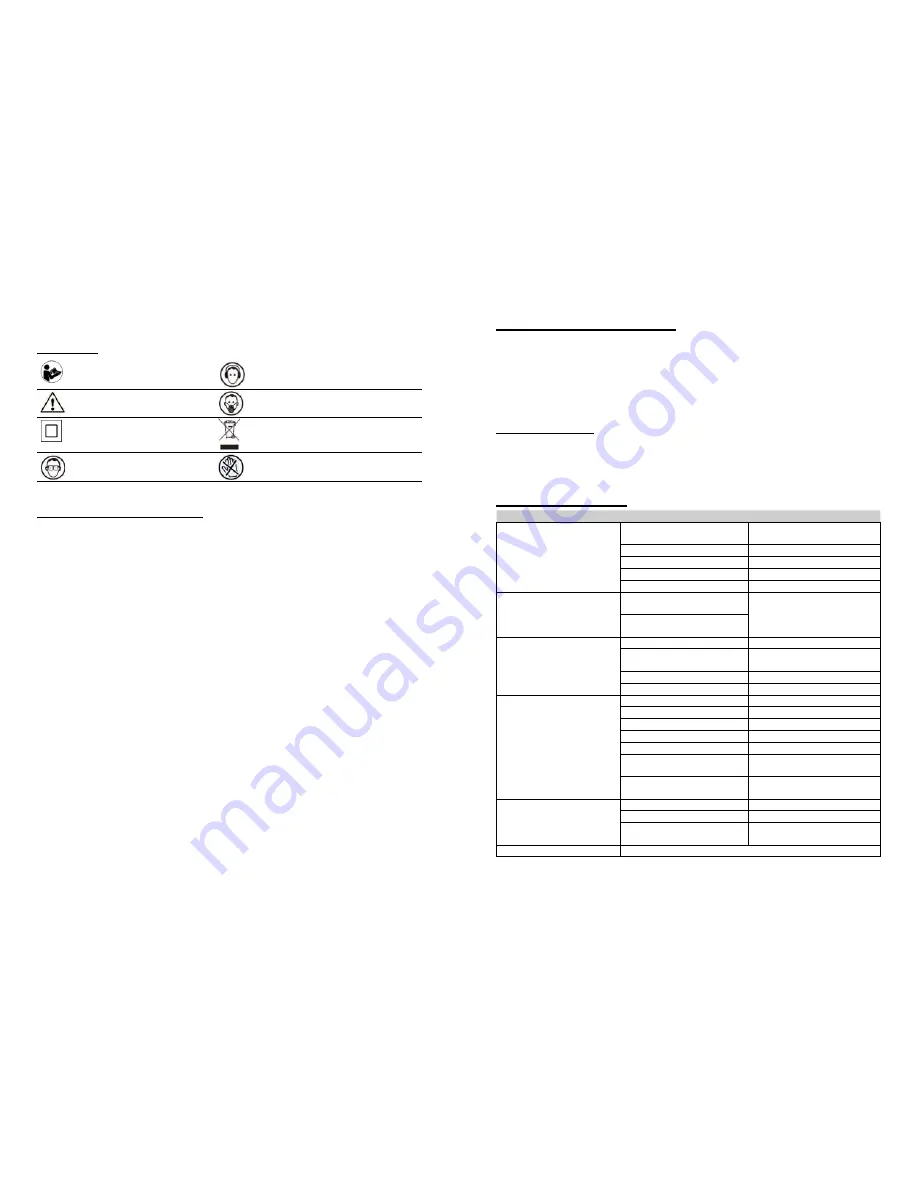
4
5
GB
GB
SYMBOLS
Read the manual
Wear ear protection
Warning
Wear dust mask
Double insulation
Do not dispose of old appliances in the
household garbage
Wear eye protection
Keep your hands and feet away from all
opening
OPERATING INSTRUCTION
PREPARATION FOR THE STARTING
(1) The place to set the compressor should be clean, dry and ventilated
(2) Keep the use voltage /- 5% of the rated
(3) Keep the oil level in the red circle leveler
(4)Recommend compressor oil use SAE30 or L-DAB 100 over 10
℃ ,
and use SAE 10 or L-DAB 68 below 10
℃
(5) Open the outlet valve, set the knob of pressure switch on (Fig.2), let the compressor run 10 minutes
with no load to ensure lubricating the moving parts before regular service
OPERATING AND ADJUSTMENT
(1)The compressor is controlled by pressure switch when normal working. It can be stopped automatically
as pressure increasing to the maximum and restart when pressure decreasing to the minimum. The rated
pressure has been adjusted when produced. Don’t change it carelessly. As soon as motor switched off the
compressed air in the discharge pipe should be released through the release valve under the switch. This is
the necessary condition for restart, or the motor will be damaged. The rated pressure can be adjusted by
turning the adjusting bolt of the switch (Fig.2).
