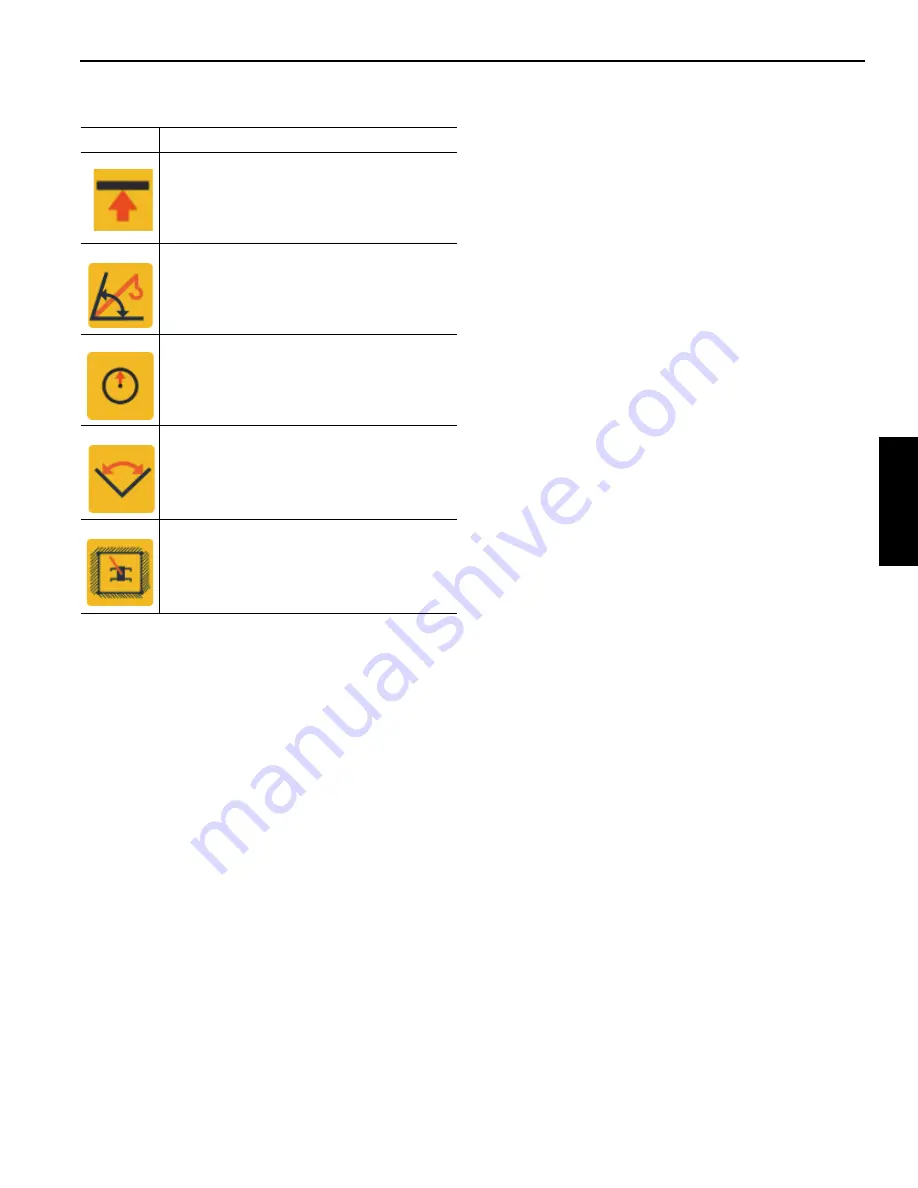
Grove
Published 3-25-2020, Control # 643-04
3-33
GRT880 OPERATOR MANUAL
OPERATING CONTROLS AND PROCEDURES
3
When a limitation is active, audible alarms are generated.
Table 3-2: indicates the behavior of the audible alarm for the
various limitations when the WRL is configured to only have
an alarm (not lockout). When the WRL is configured for the
lockout option, the alarm is generated based on when crane
functions are being affected.
The operator should notice that all the audible alarm triggers
use the values of 10 and 5. This may be 10 or 5 degrees, or it
may be 10 or 5 ft distance. This is intentional so that the
operator can continue to watch the crane operation and not
have to look at the display (assuming the 10 and 5 values are
remembered). Whenever slow beeping is heard, this will be
a 10 threshold. Whenever fast beeping is heard, this will be a
5 threshold. Whenever there is a solid sound, this will signify
being at the limitation.
TABLE 3-1: Active Indicator Symbols
Symbol
Description
Height Limitation is Active indicator symbol
(amber color)
Boom Up/Down Limitation is Active indicator
symbol (amber color)
Radius Limitation is Active indicator symbol
(amber color)
Swing Limitation is Active indicator symbol
(amber color)
Wall Limitation is Active indicator symbol
(amber color)
Summary of Contents for Grove GRT880
Page 1: ...Operator Manual Grove GRT880 8968 ...
Page 4: ...THIS PAGE BLANK ...
Page 10: ...TABLE OF CONTENTS GRT880 TOC 6 THIS PAGE BLANK ...
Page 16: ...INTRODUCTION GRT880 OPERATOR MANUAL 1 6 Published 3 25 2020 Control 643 04 THIS PAGE BLANK ...
Page 200: ...OPERATOR MANUAL GRT880 6 2 THIS PAGE BLANK ...
Page 201: ......
Page 202: ......