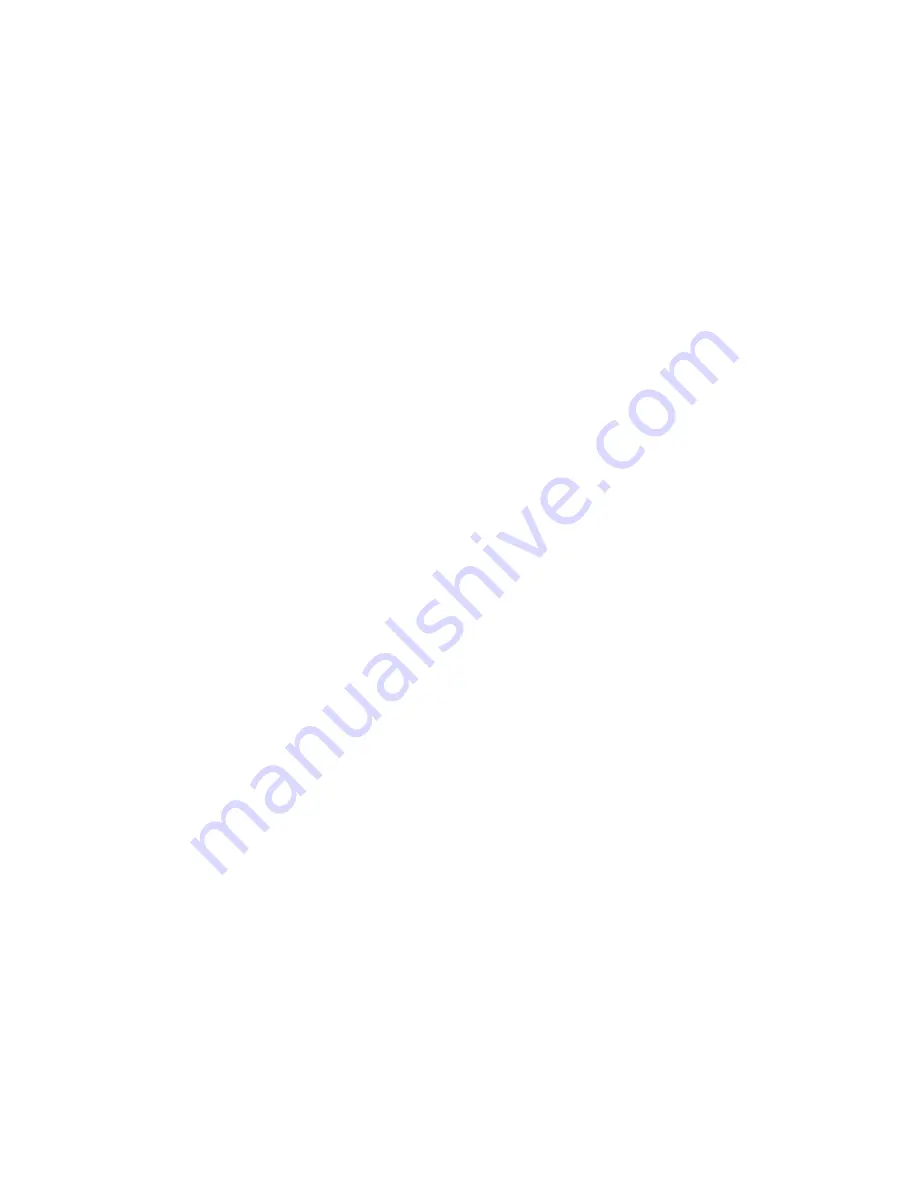
7
holes.
Blades that do not match the mounting hardware of the saw will run
eccentrically causing loss of control.
●
Never use damaged or incorrect blade washers or bolts.
The blade
washers and bolt were specially designed for your saw, for optimum
performance and safety of operation.
●
Causes and operator prevention of kickback:
- Kickback is a sudden reaction to a pinched, bound or misaligned saw
blade, causing an uncontrolled saw to lift up and out of the workpiece
toward the operator.
- When the blade is pinched or bound tightly by the kerf closing down, the blade
stalls and the motor reaction drives the unit rapidly back toward the operator.
- If the blade becomes twisted or misaligned in the cut, the teeth at the
back edge of the blade can dig into the top surface of the wood causing
the blade to climb out of the kerf and jump back toward operator.
- Kickback is the result of tool misuse and/or incorrect operating
procedures or conditions and can be avoided by taking proper
precautions as given below:
●
Maintain a firm grip with both hands on the saw and position your body
and arm to allow you to resist KICKBACK forces.
KICKBACK forces can be
controlled by the operator, if proper precautions are taken.
●
When blade is binding, or when interrupting a cut for any reason, release the
trigger and hold the saw motionless in the material until the blade comes
to a complete stop. Never attempt to remove the saw from the work or pull
the saw backward while the blade is in motion or KICKBACK may occur.
Investigate and take corrective actions to eliminate the cause of blade binding.
●
When restarting a saw in the workpiece, center the saw blade in the kerf and
check that saw teeth are not engaged into the material.
If saw blade is binding,
it may walk up or KICKBACK from the workpiece as the saw is restarted.
●
Support large panels to minimize the risk of blade pinching and
KICKBACK.
Large panels tend to sag under their own weight. Supports
must be placed under the panel on both sides near the line of cut and near
the edge of the panel.
●
Do not use dull or damaged blade.
Unsharpened or improperly set blades
produce narrow kerf causing excessive friction, blade binding and KICKBACK.
●
Blade depth and bevel adjusting locking levers must be tight and secure
before making cut
. If blade adjustment shifts while cutting, it may cause
binding and KICKBACK.
●
Use extra caution when making a “Pocket Cut” into existing walls or other
blind areas.
The protruding blade may cut objects that can cause KICKBACK.