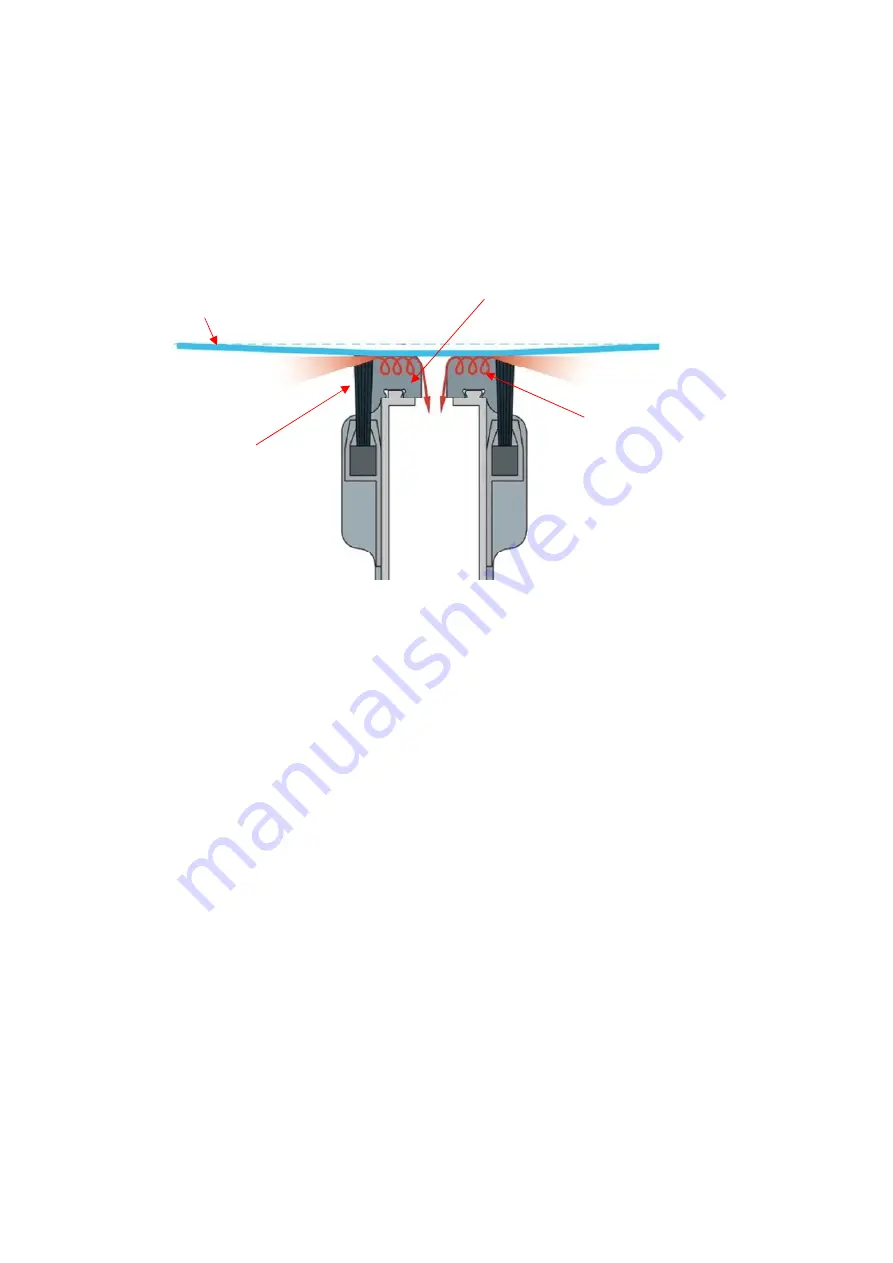
AHU-CL1 Manual
Page
59
of
102
Turbulent Air
The VacClean pulls air in between the face plate of the VacClean and the web material requiring
cleaning. This creates a turbulence that loosens the contamination on the web and allows it to be
vacuumed off the web.
Installation
The installation is covered previously in the beginning of the manual in the installation pages.
VacClean specific Installation
The general VacClean installation is covered at the start of the manual, however important areas to
check when installing are:
•
Face Plate Level
•
Brush height
•
Multi-web size fingers
•
Bars
All components of the VacClean are set before shipping but rough handling can cause damage and
movement of some components, these should be visually checked to ensure correct cleaning of the
web.
Inspecting face plate level
The face plate level can be easily visually checked that it has not come loose or “popped up”. The face
plate mounts on the VacClean through tensioning screws which can be released if the face plate needs
to be levelled. The VacClean’s use of vacuum pressure means there can be a large tolerance of 2mm
Face Plate
Web Material
Brush
Turbulent Air
Figure 88 - Removal of Contamination through Turbulent air
Summary of Contents for AHU-CL1
Page 63: ...AHU CL1 Manual Page 63 of 102 924 bar Technical Drawing...
Page 68: ...AHU CL1 Manual Page 68 of 102 Spare Part Location Drawing...
Page 69: ...AHU CL1 Manual Page 69 of 102...
Page 82: ...AHU CL1 Manual Page 82 of 102 Technical Drawings...
Page 83: ...AHU CL1 Manual Page 83 of 102...
Page 84: ...AHU CL1 Manual Page 84 of 102...
Page 85: ...AHU CL1 Manual Page 85 of 102...
Page 86: ...AHU CL1 Manual Page 86 of 102...
Page 87: ...AHU CL1 Manual Page 87 of 102...
Page 88: ...AHU CL1 Manual Page 88 of 102...
Page 89: ...AHU CL1 Manual Page 89 of 102...
Page 90: ...AHU CL1 Manual Page 90 of 102...
Page 91: ...AHU CL1 Manual Page 91 of 102 Label Locations Drawing...
Page 92: ...AHU CL1 Manual Page 92 of 102...
Page 93: ...AHU CL1 Manual Page 93 of 102...
Page 94: ...AHU CL1 Manual Page 94 of 102...
Page 95: ...AHU CL1 Manual Page 95 of 102...
Page 96: ...AHU CL1 Manual Page 96 of 102...
Page 97: ...AHU CL1 Manual Page 97 of 102...
Page 98: ...AHU CL1 Manual Page 98 of 102 Wiring Diagram...
Page 99: ...AHU CL1 Manual Page 99 of 102 CUL Certification...
Page 100: ...AHU CL1 Manual Page 100 of 102...
Page 101: ...AHU CL1 Manual Page 101 of 102...
Page 102: ...AHU CL1 Manual Page 102 of 102...