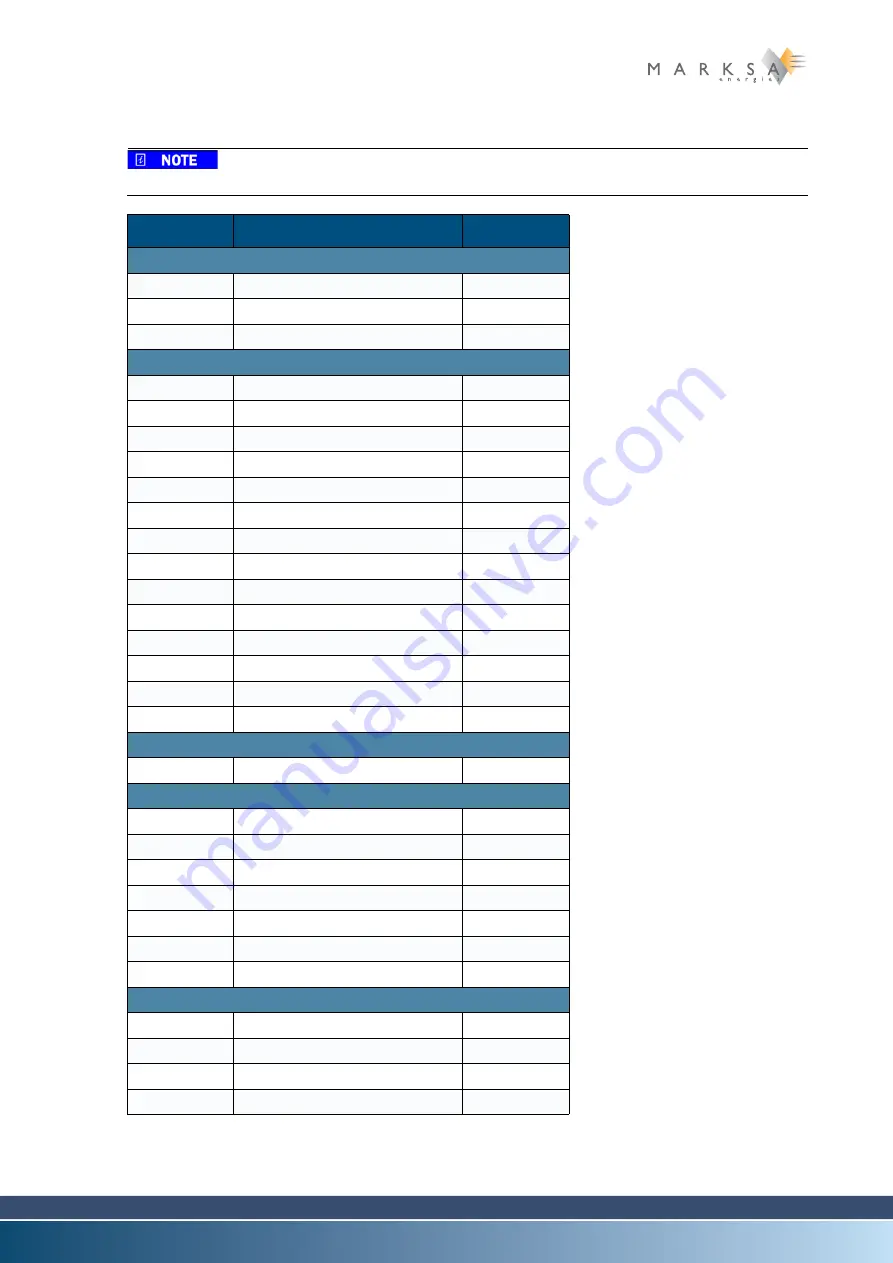
Page 58 / 86
Technical Notice CSO/CPO V1.1 / 10.14
9 Options
Settings (Omron E5CC)
The values shown below are given for information only.
Symbol
Type
Value
Adjustment
P
Proportional strip
0.9
I
Total time
65
d
Diversion time
11
Setting
CN-T
1
dU
°C
SL-H
Max setpoint
35
SL-L
Min setpoint
20
CNTL
PID
S-HC
Stnd
St
OFF
Orew
d
PtRN
OFF
ALt1
Type 1 alarm
1
ALH1
Hysteresis
1
ALt2
Type 2 alarm
1
ALH2
Hysteresis
1
oiST
Signal in mA
0-20
To access advanced functions:
AMoV
Change the value from 0 to
-169
Advanced functions
Sb1N
N-C
Sb2N
NO
At-H
0.1
Out 1
0
SUb1
High&Low temperature
ALM 1
SUb2
ALM2
SUb3
NONE
Operation
Al-1H
Too hot
10
Al-1L
Too cold
10
Al-2H
Too hot
10
Al-2L
Too cold
10