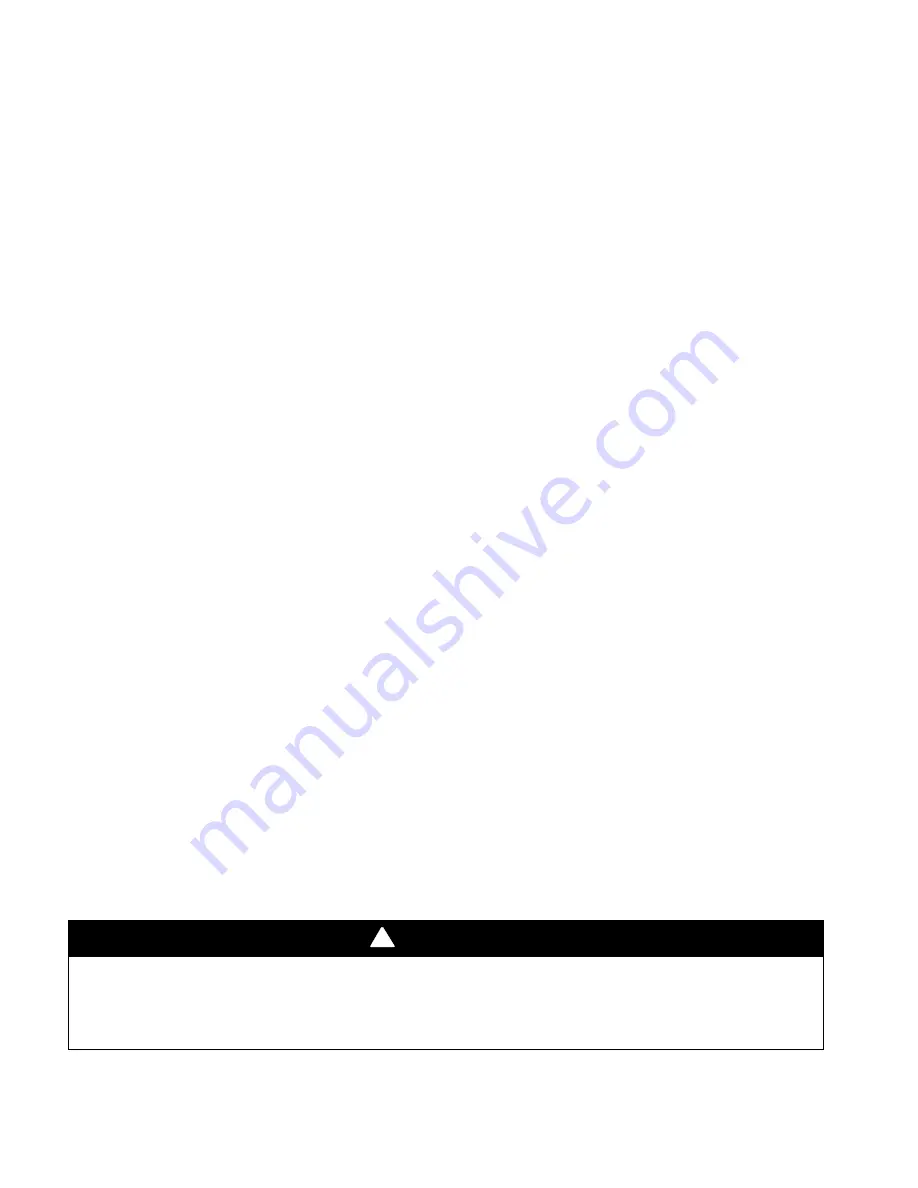
IM 422 / Page 14 of 28
Initial start-up of the Incremental
®
conditioners by
experienced personnel is usually the responsibility of the
installing contractor. This start-up consists of inspecting and
operating the equipment for all functions at the time of initial
installation, and making necessary adjustments. It also
includes demonstrating its proper operation to the owner or the
owner’s agent. Note that unless otherwise specifically agreed
to in writing, no field labor, start-up service or the like is included
in the price of the equipment. After the equipment leaves the
factory, it may become damaged or maladjusted during trans-
portation or on the job. Sometimes wires are disconnected
accidentally, or fan motors move on their bases due to rough
handling, causing fans to strike. The correction of such condi-
tions is part of the start-up.
