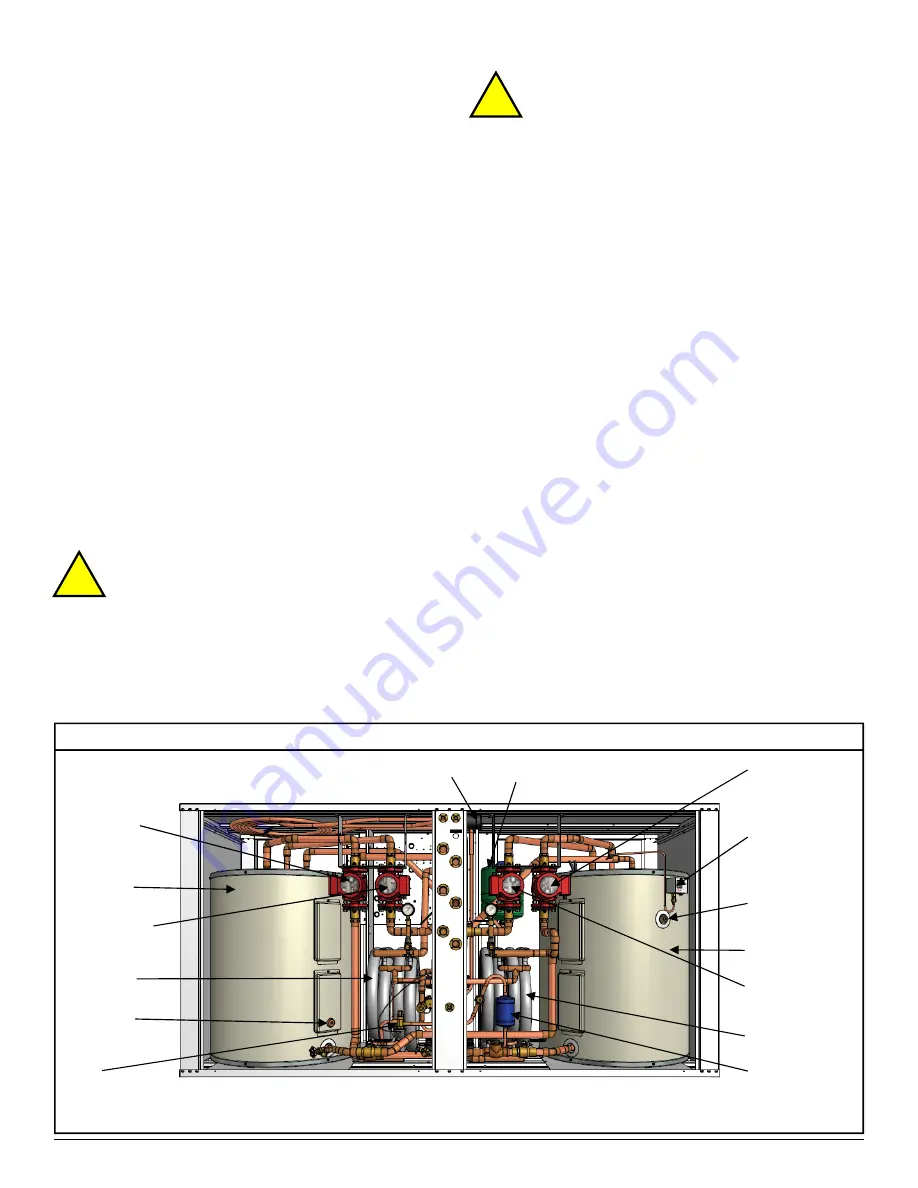
Page 8
000662MAN-03
01 MAR 2012
DIAGRAM B - Circulator and Major Component Locations
25. Open the fill hose valve.
26. Purge until no air can be heard leaving the system.
27. Close the Cold Zone Ball Valve
28. Open the top isolation valve of the Cold Zone Circulator.
29. Purge until no air can be heard leaving the system.
30. Close the Cold Indoor Boiler Drain.
31. Move the drain hose to the Hot Indoor Boiler Drain.
32. Open the top isolation valve of the Cold Indoor Circulator.
33. Open the Hot Indoor Boiler Drain.
34. Purge until no air can be heard leaving the system.
35. Close the Hot Indoor Boiler Drain.
36. Close the Cold Zone Boiler Drain when the system reaches
the desired pressure level.
