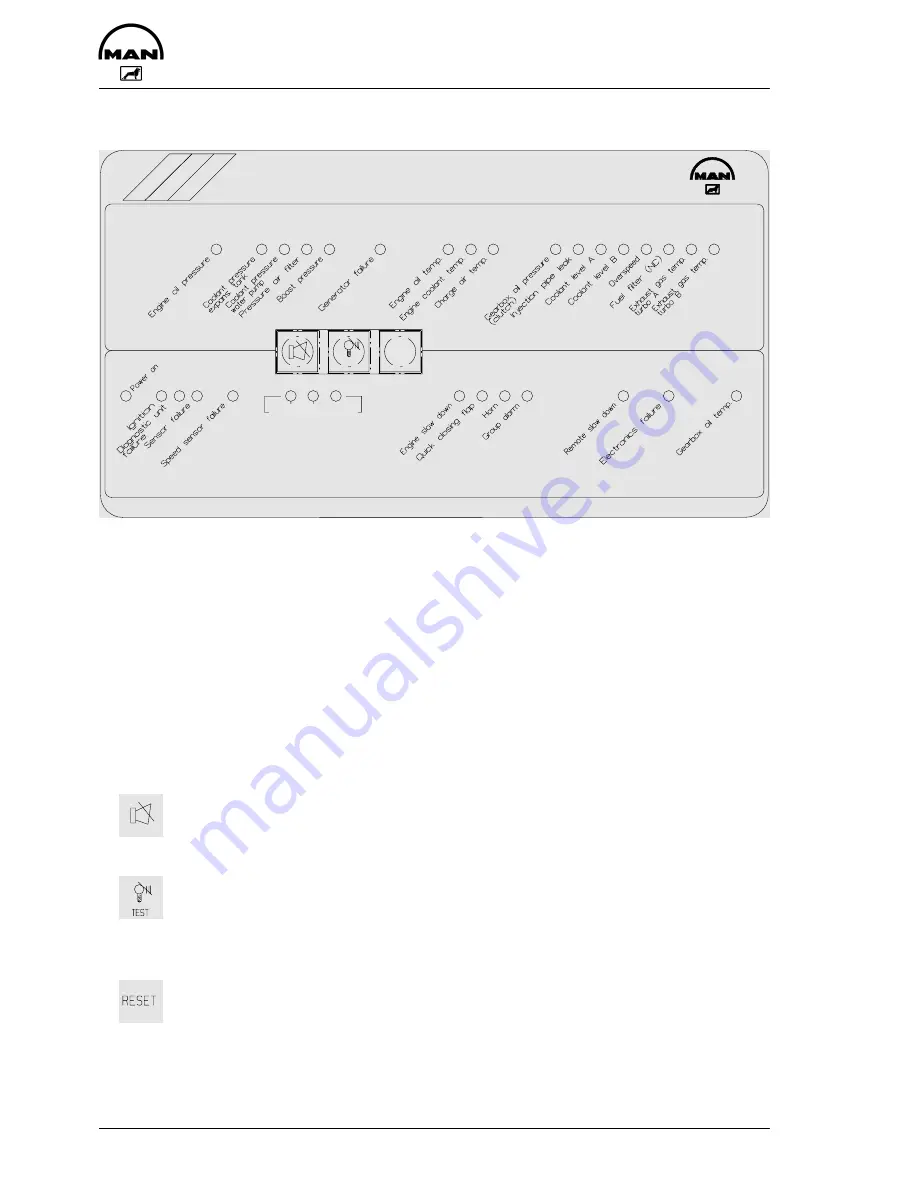
Commissioning and operation
48
Terminal box in the engine room / interface with light-emitting keys
TYP BE3
Serial data activity
MAN Marine Diesel
RESET
TEST
The terminal box with light-emitting diodes functions at the same time as an engine room
monitoring panel.
If an alarm is issued, the corresponding light-emitting diode lights up. The following re-
lays are activated on the diagnosis unit:
D
Engine slow down (main alarm) = reduction of engine speed
D
Horn = acoustic alarm
D
Group alarm = collective fault indication
The keys are intended for:
D
Horn off
Switches off the alarm horn and the integrated buzzer
D
Flashing light off, transition to continuous light / test of light-emitting diodes
Switches off the flashing signal of the relevant warning lamp, i.e. the flashing
light switches to continuous light. Before the flashing signal is cleared, the
alarm horn must be switched off.
D
Reset
Clearing the alarm message (red warning lamp goes out)
Requirement for clearing an alarm message is:
– Pressing the keys “Horn off” and “Test” in that order
– Removing the cause of the alarm