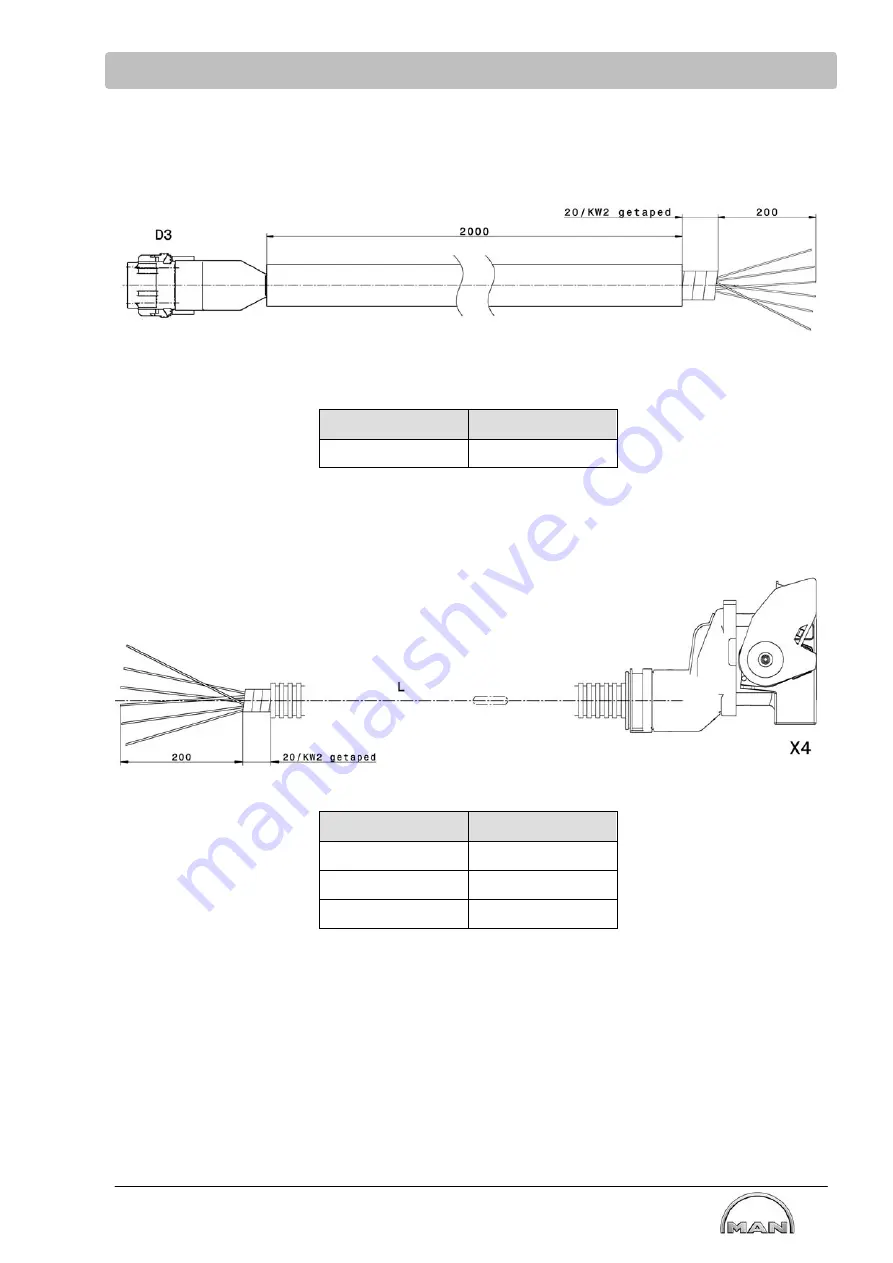
Connecting cable
117
Read this manual carefully before starting any work!
This is particularly applicable to the chapter “General Safety Instructions”
and the respective safety instructions in the chapters.
D3 bridge display C - Inputs CC
Length L
Part number
2 m
51.25411-6113
X4 E-box - ship
Length L
Part number
10 m
51.25411-6114
20 m
51.25411-6093
29 m
51.25411-6124
Summary of Contents for iSea
Page 1: ......
Page 2: ......
Page 163: ...Wiring diagram Marine shipyard classified...
Page 164: ......
Page 165: ...Wiring diagram Marine shipyard non classified...
Page 166: ......
Page 170: ......
Page 171: ......
Page 172: ......