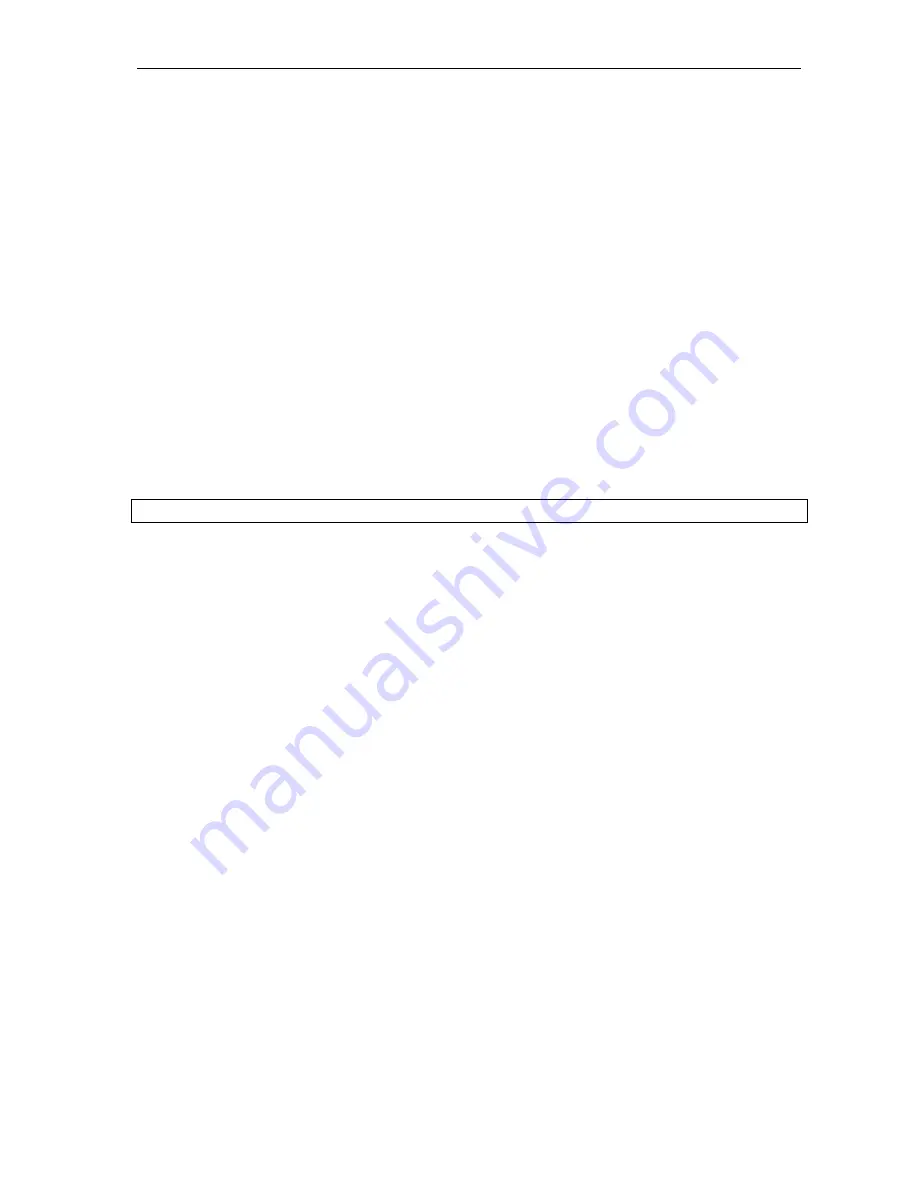
ENGLISH
20
1.
Connect the earth clamp to the metal to be welded. Scrape the surface a little to ensure good
electrical contact.
2.
Set the welding input and feed speed of the welding electrode according to the type of material,
thickness and size of welding electrode.
3.
Connect the welding machine to the mains supply and start the machine.
4.
Cut off the welding electrode to a length of 3 mm from the welding tip.
5.
Place the tip 6 mm from the starting point of the weld.
6.
Hold the welding shield in place.
7.
Press in the trigger. Move the tip slowly when the welding arc is formed.
8.
If the welding arc produces a buzzing noise and a lump forms at the end of the welding electrode,
the feed speed is too low and must be increased. If the electrode produces an abnormal noise, a
feeling that the electrode "drags" against the workpiece and that the welding produces too much
spatter, this means that the feed speed is too high. A steady, crackling noise is heard when the
feed speed is correctly adjusted. If the weld joint becomes porous, the gas flow is insufficient and
must be increased.
9.
The welding machine can be adjusted to deliver different output currents during a work cycle that
are specified as a percentage, see type plate on the casing. The percentage indicates the welding
time during a 10 minute period. A work cycle of, for example, 60% means that the welding time is 6
minutes with a subsequent rest period of 4 minutes. If the welding machine is used for a longer
period of time some components may overheat and this can trip the thermal protection. It will then
not be possible to use the welding machine. This is indicated by a yellow control lamp on the front
panel. If this happens on a welding machine without fan cooling, the machine must be switched off
to cool down. The thermal protection resets automatically when the welding machine has cooled.
Fan-cooled welding machines cool much faster if you switch off the machine and allow the fan to
run.
MAINTENANCE
Electrical repairs must only be carried out by authorised personnel.
Covers must not be dismantled by unauthorised personnel and the welding machine must not be
used with any of the covers dismantled.
Always disconnect the welding machine from the mains supply before maintenance, repairs or
other servicing.
If the power cord needs to be replaced, the cable conductors must be connected inside the welding
machine so that they do not come into contact with parts that get hot during normal operation, e.g.
transformer, choke, rectifier or circuit board. This must only be carried out by an authorised service
centre.
Welding cables
Regularly check the connections on the welding cables.
Welding tip
The tip and casing must be regularly cleaned to remove spatter that can affect the feeding of the
welding electrode. An accumulation of spatter can be counteracted by spraying an antispatter
agent on the tip and casing.
The tip must be regularly replaced to ensure good electrical contact between the tip and welding
electrode.
Avoid bending or twisting the welding tip. Never use it to move the welding machine.
Blow clean the casing with clean, dry air at regular intervals to ensure that the welding electrode
passes freely through the tip. The casing should be replaced if the welding electrode still does not
run freely.