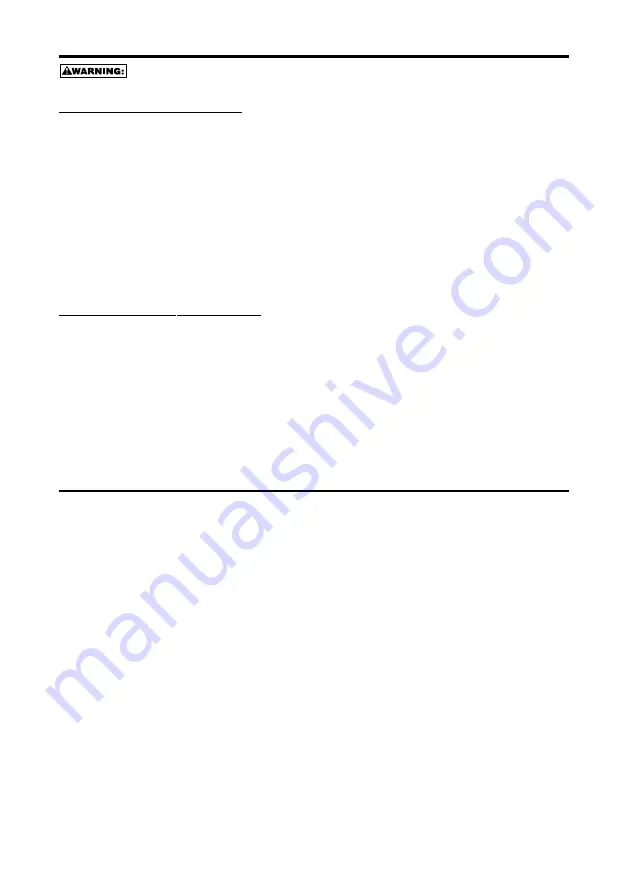
-5-
OPERATING INSTRUCTIONS
Do not use oxygen, combustible gases, or bottled gases as a power source for this tool as
tool may explode, possibly causing injury. Keep the tool pointed away from yourself and
others when connecting air source.
OPERATING PROCEDURES:
Protective equipment:
Before using any tool always ensure that you and those in the work area are using the
appropriate working equipment
Exhaust air:
each time a fastener is driven a blast of air is exhausted from the top front area of the tool, keep
your face clear of this, some tools incorporate a 360 exhaust, which enables you to control the direction of the
exhaust gases.
Always use the lowest possible air pressure for the following reasons,
- save energy
- less noise will be produced
- a reduction in fastener driving tool wear will be achieved
Any defective or improperly functioning tool must be immediately be disconnected from the compressed air
supply and passed to a specialist for inspection.
PRECAUTIONARY MEASURES:
‘Respect your tool and never horseplay’
• Keep the tool pointed in a safe direction at all times, never pointing it toward yourself or others whether it
contains fasteners or not.
• Never attempt, to drive a fastener into material that is too hard, or at too steep an angle or near the edge of
the workpiece, the fastener can ricochet causing personal injury. Remember, always hold nose right up to
and firmly against the work material.
• Disconnect the tool from the air supply before performing any maintenance, leaving the work area, moving
the tool to another location, or handing the tool to another person.
• Written approval of the tool manufacturer must be obtained prior to making any modifications to the tool.
MAINTENANCE
‘Clean and inspect your tool every time you use it’
The employer and tool operator are responsible for assuring that the tool is kept in safe working order.
Furthermore only service personnel trained by the manufacturer, distributor, or employer shall repair the tool.
CAUTION
Always remove the air supply before commencing any cleaning or
inspection and remember to correct all the problems before beginning any repair work.
• Wipe tool clean and inspect tool for wear or damage. Use non-flammable
cleaning solutions to wipe the tool. Never soak the tool in these solutions as
they can cause internal damage.
• Always ensure that all of the screws are kept tight as loose screws can cause
injury or can damage the tool.
• If the tool is used without an in line lubricant then be sure to put in about 3
drops of lubricant at the start of each workday and 3 drops for every 1,000
fasteners fired there after.
• Tools shall be repaired or equipped only with parts or accessories that are
supplied or recommended by the tool manufacturer / supplier.
•
NEVER
use a tool that requires repair work.