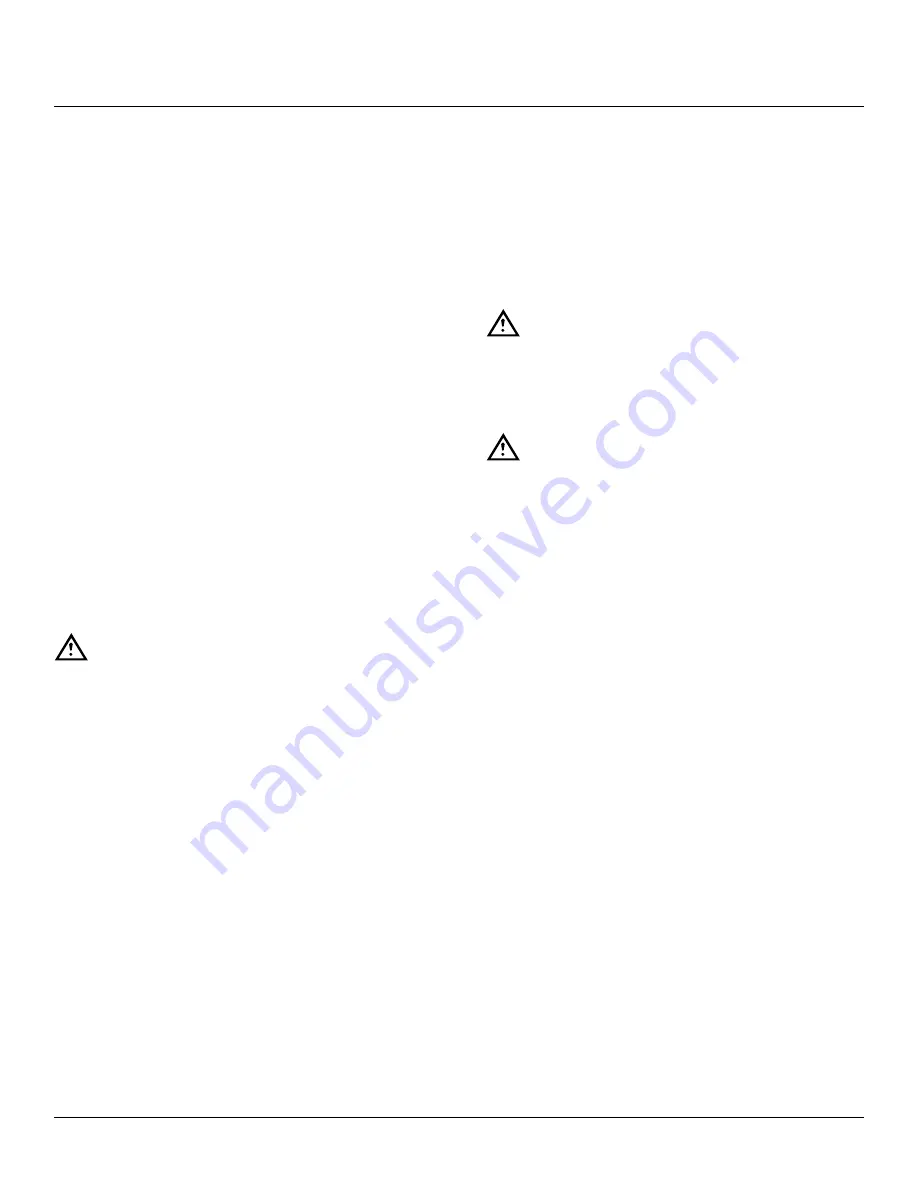
5
INSTALLATION
Utility Connections
GAS CONNECTION
The serial plate on the lower right side of the unit indicates
the type of gas your unit is equipped to burn. Do NOT
connect to any other gas type.
A 3/4” NPT line is provided at the rear for the connection.
Each unit is equipped with an internal pressure regulator
which is set for 3.5” W.C. manifold pressure for natural
gas and 4.0” W.C. for propane gas. Use 1/8” pipe tap on
the downstream side of the combination valve for check-
ing pressure.
An adequate gas supply is imperative. Undersized or low
pressure lines will restrict the volume of gas required for
satisfactory performance. A steady pressure, minimum 6”
W.C. for natural gas and minimum 11” W.C. for propane
gas, is recommended. With all units operating simultane-
ously, the manifold pressure on all units should not show
any appreciable drop. Fluctuations of more than 25% on
natural gas, and 10% on propane gas, will create pilot
problems and affect burner operating characteristics.
Contact your gas company for correct supply line sizes.
Purge the supply line to clean out any dust, dirt, or other
foreign matter before connecting the line to the unit. It is
recommended that an individual manual shut off valve be
installed in the gas supply line to the unit. Use pipe joint
compound which is suitable for use with LP gas on all
threaded connections. Test pipe connections thoroughly
for gas leaks.
WARNING
All connections must be checked for leaks,
after the unit has been put in operation. Use
soapy water only for testing on all gases.
Never use an open flame to check for gas
leaks.
NOTICE
If applicable, the vent line from the gas appli-
ance pressure regulator shall be installed to
the outdoors in accordance with local codes
or, in the absence of local codes, with the Na-
tional Fuel Gas Code, ANSI Z223.1/NFPA 54, or
the Natural Gas and Propane Installation Code
CSA B149.1, as applicable.
NOTICE
If this equipment is being installed at over
2,000 feet altitude and was not so specified on
order, contact service department. Failure to
install with proper orifice sizing may void the
warranty.
WATER CONNECTION
On units equipped with an optional water fill valve connect
a water line (minimum 1/4”) to the valve with a 1/4” NPT
female fitting. Units with dual (hot and cold) valves must
have the hot water line connected to side with the hot wa-
ter valve (red) and cold water line to the cold water valve
(blue). Plastic or rubber hose is not recommended, as it
may melt against the hot kettle side.
ELECTRICAL CONNECTION
WARNING
Do not connect the kettle to the electrical sup-
ply until after the gas connection has been
made.
1. 120 VAC - 60 Hz - Single Phase
WARNING: ELECTRICAL GROUNDING
INSTRUCTIONS
This appliance is equipped with a three-prong
(grounding) plug for your protection against
shock hazard and should be plugged directly
into a properly grounded three-prong recep-
tacle. Do not cut or remove the grounding
prong from this plug. (120V units only).
Units with this electrical rating are factory supplied
with a three-wired cord and three-prong plug which
fits any standard 120V, three-prong grounded recep
-
tacle. A separate 15 amp supply is needed for each
unit.
2. 208/240 VAC - 60 Hz - Single and Three Phase
Units with this electrical rating are factory equipped
with a transformer. To connect supply wires, remove
cover from right console. Route supply wires and
ground wire through the hole in the console with a
strain relief fitting. Connect wires to the terminal
block in the rear of the right console. Connect ground
wire to lug. Replace cover. Three-phase units are
wired as above, using only two supply wires. The
third supply wire is not connected and must be prop-
erly terminated.
3. 220 VAC - 50 Hz - Single Phase
Units equipped with this voltage ratings should be
wired exactly as in (2.) above.