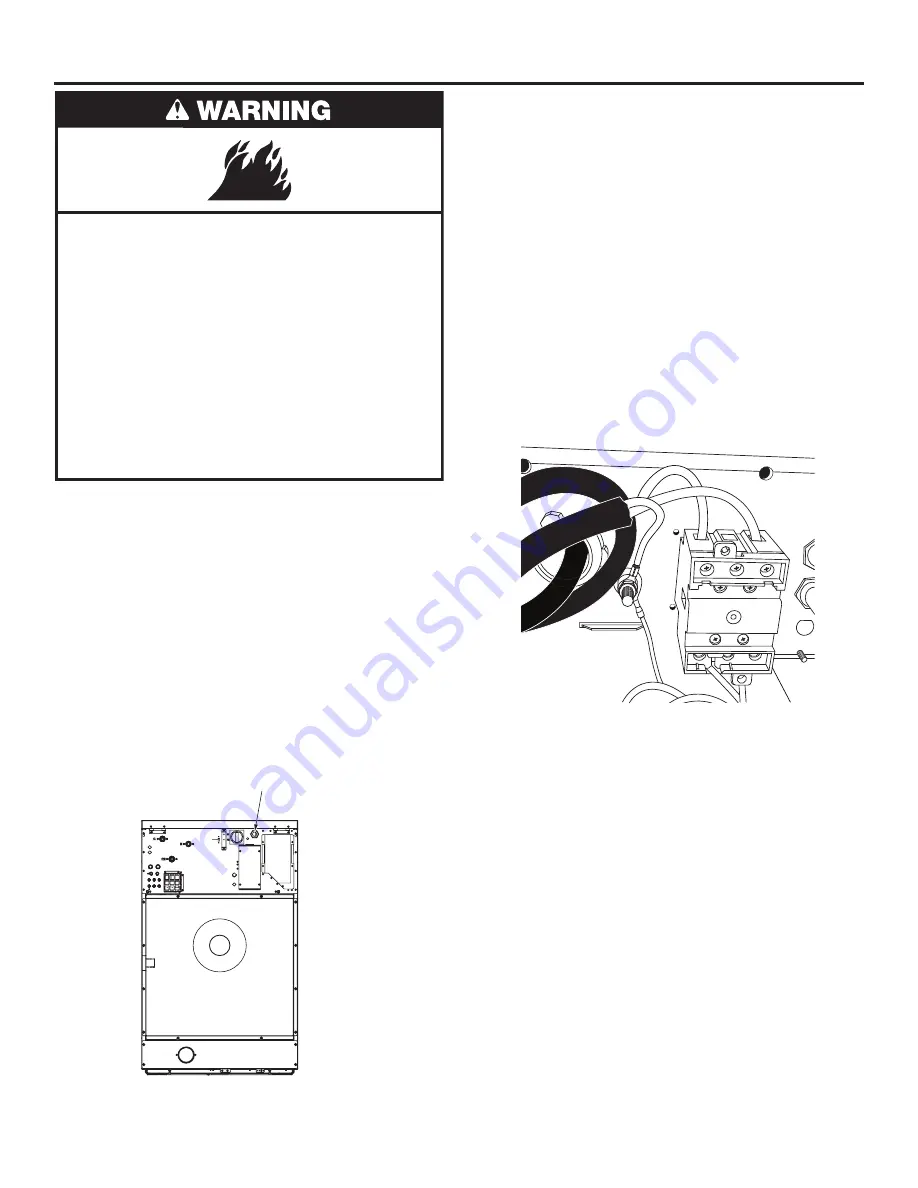
14
ELECTRICAL CONNECTION
Connection to Washer:
The washer must be electrically grounded in accordance with all
local codes or, in the absence of local codes, with the National
Electrical Code, ANSI/NFPA 70, latest edition, or Canadian
Electrical Code, CSA C22.1
Direct Wire Installation:
Power supply cable must match power supply (3-wire) and be:
͜
To access the disconnect, lift the top cover and support it
with the prop rod.
͜
Copper wire of appropriate gauge for amperage requirement
(see “Manufacturer’s Recommended Minimal Conductor
section”). Solid wire is recommended. Do not use aluminum
wire.
͜
Flexible armored cable or flexible conduit must be used
for the supply connections. Use the hole in the rear of the
washer for routing. Connection is made directly to the
disconnect switch inside the back top panel of the washer.
The Aluminum Lug for Ground is next to that disconnect
body. A Flat-head screwdriver can be used for the power
wires to the disconnect as well as the ground to the
lug. Incoming service wires are applied to the top of the
disconnect body. If the washer is single phase, (only
2 power wires) the outside positions of the disconnect
should be used (leaving the center pole empty). Tighten
down all connections including the unused position in the
single-phase service case. Leaving a small radius of slack for
the wires inside the washer, check that the cable is well held
in place.
͜
Check the rating plate on the washer. Make sure that the
supply phase and voltage match the rating of the washer.
Some locations require an autonomous power switch (I) at
the current input, with a minimum of 0.12" (3 mm) between
contacts. Fit a 300 mA, type A, immediate response
differential protection. Check your local regulations. Insert
the flexible armored cable or flexible conduit through the
hole in the rear panel. Secure the armored cable or conduit
to the rear panel. Connect the wiring per the correct
illustration.
Fire Hazard
Use appropriate gauge of solid copper wire. (See chart
in “Electrical Requirements” section).
Use a UL listed strain relief.
Disconnect power before making electrical connections.
Connect neutral wire (white) to terminal (N).
Ground wire (green or bare wire) must be connected
to ground connector (PE).
Connect remaining 3 supply wires to remaining
3 terminals (L1, L2 and L3).
Securely tighten all electrical connections.
Failure to do so can result in death, fire, or
electrical shock.
Knock out for
Electrical Connection
PE
L1
L2
Single Phase
Summary of Contents for MYR20
Page 19: ...19 NOTES ...
Page 20: ...20 NOTES ...
Page 21: ...21 NOTES ...
Page 22: ...22 NOTES ...
Page 23: ...NOTES 23 ...
Page 24: ...WFR124390H 11 21 TM 2021 Maytag All rights reserved Used under license in Canada ...