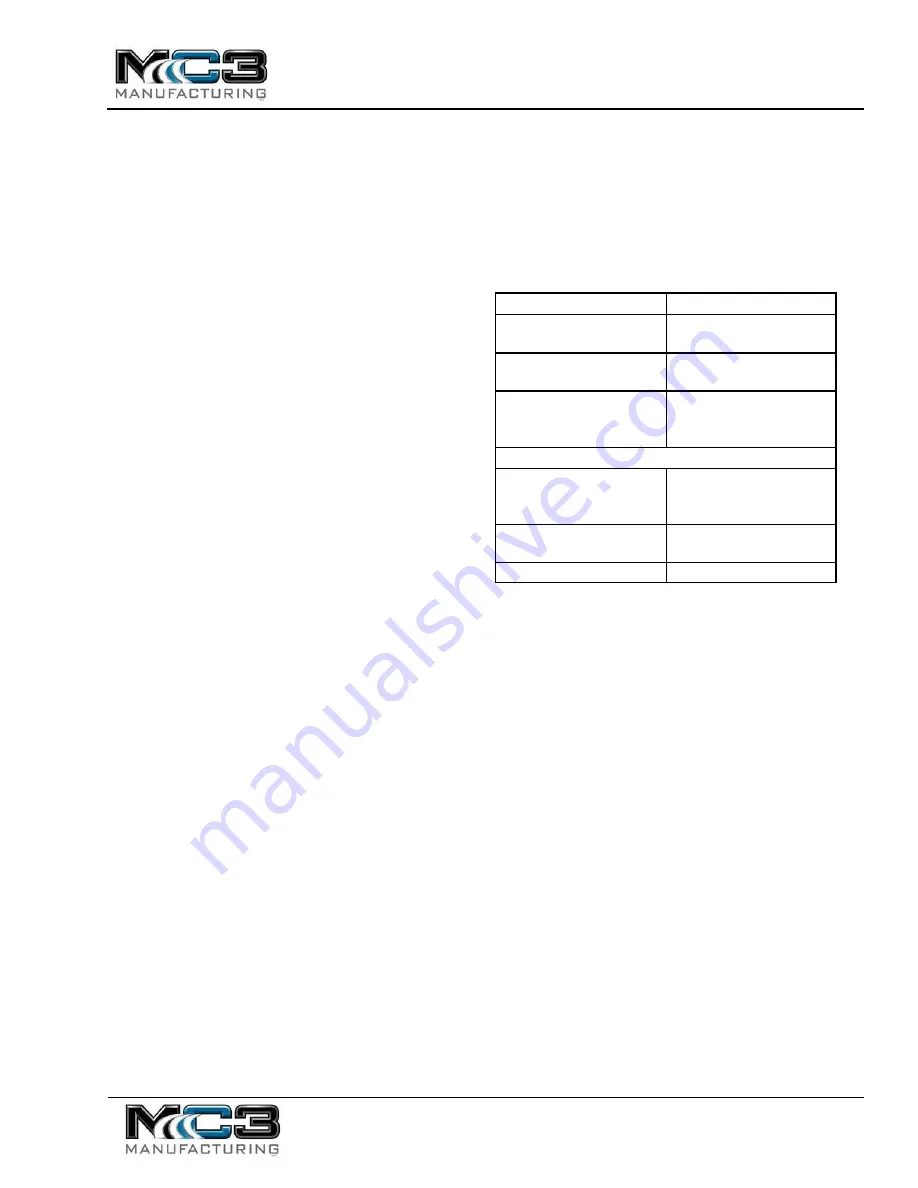
CDLR Conveyor
Operation and Maintenance Manual
Rev. 0
2021-01-26
7
Routine Maintenance
Roller Care
1.
Check chain tension to be certain the slack span
has an approximate 2% mid-span movement
a)
If the chain is too tight or vise-versa, adjust
the links to adjust the slack.
Note:
Excess loads may cause increased lacing and belt
wear as well as reducing overall belt life.
Motors
1.
Cleaning - All motors should be kept free of dirt
and grease accumulations. Open motors should
be periodically vacuumed to remove dust and
dirt from the windings.
2.
Ventilation - For best results motors should be
operated in an area where adequate ventilation
is available.
3.
Temperature - Most of the current smooth
body, T.E.N.V. and T.E.F.C. motors run hot to the
touch. As long as maximum ambient
temperatures are not exceeded and the
amperage draw is within the allowable range
there should not be a problem.
Note:
The temperature and amperage limits can be
found on the motor name plate.
4.
Lubrication - Most electric motors are
lubricated for life and under normal operating
conditions require no more lubrication. Under
severe conditions where additional lubrication
is required use the following chart as a guide.
See Fig. 1
Condition
Lubricating Frequency
Normal 8 hr Day - Light
Loads
2-3 Years
Heavy 24 hr Day - Heavy
1 Year
Loads - Dirty Conditions
Extreme - Shock Loads -
High
3-6 Months
Temperature
Typical Lubricants
Chevron Oil Co. - SRI #2
Gulf Refining Co. -
Precision
#2 or #3
Shell Oil Co. - Alvania #2,
Mobil Oil Co. - Mobilux
Dolium R
Grease #2
Texaco Inc. - Premium RB Sinclair Refining Co. - AF #2
Fig. 1
Note:
The chart above is based on motors with
grease lubricated bearings, running at speeds
of 1750 RPM or less and operating within an
ambient temperature range of between 0°F
to 120°F (-18°C to 49°C).
Gear Reducers
1.
Ventilation - During normal operation gear
reducers build up heat and pressure and must
be vented to protect the seals and gears.
2.
Cleaning - After approximately two to three
weeks of operation the reducer must be
drained, flushed out and refilled to the correct
level with fresh oil. This is done to remove any
brass particles created during the normal wear-
in period of the worm gear. From then on the oil
should be changed every 2500 hours of
operation or every 6 months, whichever comes
first.