Before Starting Equipment, Make Certain That:
1. Correct voltage has been supplied to the equipment.
2. The electrical plug from the control box has been inserted
into the receptacle.
During Start-up (Applies Only to Standard Equipment):
1. Set manual ventilation damper to OPEN or CLOSED posi-
Equipment Start-up
tion as required by owner. Set “Auto-Off” switch as re-
quired if unit is equipped with electric fresh air damper.
2. Push HIGH button to preselect fan speed. Push HEAT
button. Move thermostat to the extreme heating position
(counterclockwise). If the “Cycle/Constant” switch is placed
in the “Cycle” position, heat and indoor fan motor should
cycle on and off as the thermostat requires. Push LOW
button. Fan should change to low speed.
3. Push HIGH button to preselect fan speed. Push COOL
button. Move thermostat to the extreme cooling position
(clockwise). Compressor and indoor fan motor should
cycle on and off as the thermostat requires. Push LOW
button. Fan should change to lower speed. Outdoor fan
should be on whenever compressor operates.
4. Push FAN button. Indoor fan should operate at high or low
speed as selected. Neither heater nor compressor should
continue to operate.
5. Push OFF or STBY button. Fan should stop, and neither
heater nor compressor should continue to operate.
Incremental
®
conditioners are built to last. With proper care, the
unit should provide uninterrupted service for many years. Sched-
uled maintenance of this equipment, as described below, is the
key to the equipment’s longevity.
1. Air filters must be cleaned at regular intervals. Twice
annually may be adequate in some areas while twice monthly
may be required in others. Areas with high dirt and lint
content or heavy usage of units require more frequent filter
maintenance than those areas of relatively clean operating
or low usage conditions. Unit malfunction may occur if air
filters are not kept clean.
2. McQuay recommends that every year the chassis be re-
moved for a thorough checkup. This should be
completed as follows:
a. Unplug unit from power source.
b. Remove front panel and unplug valve from control box.
c. Vacuum heating coil to remove any accumulated dust.
d. Remove chassis from cabinet and move it to the
maintenance department. Replace with spare chassis or
weather plate.
e. Check all seals and insulation and repair as required.
f. Check all wiring and controls for hazardous conditions.
Scheduled Maintenance
g. Cover motors and control module with watertight
material and wash evaporator coil, condenser coil and
base pan using hot water and a mild soap. Do not use a
harsh detergent for it may corrode the aluminum fins.
h. Clean condensate drain and clear weep holes.
i. Dry equipment thoroughly, especially electric parts and
insulation.
j. Clean any rust spots with steel wool and paint with rust
inhibiting paint.
k. Clean insulation or replace if necessary.
l. Check all fasteners and tighten as required.
m. Clean and oil damper door and linkage.
n. All fan motors are permanently lubricated by the manu-
facturer. They do not require further lubrication.
o. Test run chassis before re-installing or returning to spare
parts stock.
Residential and institutional cleaning compounds can cause permanent damage to the packaged terminal unit. To avoid
damage to unit controls and heat transfer surfaces, do not spray cleaning compounds onto the discharge grille, return air
opening, or unit controls. Normal cleaning can be accomplished by wiping the unit surface with a damp cloth. When using
cleaning compounds on carpets, floors or walls, turn the unit off to avoid drawing potentially damaging vapors into the
package terminal unit.
!
WARNING
Summary of Contents for Incremental PDNC Series
Page 21: ...IM 422 Page 21 of 28 Wiring Diagram PDNS PDNC Control Remote Thermostat N O Valve 24V...
Page 22: ...IM 422 Page 22 of 28 Wiring Diagram PDNS PDNC Control Unit Mounted N O Valve 24V...
Page 23: ...IM 422 Page 23 of 28 Wiring Diagram PDNS PDNC Chassis Wiring...
Page 24: ...IM 422 Page 24 of 28 Wiring Diagram PDNS PDNC Control Remote Thermostat N C Valve 24V...