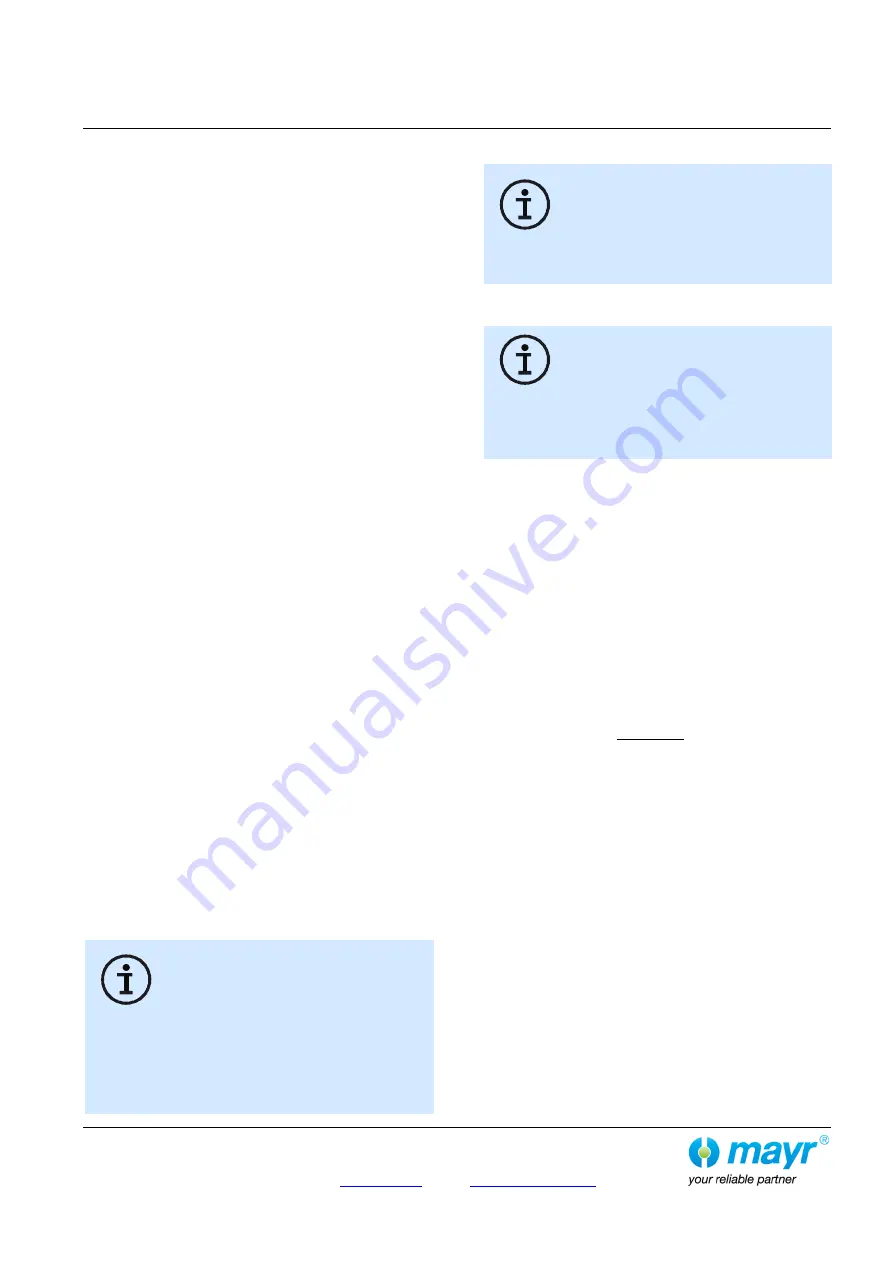
Installation and Operational Instructions for
ROBA-stop
®
-stage Type 8070. _ _ _ _ _
Sizes 8
– 200
(E102 03 000 000 4 EN)
18/11/2022 HW/GC
Chr. Mayr GmbH + Co. KG
Eichenstraße 1, D-87665 Mauerstetten, Germany
Phone: +49 8341 804-0, Fax: +49 8341 804-421
Page 10 of 17
Application
ROBA-stop
®
-stage brake for use as a holding brake with
occasional EMERGENCY STOP braking actions.
The max. permitted speed and friction work (see Technical
Data) must be observed.
