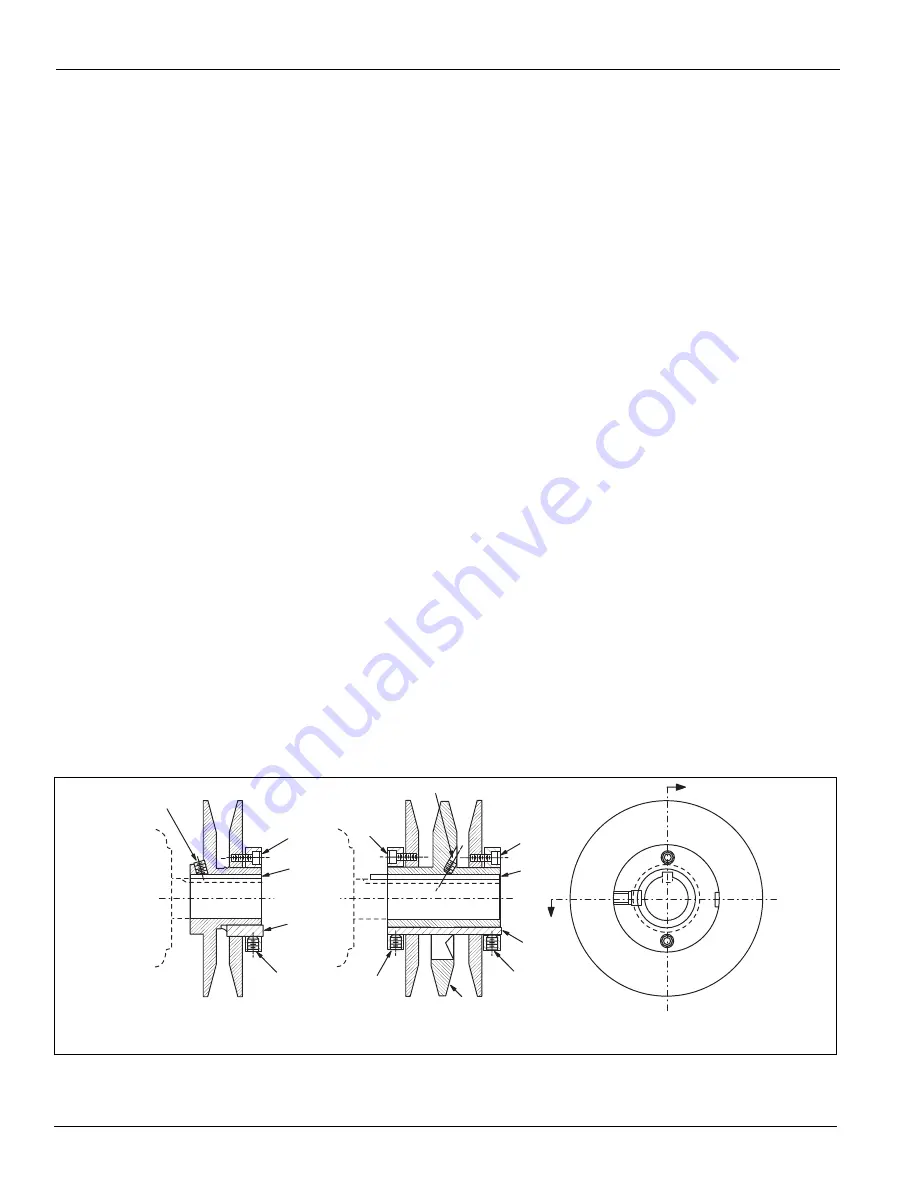
24
McQuay IM 777-2
Service and Maintenance
LVP Variable Speed Sheaves
Mounting
1
Slide sheave on motor shaft so that the side of the sheave
with setscrew
A
is next to the motor when setscrew
A
is in
the hub or barrel of the sheave.
2
When setscrew
A
is at an angle in the center flange
B
,
mount it away from the motor so that the outer locking ring
and flange can be removed to get to the setscrew.
3
To remove the flange and locking ring:
a
Loosen setscrews
D
.
b
Loosen but
do not remove
capscrews
E
.
c
Remove key
F
.
Note:
This key projects a small amount to provide a grip
for removing.
d
Rotate the flange counterclockwise until it disengages
the threads on the sheave barrel.
4
Verify that the driving and driven sheaves are in alignment
and the shafts are parallel. When aligning two-groove
sheaves, allow room between the sheave and motor to
access capscrews
E
.
5
Insert key
C
between the sheave and the shaft and tighten
setscrew
A
securely.
6
If flange and locking ring have been removed, when
replacing them make sure that the inner and outer flanges
are open from the closed position by the same amount as
the other flange. Determine this by accurately measuring
the top width of the grooves.
7
Insert key
F
.
8
Tighten setscrews
D
and capscrews
E
.
9
Put on belts and adjust belt tension.
Do not force belts
over grooves.
See “Fan Drive Belt Adjustment” on page
26.
10
Before starting the drive, ensure that all keys are in place
and all setscrews and all capscrews are tight. Check and
retighten all screws and retension belts after approximately
24 hours of service.
Adjusting
1
Slack off belt tension if belts have been installed.
2
Loosen setscrews
D
.
3
Loosen but
do not remove
capscrews
E
.
4
Remove key
F
.
Note:
This key projects a small amount to provide a grip
for removing.
5
Adjust pitch diameter by opening or closing the movable
flanges by half or full turns.
Note:
Two-groove sheaves are supplied with both grooves
set at the same pitch diameter.
To provide the same pitch diameter for satisfactory
operation, move both movable flanges the same number of
turns. Do not open sheaves more than five turns for
A
belts
or six turns for
B
belts.
6
Replace key
F
.
7
Tighten setscrews
D
and capscrews
E.
8
If belts have been installed, readjust belt tension. If belts
have not been installed, install them and adjust belt tension.
Do not force belts over grooves.
See “Fan Drive Belt
Adjustment” on page 26.
9
Before starting the drive, ensure that all keys are in place
and all setscrews and all capscrews are tight. Check and
retighten all screws and retension belts after approximately
24 hours of operation.
Figure 34: LVP Type Sheave Adjustment
Section A-A
Section A-A
A
B
C
D
E
F
D
E
A
E
C
F
D
A
A