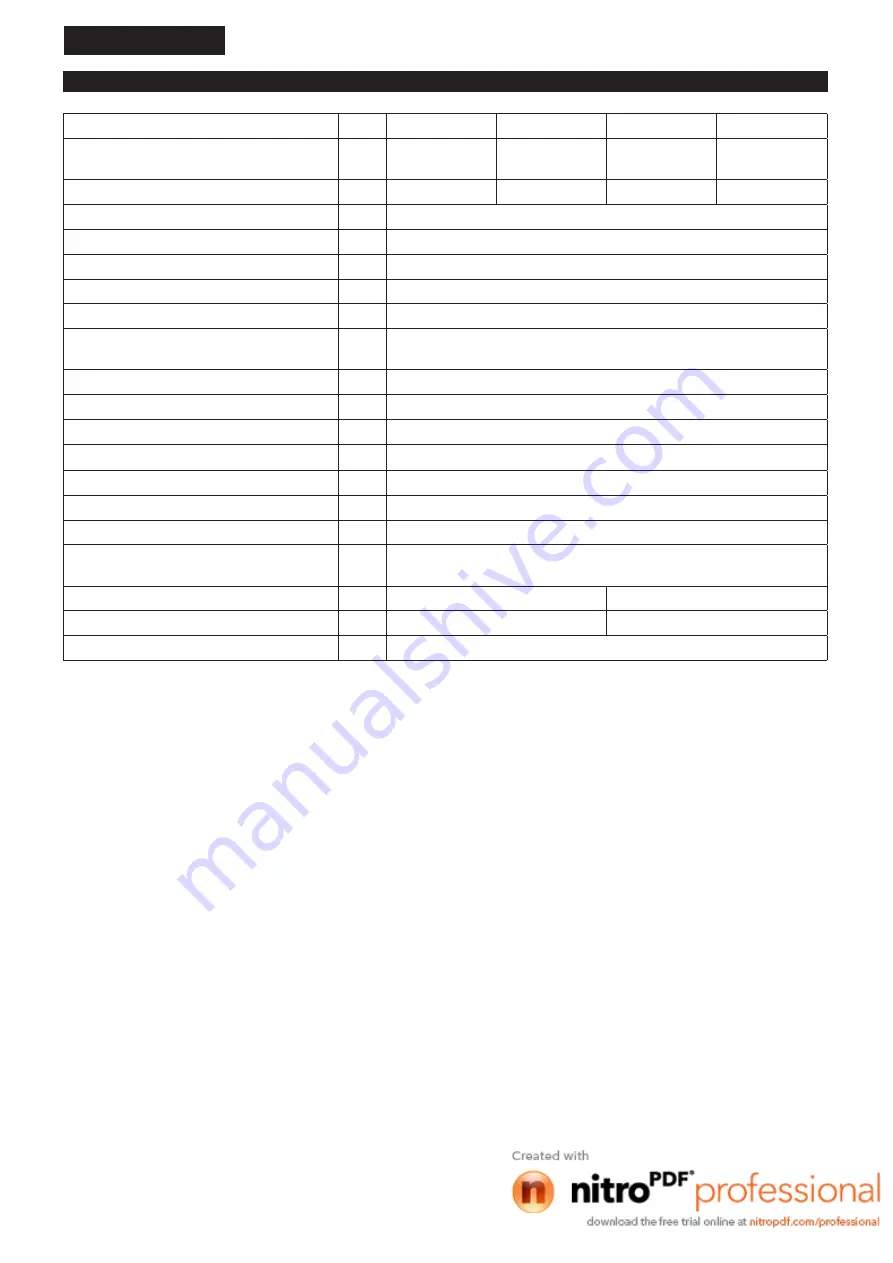
2
English
(Original instructions)
TECHNICAL DATA
Model
EM2510LH
EM2511LH
EM2510LHC
EM2511LHC
Dimensions: length x width x height (without
cutting tool)
mm 1,757 x 368 x 286 1,766 x 368 x 286 1,757 x 305 x 302 1,766 x 305 x 302
Weight (without plastic guard and cutting tool)
kg
5.3
5.4
5.3
5.4
Engine type
Air cooled, 4-stroke, single cylinder
Volume (fuel tank)
L
0.5
Volume (oil tank)
L
0.08
Engine displacement
cm
3
24.5
Maximum engine performance
kw
0.71 at 7,000 min
-1
Engine speed at recommended max. spindle
speed
min
-1
8,500
Maximum spindle speed (corresponding)
min
-1
6,500
Idling speed
min
-1
3,000
Clutch engagement speed
min
-1
3,750
Carburetor
Diaphragm type
Spark plug
type
NGK CMR4A
Electrode gap
mm
0.7 - 0.8
Fuel
Automobile gasoline (petrol)
Engine Oil
API grade SF class or higher, SAE 10W-30 oil
(automobile 4-stroke engine oil)
Cutting tool diameter (with metal blade)
mm
230
–
Cutting tool diameter (with nylon cutting head)
mm
420
420
Gear ratio
14/19
• Due to our continuing program of research and development, the specifications herein are subject to change without notice.
• Specifications may differ from country to country.