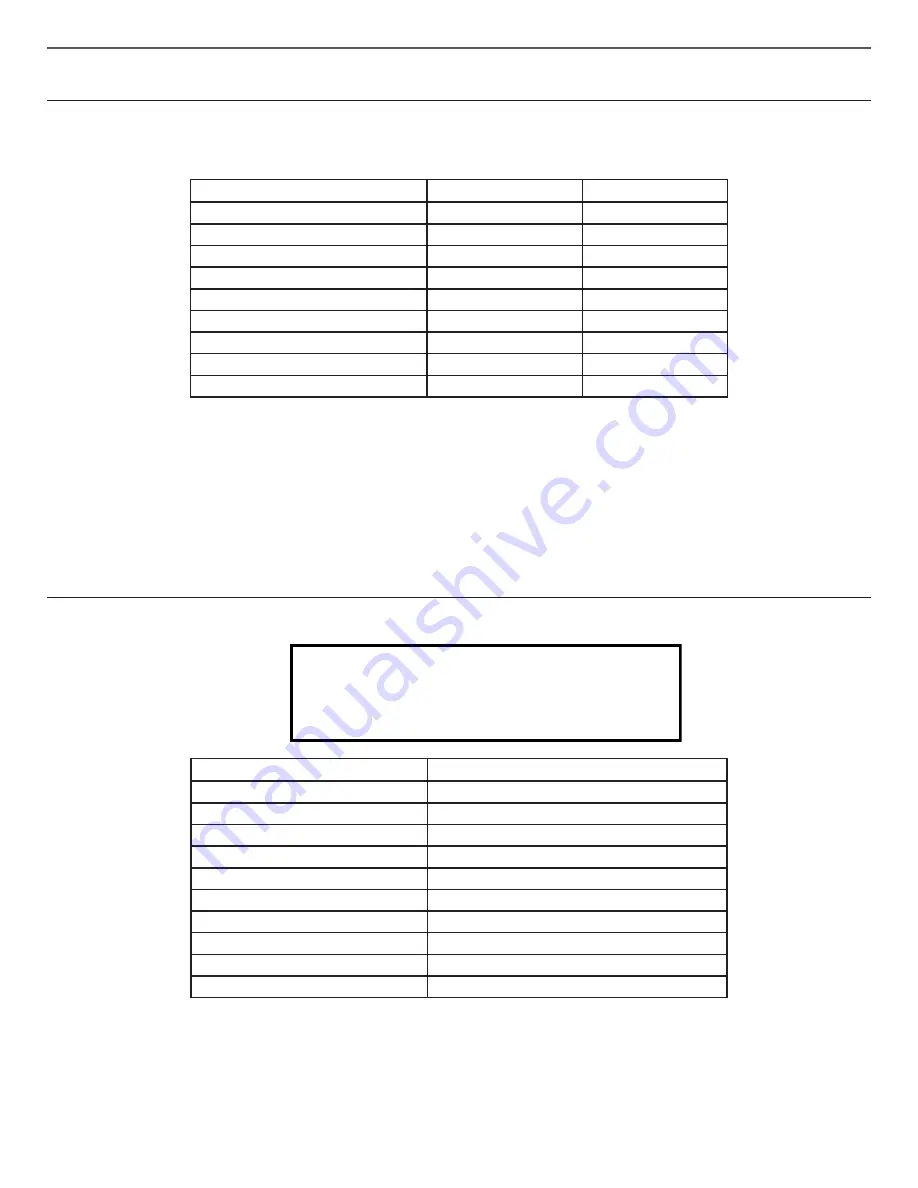
6
SYSTEM SPECIFICATIONS
QUALIFIED SYSTEM PERFORMANCE
For good performance of a Membrane consider the pressure, temperature, pH and TDS. The below Table 1 must be used for
comparison purposes only.
Specifications
U.S.
Metric
Membrane Production
1
41 - 53 gallons/day
155 - 201 (L/day)
Membrane TDS Reduction
1
96% minimum
96% minimum
System Production²
12 gallons/day
45 (L/day)
Recovery Rating²
30%
30%
Efficiency Rating²
14%
14%
TDS Reduction²
90%+ typical
90%+ typical
Drain (reject water) Flow
3-5 x product flow
3-5 x product flow
Empty Storage Tank Pre-charge
5 - 7 PSIG air
35 - 48 kPa air
Storage Tank Capacity
2
1.7 gallons
6.4 L
Table 1: Qualified System Performance
1
Industry standards measure membrane performance with no back pressure on the product water, at 65 PSIG (448 kPa) and
77 °F (25 °C). Further conditions on the above are 250 ppm TDS. Production rate and TDS reduction figures are for a new Membrane
that has been rinsed for 24 hours. The production rate of a new Membrane can decrease by 10% per year or more if the scaling and
fouling tendencies of the Feed Water increase.
2
Measured at 50 PSIG (345 kPa), 77 °F ± 2 °F, 750±40 mg/l TDS per section 6 of NSF/ANSI Standard 58. Recovery rating means the
percentage of the influent water to the membrane portion of the system that is available to the user as reverse osmosis treated water
when the system is operated without a storage tank or when the storage tank is bypassed. Efficiency rating means the percentage of the
influent water to the system that is available to the user as reverse osmosis treated water under operating conditions that approximate
typical daily usage. This reverse osmosis system contains a replaceable component critical to the efficiency of the system. Replacement
of the membrane should be with one of identical specifications, as defined by the manufacturer, to assure the same efficiency and
contaminant reduction performance.
RECOMMENDED OPERATING LIMITS FOR FEED WATER
Specifications
T.F.C. Membrane
Water Pressure
40 - 100 PSIG (280 - 690 kPa)
TDS
2000 ppm (also mg/l) max.
Temperature
40-100 °F (4-38 °C)
pH
4-11 (optimum rejection at pH 7.0 - 7.5)
Hardness
Less than 10 gpg (170 mg/l) or soften
Iron
Less than 0.1 ppm (also mg/l)
Manganese
Less than 0.05 ppm (also mg/l)
Hydrogen Sulfide
None
Chlorine
See note
Bacteria
Must be potable**
Table 2: Recommended Operating Limits
NOTE:
Chlorine will damage a T.F.C. Membrane. The Sediment/Carbon module is designed to reduce chlorine from the Feed Water.
Make sure to change the filter every 6 - 12 months or more often if the water contains more than 1 PPM chlorine.
Do not use with water that is microbiologically unsafe or
of unknown quality without adequate disinfection before
or after the system. Systems certified for cyst reduction
may be used on disinfected waters that may contain
filterable cysts.