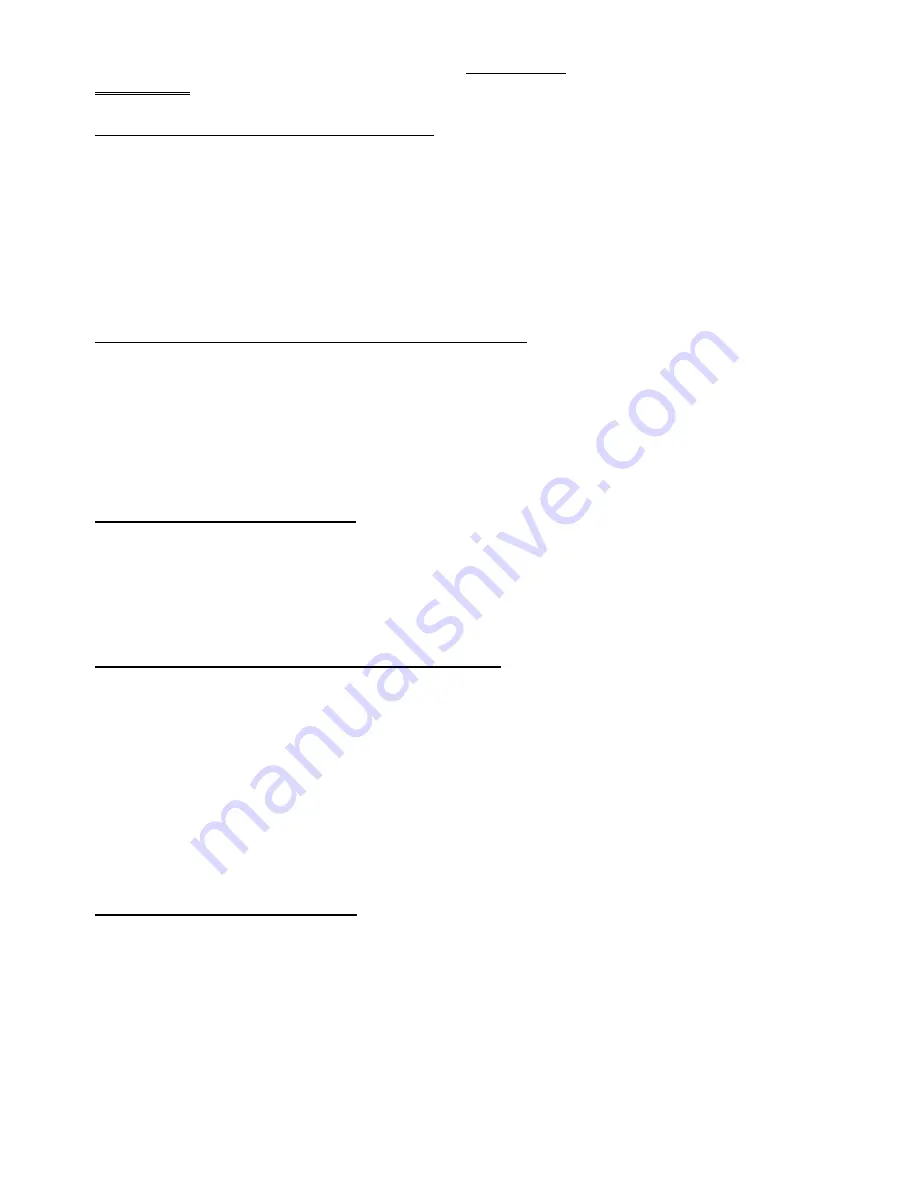
23
SECTION 5 ASSEMBLY
DOMESTIC
CHECKING THE 230° SETTING, STM-EL
The Unit should be completely evacuated then temperature selector dial should be turned on
230° Fahrenheit, Observe the current until it takes a sharp drop to approximately one-third of
the full load; at this instant, there should be a corresponding chamber pressure of 2 PSI
Observing the current further will show an- other sharp drop to approximately 2 Amps; at this
instant, there should be a corresponding chamber pressure of 6.1 PSI and a temperature
reading of 22.8° to 232° Fahrenheit, on the temperature gauge.
ADJUSTING THE RANGE OF OPERATION, STM-EL
The range of operation of Model STM-EL is adjusted by simply turning the adjusting knob on
the outside of the Control Panel. A counter-clockwise turn decreases the pressure while a
clockwise turn increases the pressure. Observe pressure and temperature gauges and adjust
knob as required.
NOTE: When resetting this control for elevations above sea level, a correction of 6/10 Ibs. per thousand feet is
necessary.
CAST-IN HEATING ELEMENTS
Located under the sterilizing cylinder is a bank of (3) U-shaped heating elements. These
elements are welded in place in a protective aluminum shield. The elements cannot be
removed, and in the unlikely event that one or all fail, the complete cylinder must be
replaced.
THE LOW WATER CUT -OFF (MANUAL RESET)
Fastened to a special mounting brace behind the front panel, the Low Water Cut-Off acts to
shut off the complete unit, should the water run dry. The Low Water Cut Off is factory set, to
shut the unit off when the cylinder temperature rises between 380 and 440° Fahrenheit.
When the Sterilmatic is turned on without water or the water has been evaporated away, the
temperature of the aluminum sterilizing cylinder will rise and by heat induction effect the Low
Water Cut-Off. Its inner electrical contacts will be forced open from heat expansion, thus
cutting off the flow of electric current to the heating elements. With the replacement of water
into the cylinder. The cylinder temperature will drop and the contacts of the Low Water Cut-
Off can be again closed. The unit will only restart after the manual button has been re-set.
THE ELECTRIC CONTACTORS
The Electric Contactors are located behind the removable lower front panel. These important
components receive an electrical impulse when the Timer is turned on. When the unit
reaches a pre-set pressure of 1.3-13.5 PSI the #1 switch will cut out causing the front
contactor to become de-energized. This, in turn, will disconnect the left and right bank of
heaters and the timer motor will start.
Summary of Contents for STM-E
Page 2: ...35 Garvey Street Everett Massachusetts 02149 ...
Page 6: ......
Page 7: ...5 SECTION 1 INSTALLATION INSTRUCTIONS ...
Page 10: ...8 SECTION 1 INSTALLATION INSTRUCTIONS ...
Page 11: ...9 SECTION 1 INSTALLATION INSTRUCTIONS ...
Page 12: ...10 SECTION 1 INSTALLATION INSTRUCTIONS TYPICAL CIRCUIT CONNECTION FOR STM E AND STM EL ...
Page 19: ......
Page 21: ......
Page 22: ......
Page 28: ...26 SECTION 6 ILLUSTRATED PARTS ...
Page 29: ......
Page 30: ...28 SECTION 6 ILLUSTRATED PARTS ...
Page 31: ......
Page 32: ......
Page 33: ......
Page 34: ......
Page 35: ......