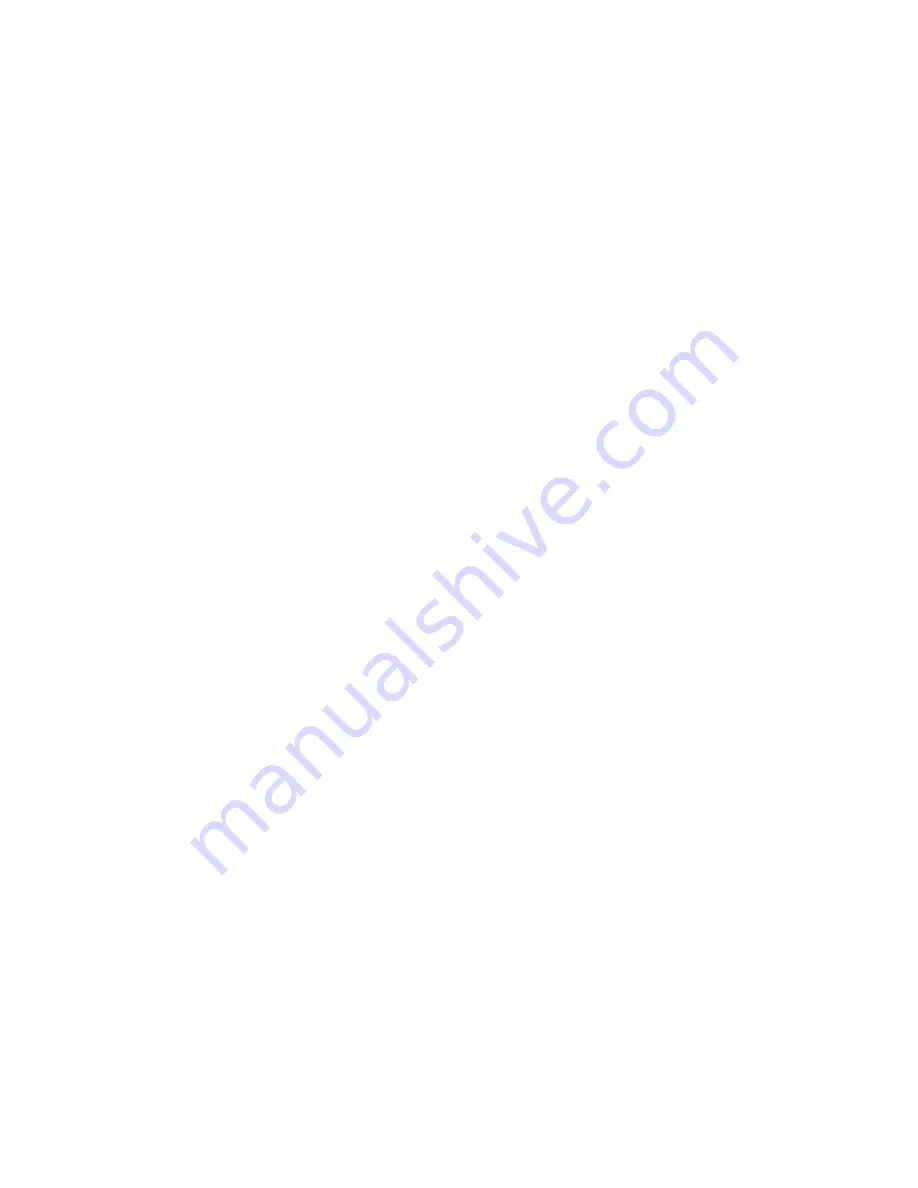
8
FUNCTIONAL DESCRIPTION
CAUTION:
• Always be sure that the tool is switched off and
unplugged before adjusting or checking function on the
tool.
Shaft lock (Fig. 1)
CAUTION:
• Never actuate the shaft lock when the spindle is mov-
ing. The tool may be damaged.
Press the shaft lock to prevent spindle rotation when
installing or removing accessories.
Switch action (Fig. 2)
CAUTION:
• Before plugging in the tool, always check to see that
the switch trigger actuates properly and returns to the
“OFF” position when released.
For tool with the lock-on switch
To start the tool, simply pull the switch trigger (in the B
direction). Release the switch trigger to stop. For continu-
ous operation, pull the switch trigger (in the B direction)
and then push in the lock lever (in the A direction). To
stop the tool from the locked position, pull the switch trig-
ger fully (in the B direction), then release it.