(2)The output pressure of compressed air can be adjusted by regulating valve (Fig.2)
(3)When the compressor in running need to be stopped, only set the knob of pressure switch in position off
CAUTIONS
(1)Put the cover off first and put on the breath pipe and the air filter before the before the compressor run
(Fig.3)
(2)Never unscrew any connecting part when the tank is in pressure condition
(3)Never disassemble any electrical part before disconnecting the plug
(4)Never adjust the safety valve carelessly
(5)Never use the compressor in place where voltage is too low or too high
(6)Never use electrical wire more than 5m long with less than the section show in table 1
(7)Never disconnect the plug to stop compressor, set the switch knob in position off instead
(8)If the release valve doesn’t work as motor stopped, find the cause immediately so as not to damage
motor
(9)Lubricating oil must be clean, oil level should be kept in the red circle of the leveler
(10)Disconnect the plug to cut off power supply and open the outlet valve
MAINTENANCE
(1)Clean crankcase and renew lubricating oil after the first 10 working hours
(2)Clean the oil level after every 20 working hours, and replenish if necessary (Fig.4)
(3)Open drain cock under the tank to exhaust condensate after every 60 working hours
(4)Clean crankcase and renew the oil, clean air filter and safety valve and pressure gauge.
CLEANING AND MAINTANCE
Before any work on the machine itself, pull the mains plug. For safe and proper working, always keep the
machine and ventilation slots clean. In extreme working conditions, conductive dust can accumulate in
the interior of the machine when working with metal. The protective insulation of the machine can be
degraded. The use of a stationary extraction system is recommended in such cases as well as frequently
blowing out the ventilation slots and installing a residual current device (RCD). Please store and handle
the accessory(-ies) carefully. If the machine should fail despite the care taken in manufacturing and testing
procedures, repair should be carried out by an after-sales service centre for Maxpro power tools.
ENVIRONMENT
Do not dispose of electric tools, accessories and packaging together with household waste material -
in observance of European Directive 2002/96/EC on waste of electric and electronic equipment and its
implementation in accordance with national law, electric tools that have reached the end of their life must
be collected separately and returned to an environmentally compatible recycling facility.
TROUBLE SHOOTING
Fault Symptom
Possible Cause
Troubleshooting
Mortor unable running Running
too slow, or or Getting hot
( 1 ) Fa u l t i n l i n e , o r vo l ta ge
insufficient
(1)
Check the line
(2)Power wire too thin or too long (2)Replace the wire
(3) Fault in pressure switch
(3)Repair or replace
(4)Fault in motor
(4)Repair or replace
(5)Sticking of main compressor
(5)Check and repair
Sticking of main compressor
(1)Moving parts burnt due to the
oil insufficient
C h e c k c r a n k s h a f t , b e a r i n g ,
connecting rod, piston, piton ring,
etc. and replace if necessary
(2)Moving parts damaged, or stuck
by foreign body
Tarrible shake Or abnormal noise (1)Connecting part loosed
(1)Check and retighten
(2)Foreign body got into main
compressor
(2)Check and clean away
(3)Piston knocking valve seat
(3)Replace with thicker paper gasket
(4)Moving parts seriously worn
(4)Repair or replace
Pressure insufficient or discharge
capacity decreased
(1)Mortor running too slow
(1)Check and remedy
(2)Air filter choked up
(2)Clean or replace the cartridge
(3)Leakage of safety valve
(3)Check and adjust
(4)Leakage of discharge pipe
(4)Check and repair
(5)Sealing gasket damaged
(5)Check and replace
(6)Valve plate damaged, carbon
buildup or stuck
(6)Replace and clean
(7)Piston ring and cylinder worn of
damaged
(7)Repair or replace
T h e o i l C o n s u m p t i o n t o o
excessive
(1)Oil level too high
(1)Keep the level within set range
(2)Breath pipe choked up
(2)Check and clean
(3)Piston ring and cylinder worn of
damaged
(3)Repain or replace
Spare parts list and drawing
Please download files on
www.maxpro-tools.com