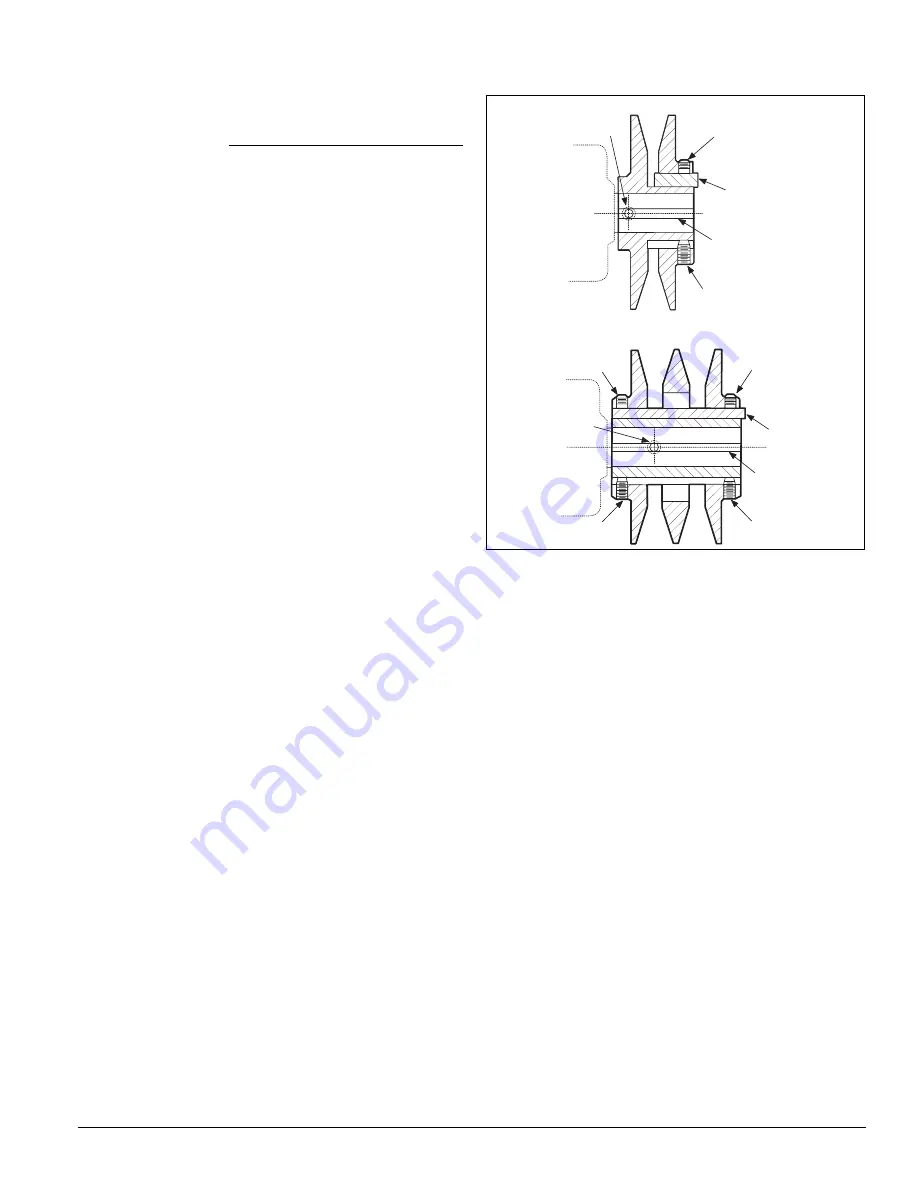
McQuay IM 777-1
21
Service and Maintenance
passes around the sheave (pitch diameter). Calculate fan speed
from the motor nameplate rpm.
VM and VP Variable Pitch Key Type Sheaves
Mounting:
1
Mount all sheaves on the motor or driving shaft with the
setscrews
A
toward the motor.
2
Verify that both driving and driven sheaves are in
alignment and that shafts are parallel.
3
Fit internal key
D
between sheave and shaft and lock
setscrew
A
securely in place.
Adjusting:
1
Loosen setscrews
B
and
C
in moving parts of sheave and
pull out external key
E
. (This key projects a small amount
to provide a grip for removing.)
2
To adjust sheave pitch diameter for desired speed, open
moving parts by half or full turns from closed position.
Do
not open more than five full turns for
A
belts or six full
turns for
B
belts.
3
Replace external key
E
and securely tighten setscrews
B
over key and setscrews
C
into keyway in fixed half of the
sheave.
4
Put on belts and adjust belt tension.
Do not force belts
over grooves
. See “Fan Drive Belt Adjustment” on page
24.
5
Make future adjustments by loosening the belt tension and
increasing or decreasing the pitch diameter of the sheave by
half or full turns as required. Readjust belt tension before
starting drive.
6
To provide the same pitch diameter, adjust both halves of
the two-groove sheaves by the same number of turns from
closed position.
7
Verify that all keys are in place and that all se screws are
tight before starting drive. Check setscrews and belt tension
after 24 hours service.
Figure 32: VP type sheave adjustment
LVP Variable Speed Sheaves
Mounting:
1
Slide sheave on motor shaft so that the side of the sheave
with setscrew
A
is next to the motor when setscrew
A
is in
the hub or barrel of the sheave.
2
When setscrew
A
is at an angle in the center flange
B
,
mount it away from the motor so that the outer locking ring
and flange can be removed to get to the setscrew.
3
To remove the flange and locking ring:
a
Loosen setscrews
D
.
b
Loosen but
do not remove
capscrews
E
.
c
Remove key
F
.
Note:
This key projects a small amount to provide a grip
for removing.
d
Rotate the flange counterclockwise until it disengages
the threads on the sheave barrel.
4
Verify that the driving and driven sheaves are in alignment
and the shafts are parallel. When aligning two-groove
sheaves, allow room between the sheave and motor to
access capscrews
E
.
5
Insert key
C
between the sheave and the shaft and tighten
setscrew
A
securely.
6
If flange and locking ring have been removed, when
replacing them make sure that the inner and outer flanges
are open from the closed position by the same amount as
Fan rpm = motor rpm ×
Measured diameter at motor sheave
Measured diameter at fan sheave
Two Groove
C
A
B
B
D
E
C
A
B
E
D
C
Single Groove
Key
E
projects
to provide a grip
for removal.
Do not operate
sheeves with flange
projecting beyond
the hub end.
Summary of Contents for Skyline IM 777-1
Page 32: ...30 McQuay IM 777 1...
Page 33: ...McQuay IM 777 1 31...
Page 34: ...32 McQuay IM 777 1...
Page 35: ......