Design
The ROBA-stop
®
-stage brake is a spring applied,
electromagnetically releasing dual circuit safety brake, which
applies a defined braking effect after the voltage is switched off
or after a voltage failure.
Function
ROBA-stop
®
-stage brakes are spring applied, electromagnetic
safety brakes.
Spring applied function (brake):
In de-energized condition, thrust springs press against the
armature disks (4.1 and 4.2). The rotors (6.1 and 6.2) are held
between the armature disks (4.1 and 4.2) and the intermediate
disk (5) .
The braking torque is introduced into the drive line (shaft) via the
toothings of the rotors (6.1 and 6.2) and the hub (1).
Electromagnetic function (release):
Due to the magnetic force of the coils in the coil carriers (2 and
3), the armature disks (4.1 and 4.2) are attracted against the
spring pressure to the coil carriers (2 and 3).
The brake is released and the rotors (6.1 and 6.2) with the hub
(1) can rotate freely.
Safety brakes:
The ROBA-stop
®
-stage brakes reliably and safely in the event of
a power switch-off, a power failure
or an EMERGENCY STOP.
Scope of Delivery / State of Delivery
The ROBA-stop
®
-stage brake is manufacturer-assembled ready
for installation and set to the braking torque specified on order.
The release monitoring device (9) and the wear monitoring
device (13 / dependent on Type) are mounted and set
manufacturer-side.
The following are included loose in delivery:
- Cap screws (8)
- Washers (8.1)
- Hand release (10 / must be ordered separately if required)
Please check the scope of delivery as well as the state of
delivery immediately after receiving the goods.
mayr
®
will take no responsibility for belated complaints.
Please report transport damage immediately to the deliverer.
Please report incomplete delivery and obvious defects
immediately to the manufacturer.
Adjustment
The brakes are equipped manufacturer-side with
the respective springs for the braking torque
stated on the Type tag (12). Adjustment is not
necessary. Adaptions or modifications are not
permitted as a rule. This rule also applies to the
manufacturer-side adjusted noise damping. The proximity
switches are also adjusted manufacturer-side. Despite great
care during the manufacturer-side adjustment, re-adjustment
might be necessary after installation due to transportation and
handling.
Please observe the sections Release Monitoring and Wear
Monitoring.
Noise Damping
The noise damping was set and adjusted
manufacturer-side. However, this component is
subject to aging dependent on the application
or operating conditions (torque adjustment,
switching frequency, ambient conditions,
system vibrations etc.).
Replacing the damping element is only
permitted at the
mayr
®
site of manufacture.
Installation Conditions
Dimension l
1
= 29.5 mm for Size 8,
dimension l
1
= 29 mm for Size 16,
dimension l
1
= 29.5 mm for Size 32,
dimension l
1
= 34 mm for Size 64,
dimension l
1
= 36 mm for Size 100,
dimension l
1
= 39 mm for Size 200,
must be observed (see Fig. 2, page 6).
Shaft tolerance: h6
The eccentricity of the shaft end in relation to the mounting
pitch circle must not exceed 0.2 mm.
The positional tolerance of the threads for the cap screws (8)
must not exceed 0.2 mm.
The axial run-out deviation of the screw-on surface to the
shaft must not exceed the permitted axial run-out tolerance
of
0.065 mm
acc. DIN 42955 R.
The reference diameter is the pitch circle diameter for
securement of the brakes.
Larger deviations can lead to a drop in torque, to continuous
grinding on the rotors (6.1 and 6.2) and to overheating.
Installation
The brake is delivered manufacturer-assembled including the
centered hub (1).
For additional safety, we recommend applying Loctite 243 into
the threaded holes for fastening the brake.
1.
Push the entire brake with the hub (1) over the shaft with
key (fixing holes should align with the bores in the machine
wall).
2.
Insert the cap screws (3 x Item 8) with the washers (8.1)
into the coil carrier (3) and screw evenly into the machine
wall until the brake is lying against it.
3.
Tighten the cap screws (8) all around evenly
using a
torque wrench to a tightening torque acc. Table 1
.
4.
Secure the hub using a locking ring.
Air Gap Inspection
1.
Energize the coil carrier 1 (Item 2).
2.
Check air gap “a” between the armature disk (Item 4.2 /
brake circuit 2) and the coil carrier (3), see Fig. 2. The
nominal air gap acc. Table 1 must be given.
3.
On reaching the maximum air gap acc. Table 1 due to
wear, the brake must be replaced (see section
„Maintenance” on page 16).