For tool with the lock on and lock-off switch
To prevent the switch trigger from accidentally pulled, a
lock lever is provided.
To start the tool, push in the lock lever (in the A direction)
and then pull the switch trigger (in the B direction).
Release the switch trigger to stop.
For continuous operation, push in the lock lever (in the A
direction), pull the switch trigger (in the B direction) and
then pull the lock lever (in the C direction).
To stop the tool from the locked position, pull the switch
trigger fully (in the B direction), then release it.
Electronic function
The tools equipped with electronic function are easy to
operate because of the following features.
Constant speed control
Possible to get fine finish, because the rotating speed is
kept constantly even under loaded condition.
Additionally, when the load on the tool exceeds admissi-
ble levels, power to the motor is reduced to protect the
motor from overheating. When the load returns to admis-
sible levels, the tool will operate as normal.
Soft start feature
Soft start because of suppressed starting shock.
Indication lamp (Fig. 3)
The indication lamp lights up green when the tool is
plugged. If the indication lamp does not light up, the
mains cord or the controller may be defective. The indica-
tion lamp is lit but the tool does not start even if the tool is
switched on, the carbon brushes may be worn out, or the
controller, the motor or the ON/OFF switch may be defec-
tive.
Unintentional restart proof
Even locking lever keeping the switch trigger depressed
(Lock-on position) does not allow the tool to restart even
when the tool is plugged.
At this time, the indication lamp flickers red and shows
the unintentional restart proof device is on function.
To cancel the unintentional restart proof, pull the switch
trigger fully, then release it.
ASSEMBLY
CAUTION:
• Always be sure that the tool is switched off and
unplugged before carrying out any work on the tool.
Installing side grip (handle) (Fig. 4)
CAUTION:
• Always be sure that the side grip is installed securely
before operation.
Screw the side grip securely on the position of the tool as
shown in the figure.
Installing or removing wheel guard (For
depressed center wheel, multi disc, wire wheel
brush / abrasive cut-off wheel, diamond wheel)
WARNING:
• When using a depressed center grinding wheel/Multi-
disc, flex wheel or wire wheel brush, the wheel guard
must be fitted on the tool so that the closed side of the
guard always points toward the operator.
• When using an abrasive cut-off / diamond wheel, be
sure to use only the special wheel guard designed for
use with cut-off wheels.
For tool with locking screw type wheel guard (Fig. 5)
Mount the wheel guard with the protrusion on the wheel
guard band aligned with the notch on the bearing box.
Then rotate the wheel guard around 180 degrees coun-
terclockwise. Be sure to tighten the screw securely. To
remove wheel guard, follow the installation procedure in
reverse.
For tool with clamp lever type wheel guard
(Fig. 6 & 7)
Loosen the lever on the wheel guard. Mount the wheel
guard with the protrusion on the wheel guard band
aligned with the notch on the bearing box. Then rotate
the wheel guard around to the position shown in the fig-
ure. Tighten the lever to fasten the wheel guard. If the
lever is too tight or too loosen to fasten the wheel guard,
loosen or tighten the nut to adjust the tightening of the
wheel guard band.
To remove wheel guard, follow the installation procedure
in reverse.
Installing or removing depressed center grinding
wheel/Multi-disc (accessory)
WARNING:
• Always use supplied guard when depressed center
grinding wheel/Multi-disc is on tool. Wheel can shatter
during use and guard helps to reduce chances of per-
sonal injury.
Mount the inner flange onto the spindle. Fit the wheel/
disc on the inner flange and screw the lock nut onto the
spindle.
(Fig. 8)
NOTE:
• When using a more than 7 mm thick depressed center
grinding wheel, overturn the lock nut and screw it onto
the spindle.
Super flange
Models with the letter F are standard-equipped with a
super flange. Only 1/3 of efforts needed to undo lock nut,
compared with conventional type.
Summary of Contents for GA7012C
Page 2: ...2 1 2 3 4 5 6 7 8 11 12 13 14 6 9 10 8 9 10 6 7 8 5 4 3 A B C 2 1 ...
Page 3: ...3 9 10 11 12 13 14 15 20 11 18 19 11 22 13 23 21 A B 15 11 15 13 45 102 16 17 ...
Page 4: ...4 17 16 18 19 32 31 28 29 30 26 27 11 24 22 25 45 78 23 78 ...
Page 79: ...79 ...
Page 80: ...Makita Corporation Anjo Aichi Japan www makita com 884938B992 IDE ...