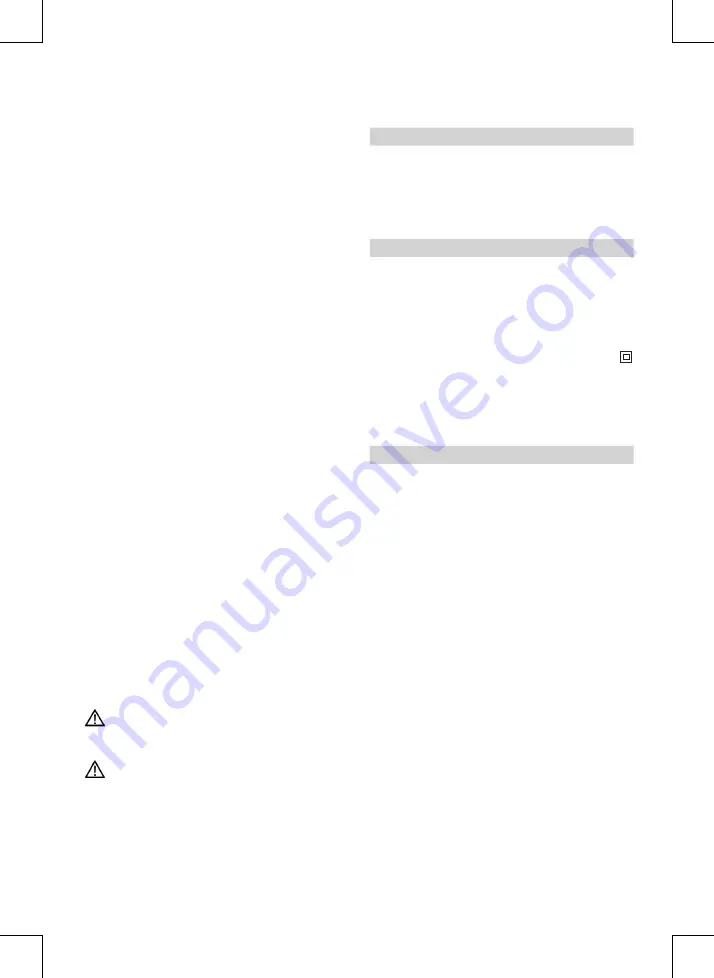
21
b) Flange nut
• Flange arrangement when using a
depressedcentre cutting wheel (Fig. 8)
a) Clamping flange
b) Flange nut
• Flange arrangement when using a straight
cutting wheel (Fig. 9)
a) Clamping flange
b) Flange nut
8.4 MOTOR
It is vital for the motor to be well ventilated
during operation. Be sure, therefore, to keep the
ventilation holes clean at all times.
8.5 WHEELS
• Never use a grinding or cutting wheel bigger
than the specified diameter.
• Before using a grinding or cutting wheel, check
its rated speed.
• The wheel´s rated speed must be higher than
the idle speed of the right-angle grinder.
• Use only grinding and cutting wheels that are
approved for a minimum speed of 12000 rpm
and a peripheral speed of 80 m/sec.
• Check the direction of rotation when you use
diamond cutting wheels. The directional arrow on
the diamond cutting wheel must point in the
direction in which the tool rotates.
8.6 OPERATING MODES
8.6.1 Rough grinding
For the best rough grinding results, hold the
grinding wheel at an angle of between 30° and
40° to the workpiece surface and guide back and
forth over the workpiece in steady movements.
It is prohibited to use the machine on
asbestos materials!
Never use a cutting wheel for rough
grinding.
9. Replacing the power cable
If the power cable for this equipment is damaged,
it must be replaced by the manufacturer or its
aftersales service or similarly trained personnel to
avoid danger.
10. Technical data
Mains voltage: 230-240 V ~/50 Hz
Power input: 900 W
Idling speed: 12000 rpm
Max. wheel diameter: 125 mm
Mounting spindle thread: M14
Protection class: II /
L
pA
sound pressure level: 91,23 (A), k=3 dB
L
WA
sound power level: 102,23 (A), k=3 dB
Vibration a
h,AG
: 6,154 m/s
2
, k=1,5 m/s
2
11. Cleaning and maintenance
Always pull out the mains power plug before
starting any cleaning work.
11.1 Cleaning
• Keep all safety devices, air vents and the motor
housing free of dirt and dust as far as possible.
Wipe the equipment with a clean cloth or blow it
with compressed air at low pressure.
We recommend that you clean the device
immediately each time you have finished using it.
• Clean the equipment regularly with a moist
cloth and some soft soap. Do not use cleaning
agents or solvents; these could attack the plastic
parts of the equipment. Ensure that no water can
seep into the device.
11.2 Carbon brushes
In case of excessive sparking, have the carbon
brushes checked only by a qualified electrician.
Important! The carbon brushes should not be rep
Summary of Contents for AG 900-125-1
Page 2: ...2 1 2 3 1 2 3 5 4 3 4 3 2 B A a...
Page 3: ...3 4 6 8 5 7 9 2 5...
Page 128: ...128 1 2 16 3 1 2 1 5 3...
Page 129: ...129 RU 30 4 4...
Page 130: ...130 30 RUS 5...
Page 131: ...131 7 3 8 8 1 4 2 2 8 2 5 5 6 1 1 2 3 4 5 7 7 1 2 3 2 A B A B 7 2 3 4 a a RUS...
Page 132: ...132 5 3 8 3 6 9 7 a b 8 a b 9 a b 8 4 RUS 8 5 12000 1 80 8 6 8 6 1 9...
Page 133: ...133 10 230 240 50 900 12000 125 91 23 102 23 6 154 2 14 85 11 12...
Page 134: ...134 1 2 3 1 a b c 2 a b c...
Page 135: ...135 UA d e f 3 a b c d e f g...
Page 136: ...136 4 a b c d e f g 5 a 4 a b c UA...
Page 137: ...137 d e f g h i j...
Page 138: ...138 k l m n o p a b c...
Page 139: ...139 d e a b c d e a b c...
Page 140: ...140 d e f 5 II...
Page 141: ...141 6 1 1 2 3 4 5 7 7 1 2 3 2 A B 7 2 3 4 4 4 4 4 7 3 1 8 8 1 4 8 2 5 5...
Page 142: ...142 5 3 8 3 6 9 7 a b 8 a b 9 a b 8 4 8 5 12000 1 80 8 6 8 6 1 30 40...
Page 152: ...152 1 2 3 1 a b c 2 a b c d e f...
Page 153: ...153 GR 3 a b c Off d e f g 4 a b c d e f g...
Page 154: ...154 5 a 4...
Page 155: ...155...
Page 156: ...156 On Off Off...
Page 157: ...157 5 6 1 2 On Off 3 4 5 7 7 1 2 3 2 7 2 4...
Page 158: ...158 7 3 1 8 8 1 4 8 2 5 5 5 3mm 8 3 6 9 7 8 9 8 4 8 5 12000rpm 8 6 8 6 1...