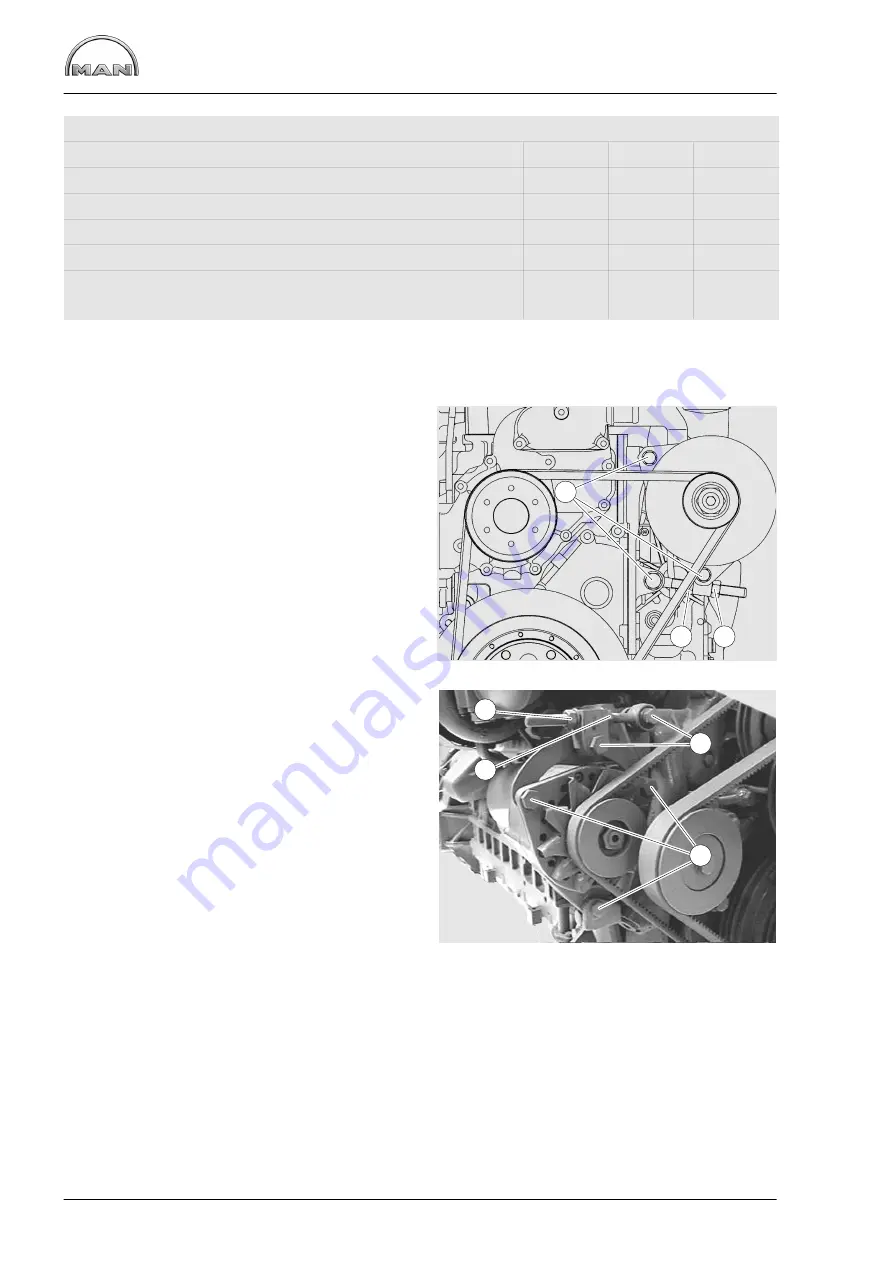
Maintenance and care
28
Tension force in cold condition according to kg scale on tester
Drive belt width
10.0
13.0
2-AVX13
New installation
Installation
45
−
50
50
−
55
100
−
110
After 10 min. running time
35
−
40
40
−
45
80
−
90
When servicing after long running time
30
35
Minimum tension force
50
Retensioning value after minimum tension force is re-
ached
70
Tensioning and changing V-belt
Crankshaft
−
Water pump
−
Alternator
D
Remove fixing bolts
À
D
Remove lock-nut
Á
D
Adjust nut
Â
until V-belts have correct
tensions
D
Retighten lock-nut and fixing bolts
To change the V-belt, turn back the setting
nut
Â
and swivel the alternator inwards.
1
2
3
Water pump
−
Alternator
D
Remove fixing bolts
À
D
Remove lock-nut
Á
D
Adjust nut
Â
until V-belts have correct
tensions
D
Retighten lock-nut and fixing bolts
To change the V-belts, remove the fan,
turn back the setting nut
Â
and swivel the
alternator inwards.
1
1
2
3
Summary of Contents for D 2876 LE 101
Page 1: ......
Page 2: ......
Page 3: ...3 Operating Instructions MAN Industrial Diesel Engines...
Page 4: ...4...
Page 39: ...Notes 39...
Page 41: ......
Page 42: ......