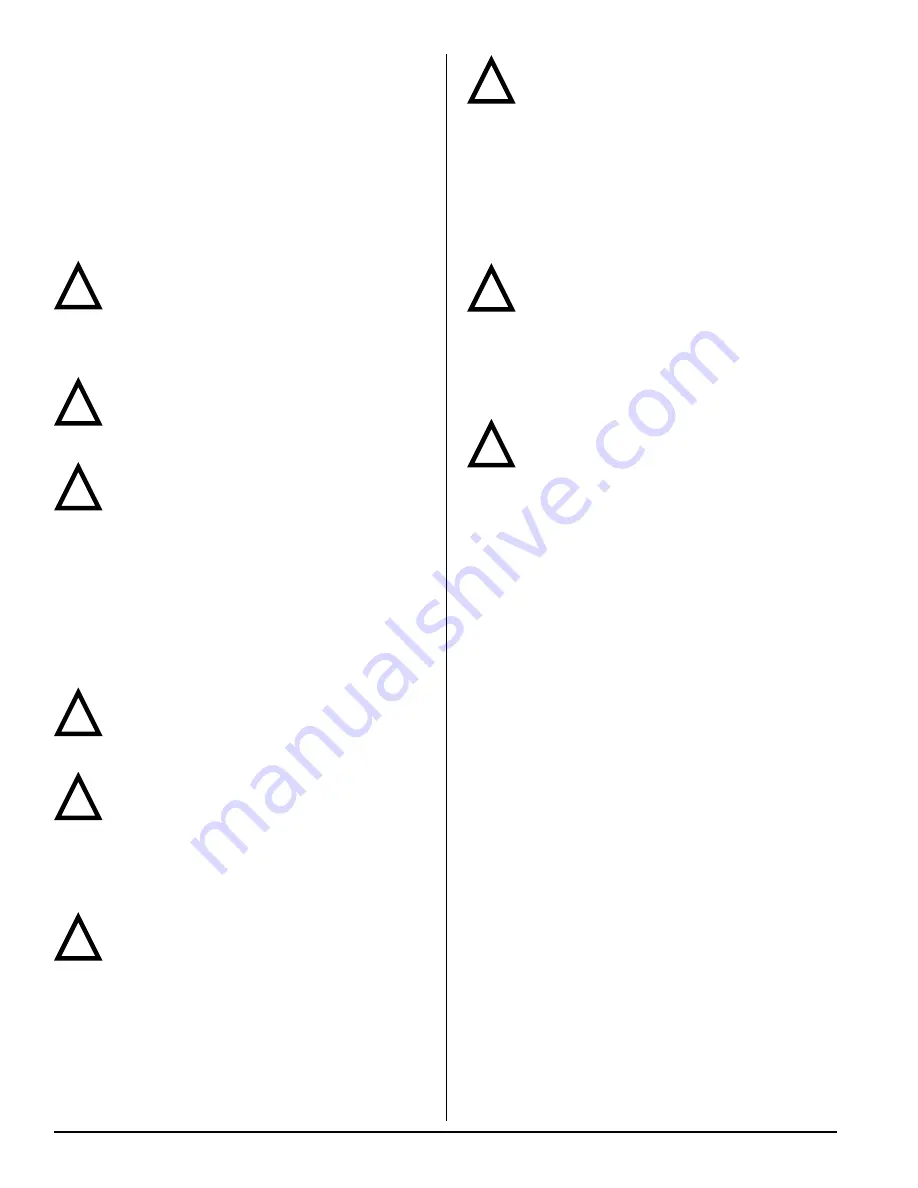
26
Maytag Co.
113413-1
Routine Maintenance__________________
Cleaning
A program and/or schedule should be established for
periodic inspection, cleaning, and removal of lint from various
areas of the dryer, as well as throughout the ductwork system.
The frequency of cleaning can best be determined from
experience at each location. Maximum operating efficiency
is dependent upon proper airflow. The accumulation of lint
can restrict this airflow. If the guidelines in this section are
met, the dryer will provide many years of efficient, trouble
free, and most importantly, safe operation.
Warning
Lint from most fabrics is highly combustible. The
accumulation of lint can create a potential fire
hazard. Keep dryer area clear and free from combustible
materials, gasoline, and other flammable vapors and
liquids.
Note
Suggested time intervals shown are for average
usage which is considered 6 to 8 operational
(running) hours per day.
Important
Dryer produces combustible lint and must be
exhausted to the outdoors. Every 6 months,
inspect the exhaust ducting and remove any lint buildup.
Suggested Cleaning Schedule
Every Third or Fourth Load
Clean the lint screen every third or fourth load. A clogged lint
screen will cause poor dryer performance. The lint door/
drawer is located just below the loading door of the dryer.
Open the lint door/drawer, brush the lint off the lint screen,
and remove the lint. Inspect lint screen and replace if torn.
Note
To remove the lint drawer from the dryer, pull
drawer out approximately halfway. Press the lint
door/drawer stop downward and pull the drawer out.
Important
The frequency of cleaning the lint screen can best
be determined from experience at each location.
Weekly
Clean lint accumulation from lint chamber, thermostat, and
microprocessor temperature sensor area.
Warning
To avoid the hazard of electrical shock,
discontinue electrical supply to the dryer.
Steam Dryers
Clean the steam coil fins. It is suggested that compressed
air and a vacuum cleaner with brush attachment be used.
Warning
When cleaning steam coil fins, be careful not to
bend the fins. If fins are bent, straighten by using
a fin comb, which is available from local air conditioning
supply houses.
90 Days
Remove lint from gas valve burner area with a dusting brush
or vacuum cleaner attachment.
Clean any lint accumulation in and around the motor(s) casing
opening.
Note
To prevent damage, avoid cleaning and/or
touching ignitor/flame-probe assembly.
Every 6 Months
Inspect and remove lint accumulation in customer furnished
exhaust ductwork system and from dryer’s internal exhaust
ducting.
Note
The accumulation of lint in the exhaust ductwork
can create a potential fire hazard.
Do not obstruct the flow of combustion and ventilation air.
Check back draft dampers in the exhaust ductwork.
Inspect and remove any lint accumulation, which can
cause the damper to bind or stick.
A back draft damper that is sticking partially closed can
result in slow drying and shutdown of heat circuit safety
switches or thermostats.
When cleaning the dryer cabinet(s), avoid using harsh
abrasives. A product intended for the cleaning of
appliances is recommended.
Adjustments
7 Days After Installation
and Every 12 Months Thereafter
Inspect bolts, nuts, screws, setscrews, grounding
connections and nonpermanent gas connections (unions,
shutoff valves, and orifices). Belts should be examined.
Cracked or seriously frayed belts should be replaced.
Complete an operational check of controls and valves.
Complete an operational check of all safety devices (lint door/
drawer switch, door switches, sail switch, and hi-limit
thermostats).
!
!
!
!
!
!
!
!
!
Summary of Contents for MLG33PDAWW
Page 28: ...Part No 113413 1 06 02 05 0...