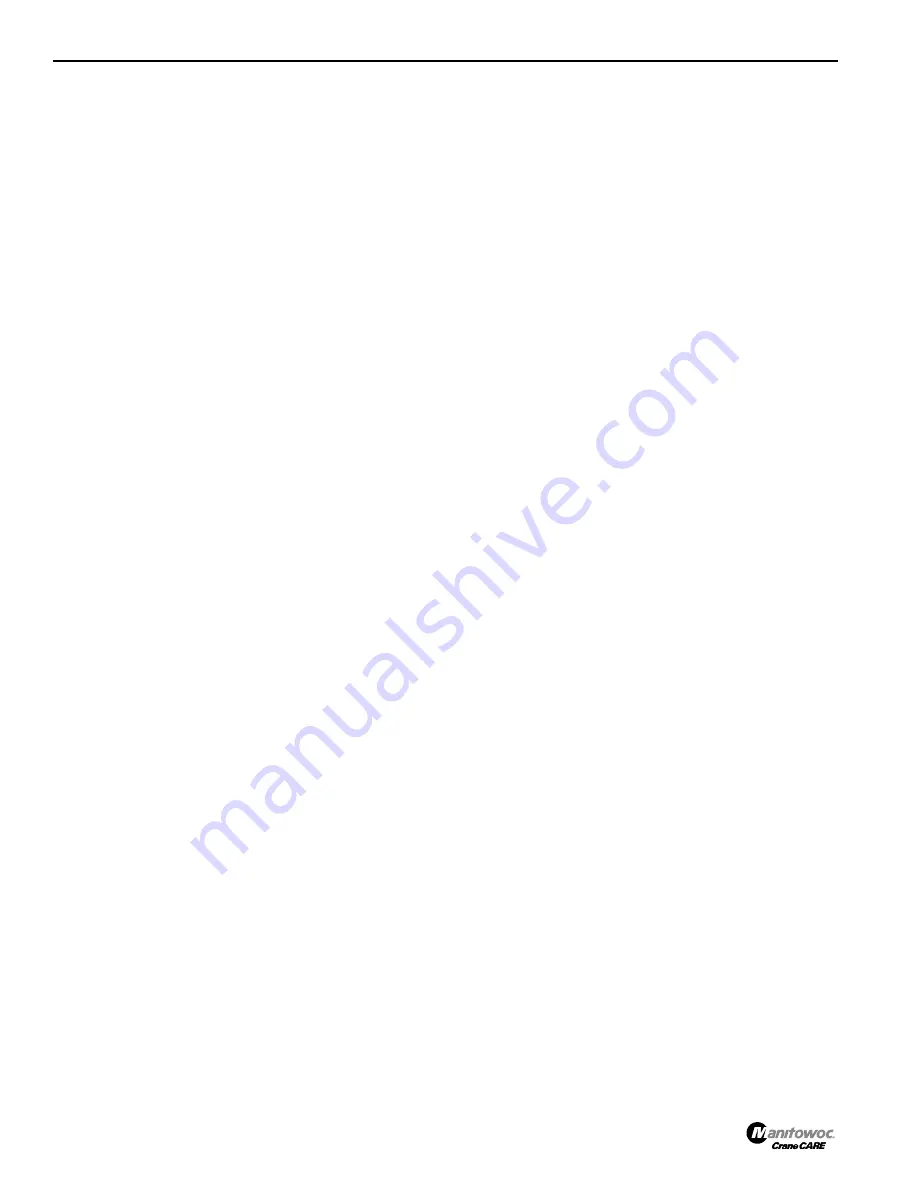
PREVENTATIVE MAINTENANCE
CD5515-2/YB5515-2 SERVICE MANUAL
5-2
Published 1-20-2017, Control# 483-02
SAFETY BELT
- Check for frayed or cut webbing, damaged
buckles or loose mounting hardware.
SAFETY DECALS
- Check condition of decals. Replace if
worn, damaged or missing. See Section 2.
COVERS
- Keep all protective covers in place.
PARKING BRAKE
- Check operation. Have unit repaired if
required.
ENGINE
- Check operation. Remove all dirt or debris, and all
flammable materials before running engine.
LUBRICANTS
Cummins Oil Registration List
Cummins has a program that lists engine oils that it has
tested to meet its engineering specifications. Listing of
recommended oils is on QuickServe® Online. Log on to
quickserve.cummins.com and login with a current username
and password or create a new account by selecting “Create
an Account” under information, choose Limited Owners Plan
and register. Once logged in, click on the “Service” Tab in the
top red bar, “Service Tools” mini-tab and “Oil Registration
Lists” link within the Service Tools list. This will load a list of
the different Cummins Engineering Specification numbers.
Select the one that applies to your engine to view the
registered oils.
It is not the policy of Manitowoc Cranes, Inc. to publish lists
of approved lubricants or guarantee lubricant performance.
The responsibility for the quality of the lubricant rests
completely with the distributor or manufacturer of the
lubricant.
In various paragraphs in this maintenance section,
statements may be found, “use (lubricant brand name) or
eq uiva len t. ” Th is stat eme nt d oe s no t co ns tit ut e an
unconditional guarantee of performance of the brand of
lubricant mentioned. It is intended only as a guide to the type
of lubricant recommended for a given application.
MAINTENANCE RECORDS
Dated records must be kept for inspection of critical
components such as, brakes, crane hooks, wire ropes,
hydraulic cylinders and relief valve pressure settings. These
records must be kept where they can be easily obtained and
reviewed.
MAINTENANCE
Preparation
Before maintenance, adjustments and repairs are started on
a crane, the following precautions shall be taken as
applicable:
•
Place a warning tag in a conspicuous location at the
controls stating that the machine requires adjustment or
repair before it can be operated.
•
Park the crane where it will cause the least interference
with other equipment or operations in the area.
•
Place all controls at the off position and set the brakes to
prevent inadvertent motion.
•
Disable all methods used to start the crane's engine.
•
Lower the boom to the ground or otherwise secured
against dropping.
•
Lower the hook block to ground or otherwise secured
against dropping.
•
Relieve the hydraulic pressure from all hydraulic circuits
before loosening or removing hydraulic components.
After maintenance, adjustments and repairs have been
made, do not return the crane to service until all guards have
been reinstalled, trapped air removed from the hydraulic
system if required, safety devices reactivated, and
maintenance equipment and all warning tags removed.
Maintenance, adjustments and repairs shall be done only by
designated personnel who are properly trained. Use only
Manitowoc supplied parts to repair the crane.
Hydraulic System Maintenance Precautions
Contaminants in a hydraulic system affect operation and
result in serious damage to the system components. Dirty
hydraulic systems are a major cause of component failures.
If evidence of foreign particles is found in the hydraulic
system, flush the system.
Disassemble and reassemble hydraulic components on a
clean surface.
Clean all metal parts in a nonflammable cleaning fluid. Then
lubricate all components to aid in assembly.
Inspect all sealing elements (O-ring, gaskets, etc.) when
disassembling and assembling the hydraulic system
components. Installation of new sealing elements is always
recommended.
When installing metal hydraulic tubes, tighten all bolts finger
tight. Then, in order, tighten the bolts at the rigid end, the
adjustable end, and the mounting brackets. After tubes are
mounted, install the hoses. Connect both ends of the hose
with all bolts finger tight. Position the hose so it does not rub
the machine or another hose and has a minimum of bending
and twisting. Tighten bolts in both couplings.
Due to manufacturing methods, there is a natural curvature
to a hydraulic hose. The hose should be installed so any
bend is with this curvature.
Reference Only