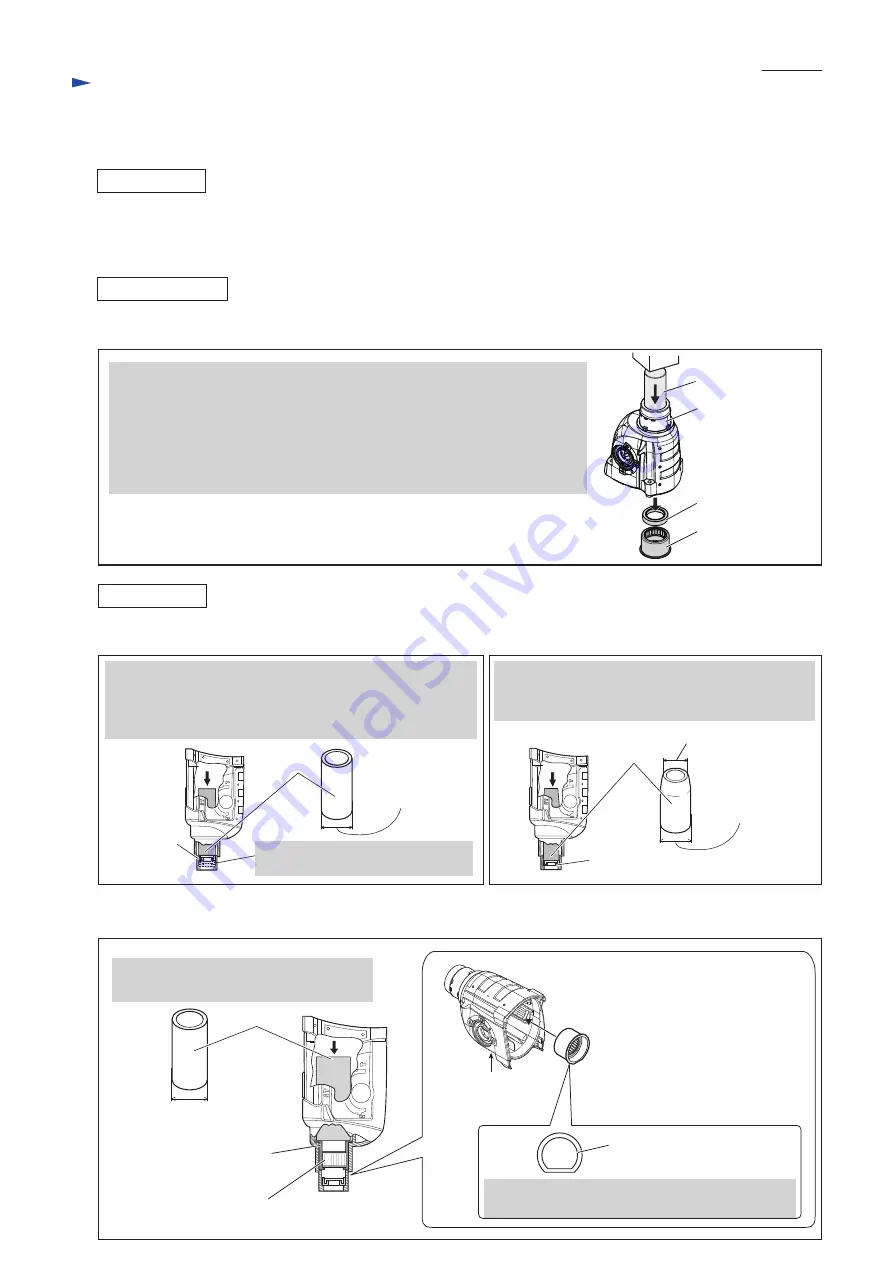
P 14/ 22
R
epair
[3] DISASSEMBLY/ASSEMBLY
[3]-5. Tool holder section of DHR263
Tool holder guide section of DHR264 (cont.)
ASSEMBLING
DISASSEMBLING
Fig. 28
(1) Assemble Spur gear 51, Compression spring 32 and Washer 31 to Tool holder (guide). (
Fig. 27
)
(2) Using repairing jigs of 1R249 and 1R369, secure the parts with Ring spring 29. (
Fig. 27
)
Put Gear housing complete on Arbor press table, and keep it upright. Then,
by pressing down Oil seal 25 using 1R252, Oil seal 25 and Needle bearing
complete can be removed from Gear housing complete
with gentle pressure
.
Note
: On Arbor press table, Gear housing complete can stand almost upright
on its end edges. Although the end edges are rather thin, you need not
worry about breakage because Oil seal 25 and Needle bearing complete
are fitted to Gear housing complete with low press fit force.
1R252
Oil seal 25
Gear housing
complete
Needle bearing
complete
[3]-6. Needle bearing complete and Oil seal 25
(1) Assemble Oil seal 25 to Gear housing complete. (
Figs. 29
and
30
)
Disassemble Needle bearing complete. (
Fig. 28
)
1R164
Outer diameter: 30mm
Outer
Diameter: 34mm
Oil seal 25
With 1R232 and Arbor press, insert Oil seal 25 until it stops.
In this step, Oil seal 25 is not yet inserted completely
because the outer diameter of 1R232 is larger than that of
Oil seal setting hole.
original position of Oil seal 25
Fig. 29
Fig. 30
Using Arbor press and the 34mm outer diameter end
of 1R164, press down Oil seal 25 until it stops at its
original position.
ASSEMBLING
Fig. 31
(2) Assemble Needle bearing complete. (
Fig. 31
)
Outer diameter: 30mm
1R165
With 1R165 and Arbor press, press down
Needle bearing complete until it stops.
Needle bearing portion of
Needle bearing complete
Cup washer portion of
Needle bearing complete
Face the flat portion of Needle bearing complete
towards the bottom side of Gear housing complete.
bottom side of
Gear housing
complete
Needle bearing complete
[view from rear side]
Note
:
1) Do not use 1R164 in this step.
2) Do not press
Needle bearing
portion
directly.
3) Too much pressure will deform
Needle bearing complete.
Do not press hard.
4) Be sure to press
Cup washer
portion
with gentle pressure.
1R232
Outer
diameter: 36mm
The diameter of Oil seal 25 setting
hole is smaller than 36mm.