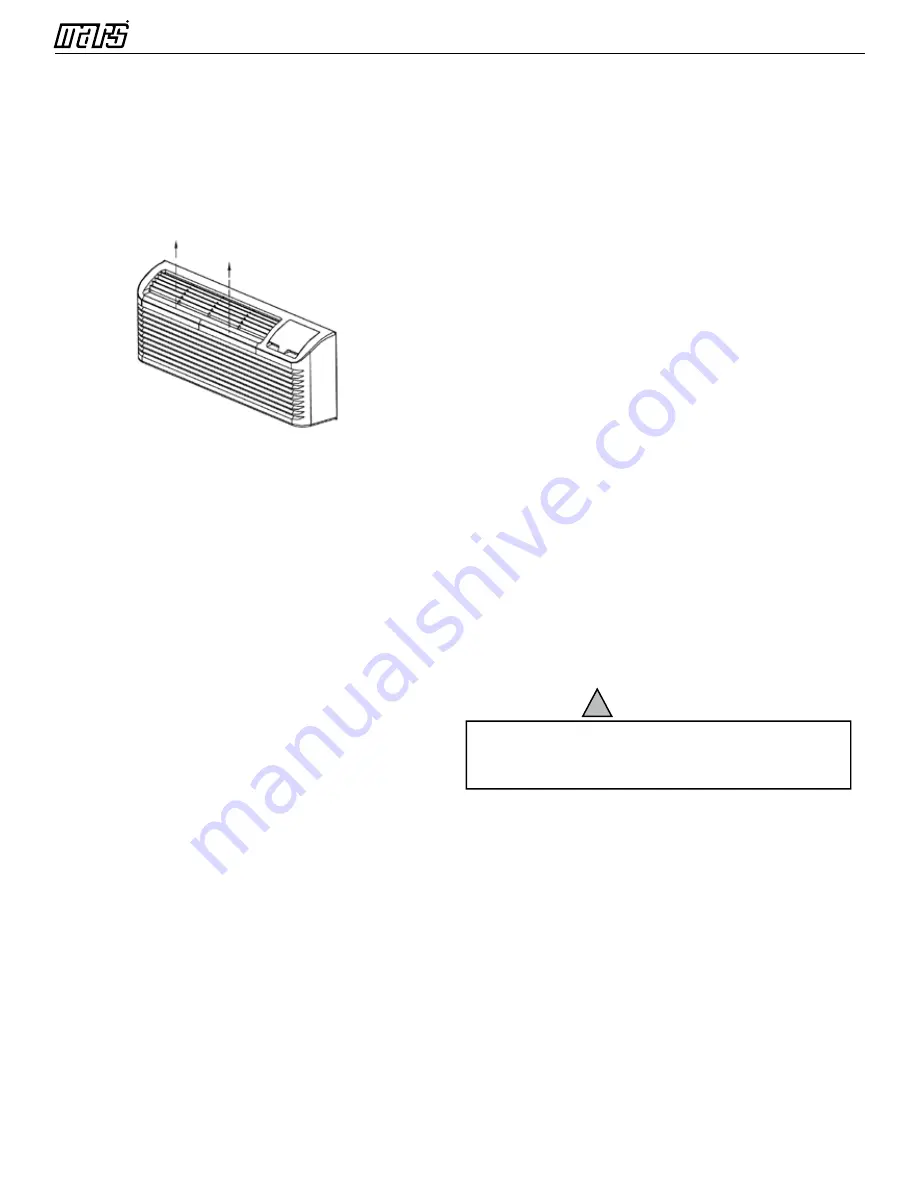
Owner’s Manual -
PTAC/PTHP130-150B/BSC
12
11
CAUTION
DO NOT USE COMMERCIAL GRADE COIL CLEANERS.
SOME OF THESE CLEANERS MAY CONTAIN ETHYLENE
DIAMINE TETRACTEIC ACID (EDTA) WHICH CAN SHORTEN
THE LIFE OF THE CONDENSER COIL.
!
Base pan and Condenser coil
Before cleaning the base pan and condenser coil, turn
OFF unit mode switch and disconnect power to the unit.
To disconnect power, disconnect power at the
fuse box
or circuit breaker.
1. Create a water tight seal by tightly covering the entire
control panel area and fan motor with plastic. Creating
this seal prevents water from entering the control area
or the fan motor and damaging the unit.
2. Spray condenser coil and base pan down with water.
3. Rinse condenser coil and base pan with water again.
NOTE:
Ensure water pressure is no higher than that
of an ordinary garden hose and the water temperature
no higher than 120°F.
Routine scheduled Maintenance
To achieve continuing top performance and high
efficiency, establish a “once a year” cleaning/inspection
schedule for the unit. Take the unit out of the sleeve and
thoroughly clean and rinse. Be sure to include in the
yearly cleaning the evaporator coil, and condenser coil,
basepan, and drain passages.
Scheduled maintenance can be accomplished by either
qualified local maintenance staff or by an authorized
servicer. They must follow the instructions described in
this manual.
Adverse Operating Conditions Maintenance
Units operating in dusty or corrosive locations; i.e.
dusty construction site or sea coast, must be cleaned
more often. A minimum of four (4) times a year will
maintain proper operational conditions and protect unit
components.
Wall sleeve
Clean the wall sleeve while cleaning the unit. The
caulking around the sleeve should be checked to make
sure that any potential air and water openings around
the sleeve are properly sealed. The wall sleeve’s level
should also be rechecked. Proper leveling for most
installations are a 1/4 bubble tilt to the outside and
level from right to left. Contact your sales person for
detailed maintenance or cleaning instructions.
Vent Screen
Before cleaning the vent screen, disconnect power
to the unit by unplugging the power cord at the wall
outlet or subbase, or disconnect power at the fuse
box or circuit breaker. If unit is operated with vent door
closed,the vent screen does not need to be cleaned.
1. Remove the cabinet front as described in Front
Removal.
2. Remove the four screws securing the chassis to the
wall sleeve.
3. Slide the chassis out of the wall sleeve far enough so
that the vent screen is accessible.
4. Clean the vent screen, slide the chassis back into the
wall sleeve, secure it in place with four screws and
reinstall the front cabinet.
Cabinet Front
The cabinet front and discharge air grille can be cleaned
with a water dampened cloth. Under no circumstances
should hydrocarbon-based cleaners (e.g. acetone,
benzene, naphtha gasoline,etc.) or ammonia based
cleaners be used to clean the front or air grilles. Use
care when cleaning the control area.
YEARLY MAINTENANCE AND CLEANING
NOTE:
Use a mild biodegradable detergent when
cleaning the unit. Special care must be taken to protect
the unit’s control board and other electrical components
from getting any water on them while cleaning. The use
of harsh or caustic cleaning agents or materials such as
bleach or coil cleaners that are not designed for PTAC
products will cause damage or deterioration of the
aluminum fin or coil material and is not recommended.
Care must be taken not to bend the aluminum fin stock.
Front removal is not
necessary to remove
the filter
Filter is removed by
grasping the filter’s top
and gently pulling up
2. Pull the filter straight up and remove.
3. Clean filter with vacuum or with running water.
Reverse this procedure to reinstall the filter.