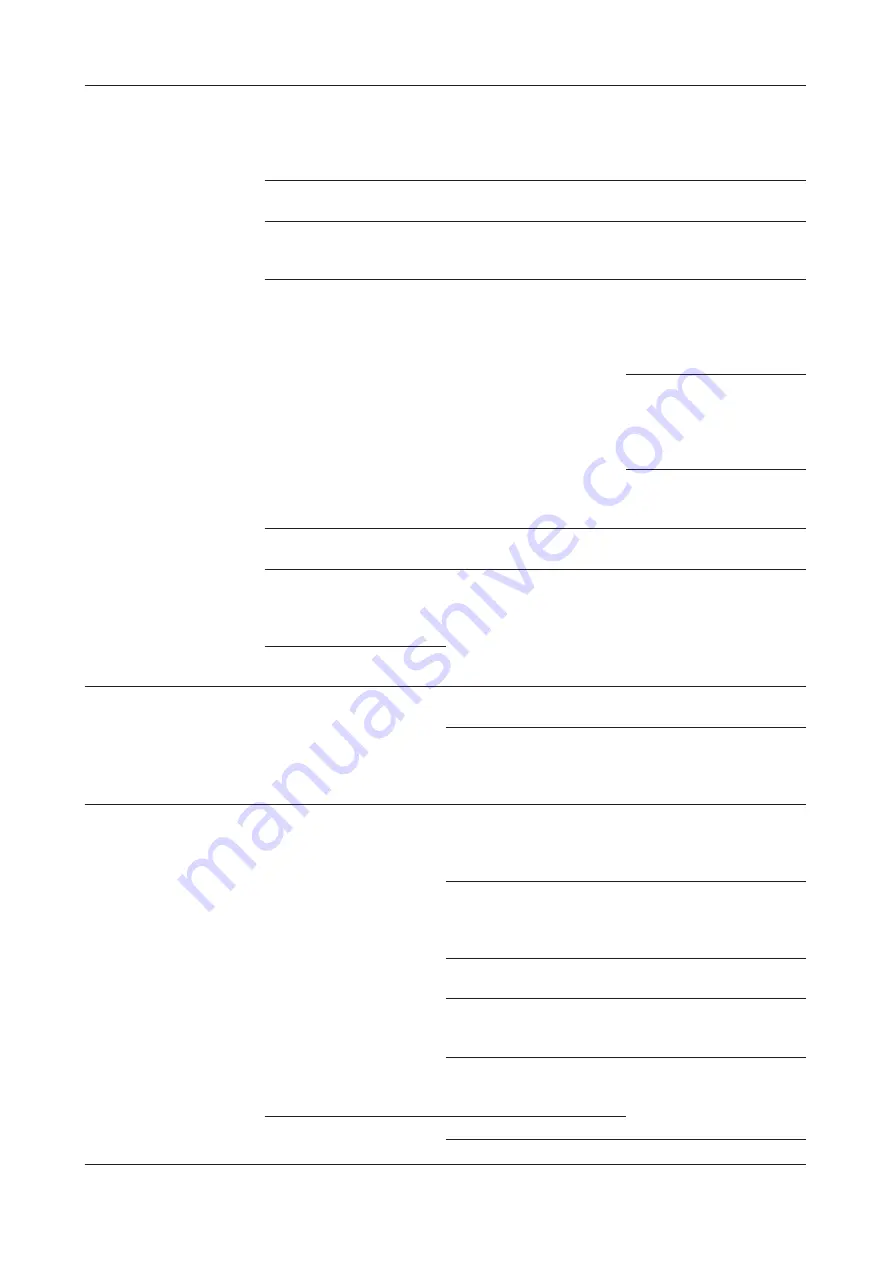
13
Forks not moving in unison
The left sleeve reaches its
end position first. When the
left sleeve is at its end posi-
tion, the right one reaches
3/4 of its stroke
KOOI-REACHFORKS® have
been connected the wrong
way round
Connect the KOOI-REACH-
FORKS® as indicated in the
instructions in the chapter
on ‘Assembly’
Sleeves not moving in
unison
A piston seal is leaking
Replace the piston with the
leaking seal
Left or right sleeve extends
without operating lever be-
ing used.
Air in hydraulic system
Follow step 5 of the chapter
on ‘Assembly’
Difference in stroke length
becomes increasingly great
and one sleeve fails to
retract fully.
Pistons cannot return to
their rear position meaning
the KOOI-REACHFORKS®
hydraulic system cannot be
flushed and reset
Slide the sleeves in fully
and operate the lever for
another 30 sec. (in the same
direction as when retract-
ing)
Check that the rear of the
sleeve(s) does not come
into contact with the car-
riage plate. If so, please
contact your supplier
Dismantle sleeves and
remove any dirt that has ac-
cumulated in the front ends.
One or both sleeves move
without being operated
Leak in the forklift’s control
valve
Inform your forklift supplier.
One sleeve remains station-
ary when retracting and
then suddenly retracts
quickly
Spring pin(s) broken
Replace the spring pin(s)
One of the sleeves fails to
retract
Difference in length be-
tween the sleeves
Stroke length difference
Piston rods are not same
length.
Please contact your sup-
plier.
Loose piston
Dismantle outer fork,
remove hydraulic set from
fork and tighten piston (100
Nm)
Difference in height be-
tween forks
One fork point hangs lower
than the other
One of the KOOI-REACH-
FORKS® has been perma-
nently deformed as a result
of overloading.
Remove KOOI-REACH-
FORKS® from carriage
immediately and contact
supplier
One of the KOOI-REACH-
FORKS® is not hanging on
the carriage plate
Hang the KOOI-REACH-
FORK® properly onto the
carriage plate (check lock-
ing mechanism)
Carriage plate is not com-
pletely horizontal
Please do contact your
forklift truck supplier.
The forks do not match
(forks belong to different
sets)
Check serial Nºs.
Wear strips on one KOOI-
REACHFORK® are more
worn than the other
Replace wear strips
Excessive play between
fork blade and sleeve
Wear strips worn out
Sleeves worn out
Replace sleeves