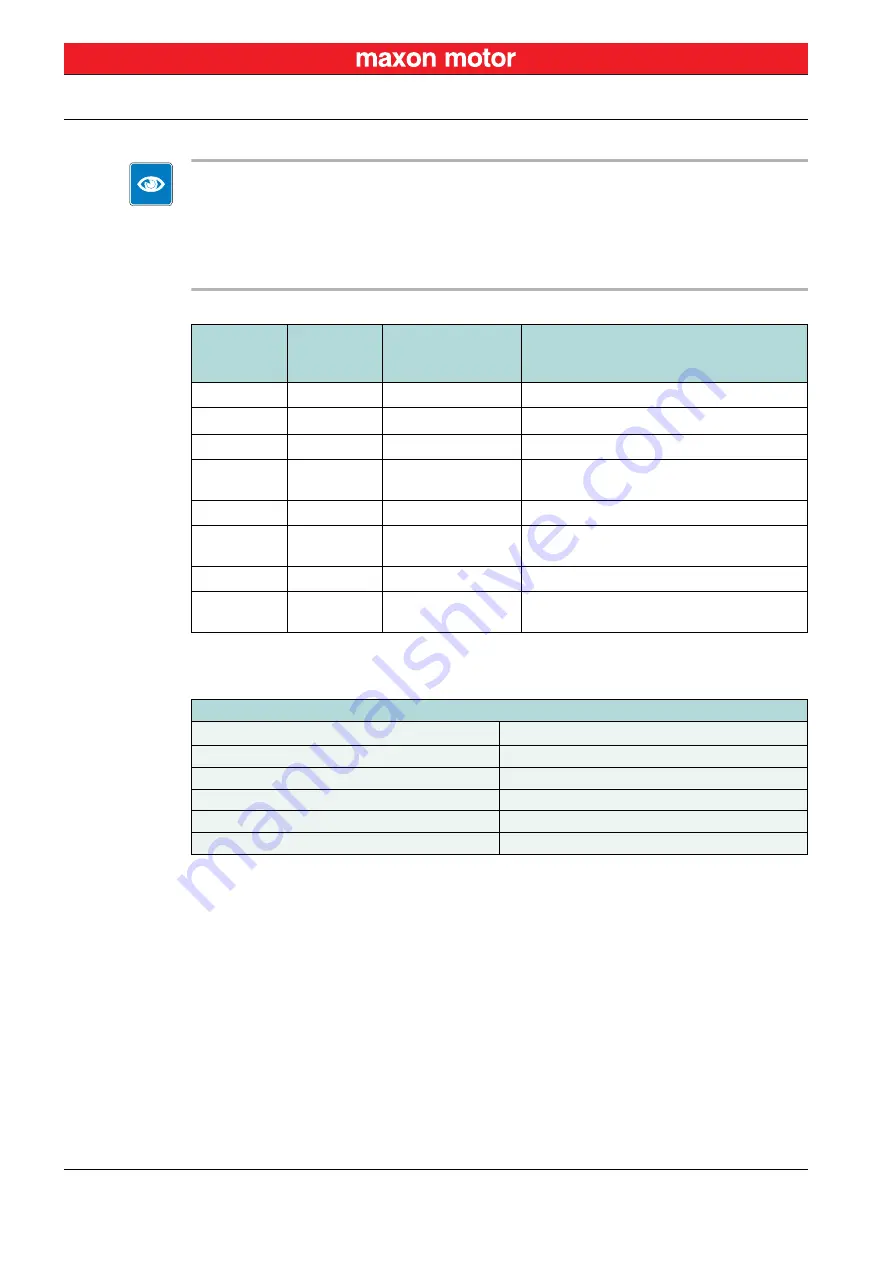
Setup
Connection Specifications
maxon motor control
3-42
Document ID: rel8003
EPOS4 Positioning Controller
Edition: May 2018
EPOS4 Module/Compact 50/5 Hardware Reference
© 2018 maxon motor. Subject to change without prior notice.
3.4.5
Encoder
Best practice
• Differential signals offer good resistance against electrical interference. Therefore,
we recommend
using a differential scheme
. Nevertheless, the controller supports both schemes – differential and
single-ended (unsymmetrical).
• For best performance,
we strongly recommend using encoders with a line driver
. Otherwise, lim-
itations may apply due to slow switching edges.
• Even though 2-channel will do,
we strongly recommend to use only 3-channel versions
.
Table 3-47
Encoder – Pin assignment
Continued on next page.
Module
Header Pin
Compact/CB
Connector
Pin
Signal
Description
A30…A36
X5 | 3
GND
Ground
A40
X5 | 2
V
Sensor
Sensor supply voltage (+5 VDC; I
L
≤
100 mA)
A41
X5 | 6
Channel A
Digital incremental encoder channel A
A42
X5 | 5
Channel A\
Digital incremental encoder channel A
complement
A43
X5 | 8
Channel B
Digital incremental encoder channel B
A44
X5 | 7
Channel B\
Digital incremental encoder channel B
complement
A45
X5 | 10
Channel I
Digital incremental encoder channel I
A46
X5 | 9
Channel I\
Digital incremental encoder channel I
complement
Encoder (differential)
Sensor supply voltage (V
Sensor
)
+5 VDC
Max. encoder supply current
70 mA
Min. differential input voltage
±200 mV
Max. input voltage
±12 VDC
Line receiver (internal)
EIA RS422 standard
Max. input frequency
6.25 MHz