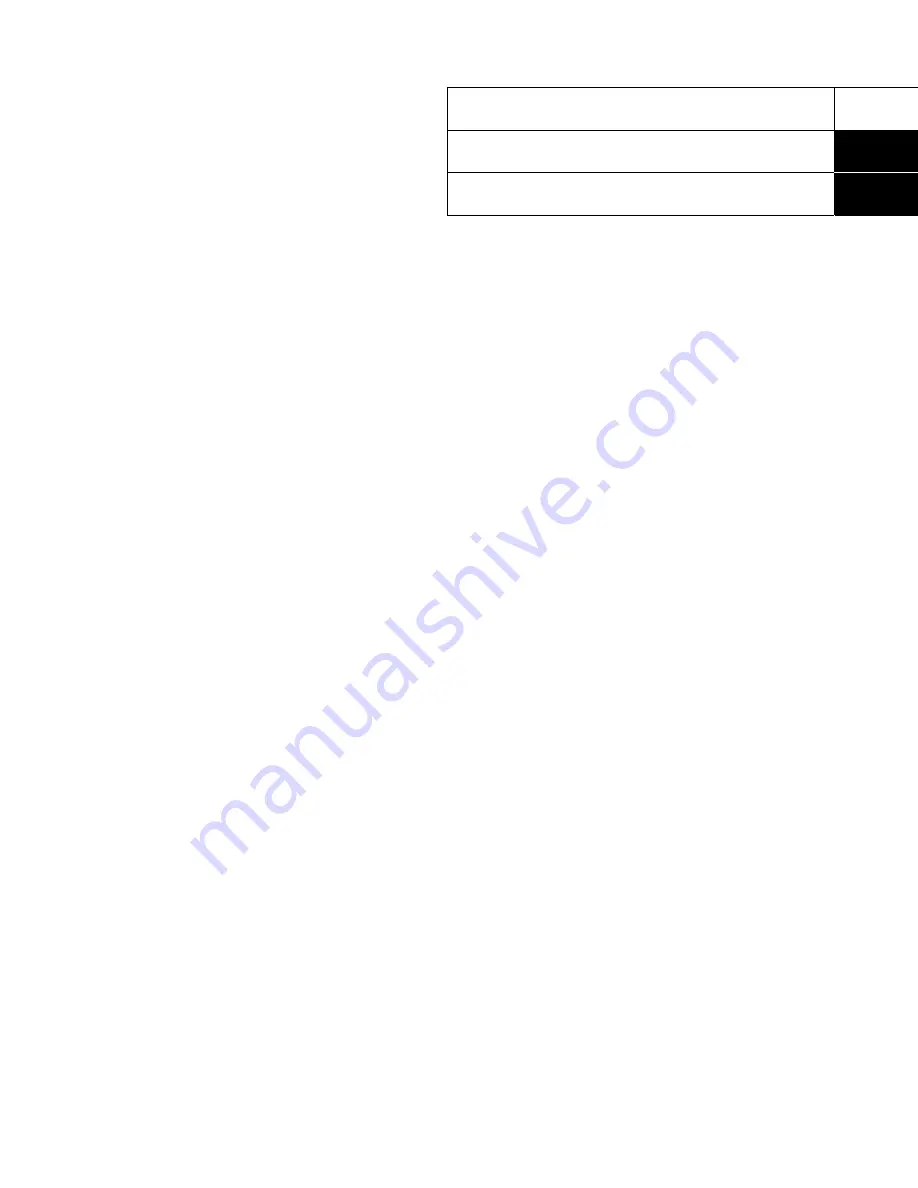
Title
Section
GENERAL INFORMATION
00
ENGINE
01
CONTENTS
Engine
Workshop
Manual
LF
L3
FOREWORD
This manual explains the service points for
the above-indicated automotive system.
This manual covers all models with the
above-indicated automotive system, not any
one specific model.
In order to do these procedures safely,
quickly, and correctly, you must first read
this manual and any other relevant service
materials carefully.
All the contents of this manual, including
drawings and specifications, are the latest
available at the time of printing.
As modifications affecting repair or
maintenance occur, relevant information
supplementary to this volume will be made
available at Mazda dealers. This manual
should be kept up-to-date.
Mazda Motor Corporation reserves the right
to alter the specifications and contents of
this manual without obligation or advance
notice.
All rights reserved. No part of this book may
be reproduced or used in any form or by any
means, electronic or mechanical—including
photocopying and recording and the use of
any kind of information storage and retrieval
system—without permission in writing.
Mazda Motor Corporation
HIROSHIMA, JAPAN
©
2005 Mazda Motor Corporation
PRINTED IN U.S.A., AUGUST 2005
Form No. 1866–1U–05H
Part No. 9999–95–LFL3–05
Summary of Contents for 2006-2008 RX7 Engine
Page 2: ......
Page 60: ...SERVICE TOOLS 01 60 2 End Of Sie 1 49 G011 201 2 Attachment...