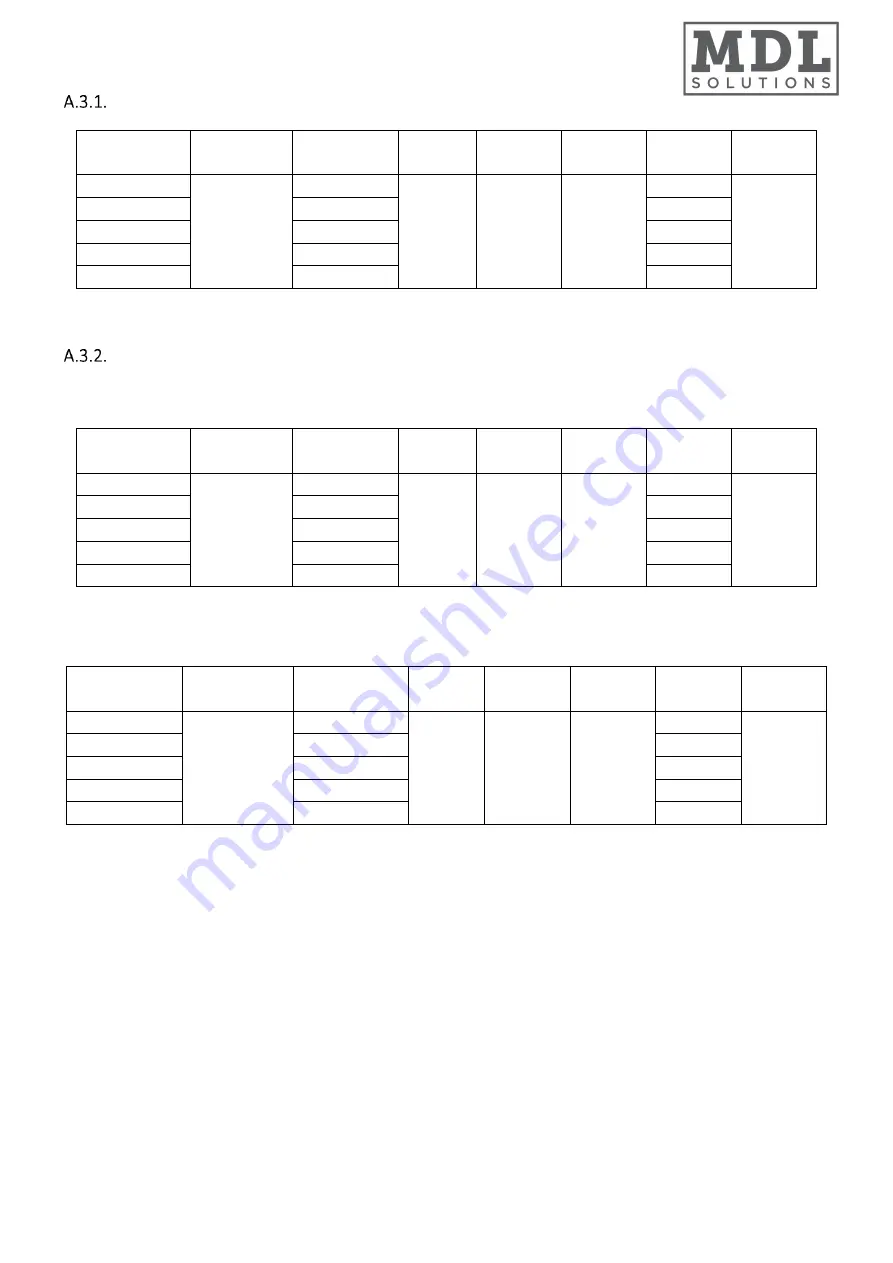
Page 8 of 53
SK2017 AHRI PFWSL-V/P-AECM-001
A.3.
Coil Data
2-Pipe Systems
Model
Fin height
Fin Length
Fins per
Inch
No. of
Rows
Fin width
No. of
Circuits
Tube Ø
PFWSL-01
11-13/16
11-7/8
15.0
2
1-3/4
2
3/8
PFWSL-02
19-3/4
2
PFWSL-03
27-5/8
2
PFWSL-04
35-1/2
3
PFWSL-05
43-3/8
3
4-Pipe Systems
Cooling Coil
Model
Fin height
Fin Length
Fins per
Inch
No. of
Rows
Fin width
No. of
Circuits
Tube Ø
PFWSL-01
11-9/16
11-7/8
16.5
2
1
2
1/4
PFWSL-02
19-3/4
2
PFWSL-03
27-5/8
3
PFWSL-04
35-1/2
4
PFWSL-05
43-3/8
4
Heating Coil
Model
Fin height
Fin Length
Fins per
Inch
No. of
Rows
Fin width
No. of
Circuits
Tube Ø
PFWSL-01
11-9/16
11-7/8
16.5
1
1/2
1
1/4
PFWSL-02
19-3/4
1
PFWSL-03
27-5/8
1
PFWSL-04
35-1/2
2
PFWSL-05
43-3/8
2
(All dimensions are approximate within 1/16 of an inch of those indicated.)