37. Close the fill hose valve and disconnect the hoses.
38. Open the Cold Zone and Cold Indoor Ball Valves.
39. Open the Hot Zone and Hot Indoor Ball Valves.
40. Do a final check of all ball valves and isolation valves to
ensure they are all open.
Repeat the above procedure as necessary to ensure that
all of the air has been removed, then remove the purging equip-
ment.
DOMESTIC HOT WATER
CONNECTIONS
A typical piping diagram for a two tank (pre-heat tank) con-
figurations can be found in
drawing 000970PDG at the end of
this section
. Be sure to note the position of the check valve and
the direction of water flow. Other configurations are possible,
and there may be multiple units tied together in larger buildings.
CAUTION: Use only copper pipe to connect the
desuperheater. Should the DHW thermostat fail,
the water temperature could rise to as high as
200°F (93°C).
Ensure the tank is filled with water and under pressure
before activating the heat pump. Slightly loosen the boiler drain
on the DHW Out pipe to allow air to escape from the system
before the unit is started. This step will make certain that the
domestic hot water circulator in the unit is flooded with water
when it is started.
CAUTION: the domestic hot water pump is water
lubricated; damage will occur to the pump if it is
run dry for even a short period of time.
The DHW loop may have to be purged of air several times
before good circulation is obtained. A temperature difference
between the DHW In and DHW Out can be felt by hand when
the circulator pump is operating properly.
The final tank should be set to
140°F(60°C).
The pre-heat
tank does not require electric elements. This setup takes full
advantage of the desuperheater as it is the sole heat provider to
the pre-heat tank. The desuperheater remains active during the
compressor runtime until the pre-heat tank has been completely
heated by the desuperheater alone. This setup is more energy
efficient than a single tank setup.
CAUTION: If two (2) shut-off valves are located on the
domestic hot water ines as shown in the diagram, a pres-
sure relief valve must be installed to prevent possible dam-
age to the domestic hot water circulator pump should both
valves be closed.
!
Evaporator
Cold Indoor
Circulator
(Evaporator)
Hot Zone
Circulator
Cold Zone
Circulator
DHW Circulator
Condenser
Hot Tank
Cold Tank
Expansion Tank
Cold Tank
Probe
Hot Tank
Probe
Safety Pressure
Switch for Electric
Backup
Hot Indoor
Circulator
(Condenser)
TXV
Filter-drier
!
Summary of Contents for EMWT-65-HACW-P-1T
Page 9: ...01 MAR 2012 Page 9 000662MAN 03...
Page 10: ...Page 10 000662MAN 03 01 MAR 2012...
Page 13: ...01 MAR 2012 Page 13 000662MAN 03...
Page 16: ...Page 16 000662MAN 03 01 MAR 2012...
Page 19: ...01 MAR 2012 Page 19 000662MAN 03...
Page 34: ...Page 34 000662MAN 03 01 MAR 2012 REFRIGERATION CIRCUIT DIAGRAM...
Page 35: ...01 MAR 2012 Page 35 000662MAN 03 REFRIGERATION CIRCUIT DIAGRAM continued...
Page 41: ...01 MAR 2012 Page 41 000662MAN 03 ELECTRICAL DIAGRAMS 230 1 60...
Page 42: ...Page 42 000662MAN 03 01 MAR 2012 ELECTRICAL DIAGRAMS 230 1 60 continued...
Page 43: ...01 MAR 2012 Page 43 000662MAN 03 Back View Front View CASE DETAILS Right Side View...