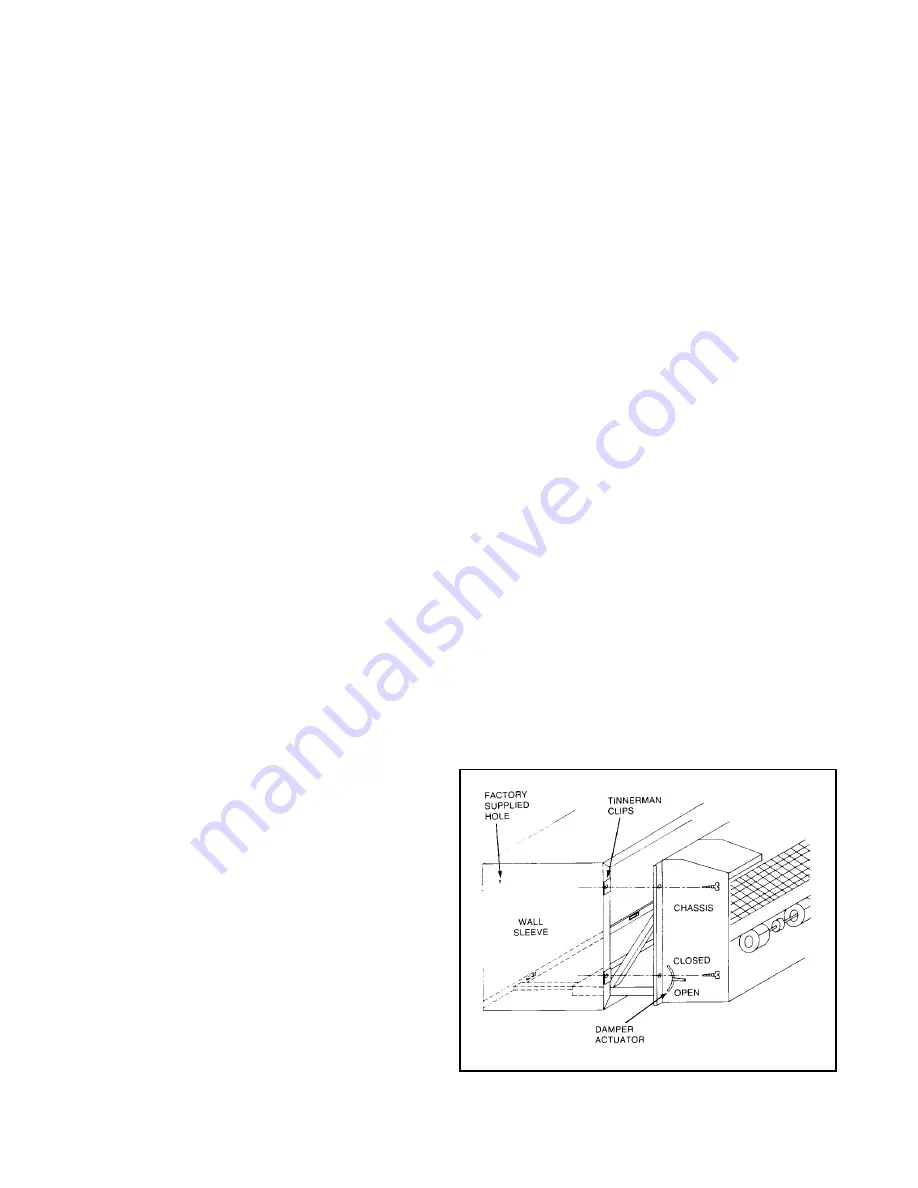
IM 368 / Page 10 of 20 (Rev 11/03)
Installation of Louvers
1. Remove louver and mounting hardware from the shipping
carton.
2. Remove temporary cardboard weather panel from cabinet/
wall sleeve.
3. Make a temporary handle by looping a piece of flexible wire
or heavy cord through the louver. This enables the installer to
keep a firm grasp on the louver when installing from inside
the room.
4. Push the louver through the opening at the rear of the wall
box, then pull the louver back to the wall sleeve flange so that
the louver studs pass through the holes in the flange.
5. Attach washers and nuts and secure louver in place.
6. If the heating/cooling chassis is not to be immediately installed,
replace the weather panel.
Installation of Chassis
Figure 16. Chassis Installation
Proper installation of the heating/cooling chassis is extremely
important to the proper operation of the unit. Whether the wall
sleeve has been separately shipped or shipped with the chassis,
proper installation is as follows:
1. Remove shipping carton and inspect for any shipping
damage. Report any found to the carrier.
2. Save shipping carton to cover installed conditioner until
construction is complete.
3. Check nameplate data on chassis to insure that the correct
jobsite distribution has been made with respect to heating/
cooling capacities. Generally, corner rooms require larger
capacities.
4. Set front panel aside and remove air filter.
5. Remove chassis from carton by pulling evenly on substantial
portion of unit. Caution: Do not pull on evaporator fan housing
or control box.
6. If wall sleeve has been previously installed, remove temporary
cardboard weather panel.
7. If louver has not been previously installed, connect to wall
sleeve as described earlier.
8. Place Tinnerman clips on wall sleeve. Clips and mounting
screws are enclosed in a bag attached to the inside chassis
side panel.
9. Rotate fans to be sure they are free of obstruction.
10. Check all fasteners to make certain they did not loosen
during shipment. Do not loosen nuts holding down compressor;
they are factory installed.
11. Do not lubricate motors before startup. Motors are factory
lubricated. Consult “Scheduled Maintenance” section on page
12 for lubrication instructions.
12. Slide chassis into wall sleeve until firmly seated against
weather seals. Caution: Do not push on coil surface, control
box cover or fan scroll. Make sure tubing does not catch when
inserting chassis.
13. Secure the chassis in the cabinet/wall sleeve with four (4)
screws packaged with the Tinnerman clips.
14. Plug electrical cord into receptacle. Excess cord for 208V and
230V units should be coiled neatly and stored in the condi-
tioner. Attach plug/cord cover to front face of subbase on 265V.
15. Set the manual damper operator in open or closed position
as desired. On units equipped with the optional electric fresh
air damper, set the “auto/off” switch to the desired position. In
“auto,” the damper is open whenever the indoor fan motor is
running. The “auto/off” switch is located on the bottom front
face of the control box.
16. Check the “Override/Normal” dial (heat pump only) located
on the front face of the control box. For normal heat pump
operation, position the dial to “Normal.” Only the electric heater
will operate when dial is in “Override” position.
17. Set fan cycle switch (located on the lower front face of the
control box) for constant or cycling indoor fan. With the switch
in the “cycle” position, the indoor fan will shut off when the
thermostat shuts off heating or cooling.
18. Set the temperature limiting feature to the desired range of
thermostat operation.
19. Replace the air filter and front panel.
20. For hydronic units, place the disconnect switch to the “On”
position.
a. Punch the two low voltage valve wires, with Molex
connections, through the opening provided in the subbase
and connect to valve.
b. Connect short power cord from the chassis to the receptacle
in the subbase heat section.
c. Replace filter and louvered subbase front panel.
d. Relocate thermostat bulb to bracket located in the subbase.
Refer to IM 419 which is provided with the hydronic subbase.