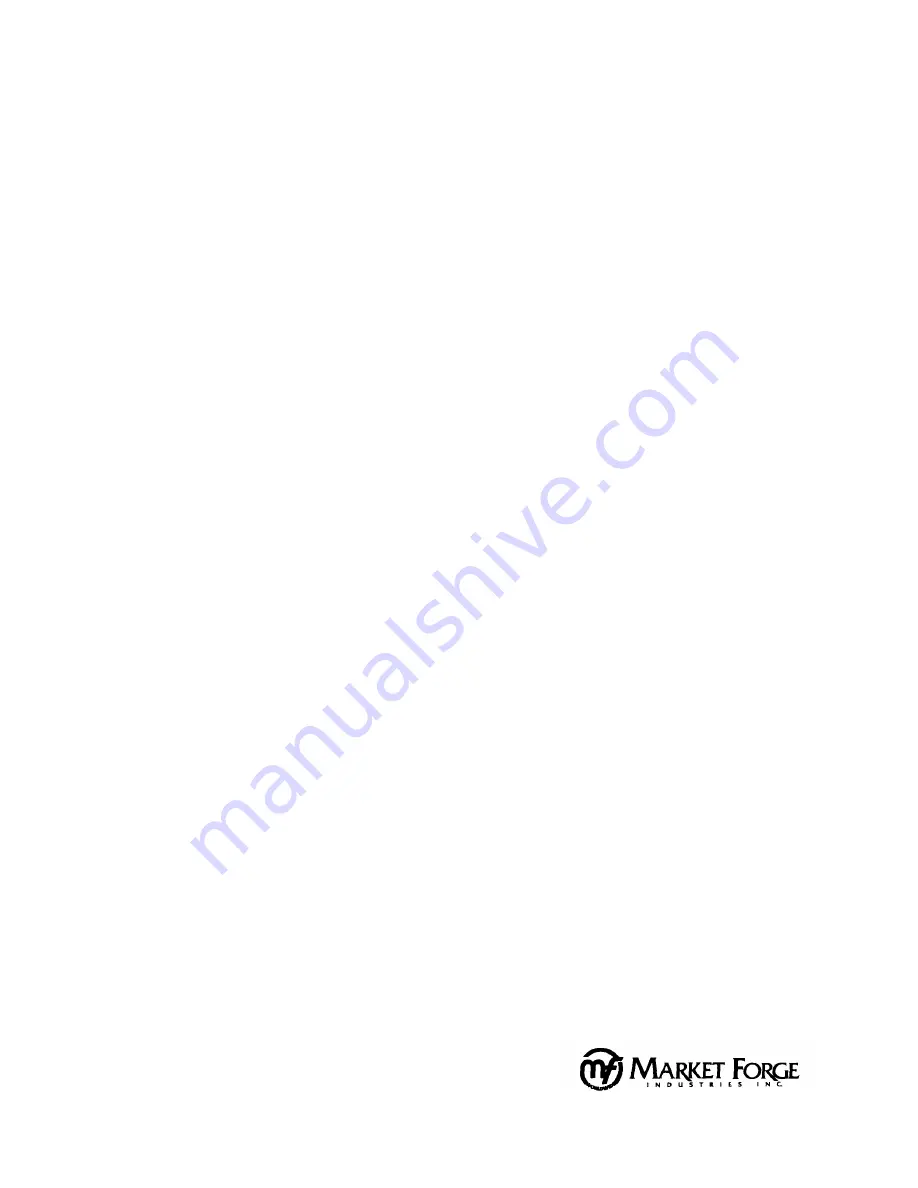
5.2 WATER LEVEL CONTROL BOARD
The Dual Function Water Level Controller is two
controls on one board. One controller maintains correct
water level in the boiler, the other a low water safety
cutoff.
The following troubleshooting procedure will only
determine if the Water Level Control Board is working
properly, it will not determine why the board has failed.
This procedure exposes you to a shock hazard and
must be performed only by qualified service personnel.
NOTE:
Improperly connected or malfunctioning water
level controller may cause damage to the steam
generator due to low water, or create a scalding hazard
to the operator due to a hot water overflow condition.
Tools Required:
A digital or analog volt meter capable of reading 120
volts A.C. and a jumper wire with alligator clips.
Procedure:
1. Turn off all power to the unit.
2. Select the controller to be tested. Inside the electrical
panel, the water level control for the top cooking cavity
is at the top of the electrical p anel and wires to the
controller will have an "A" after the wire number. The
controller for the bottom cooking cavity is at the bottom
of the electrical panel and its wires will have a "B" suf-
fix. In this test procedure, reference to the wires' "A" or
"B" suffix will be omitted.
3. Remove the wires #40,41, and 42 from the terminal
connectors "G", "H", and "LLOC".
WARNING:
When
you turn the power on, there are
terminals that carry 120 volts. Protect the ends of these
disconnected wires to prevent
snorting to hot /eads.
4. Turn power ON. Using the voltmeter, check that
power being supplied to terminals L I & L2 is 1 20 volts,
plus 10%, minus 15%.
MARKET FORGE INDUSTRIES
,
INC
35
GARVEY
STREET EVERETT, MA 02149
5.6
TEL 6173874100 TELEX 94-9414
FAX
6173874456 OUTSIDE MA 800 227 2659
5. Troubleshooting