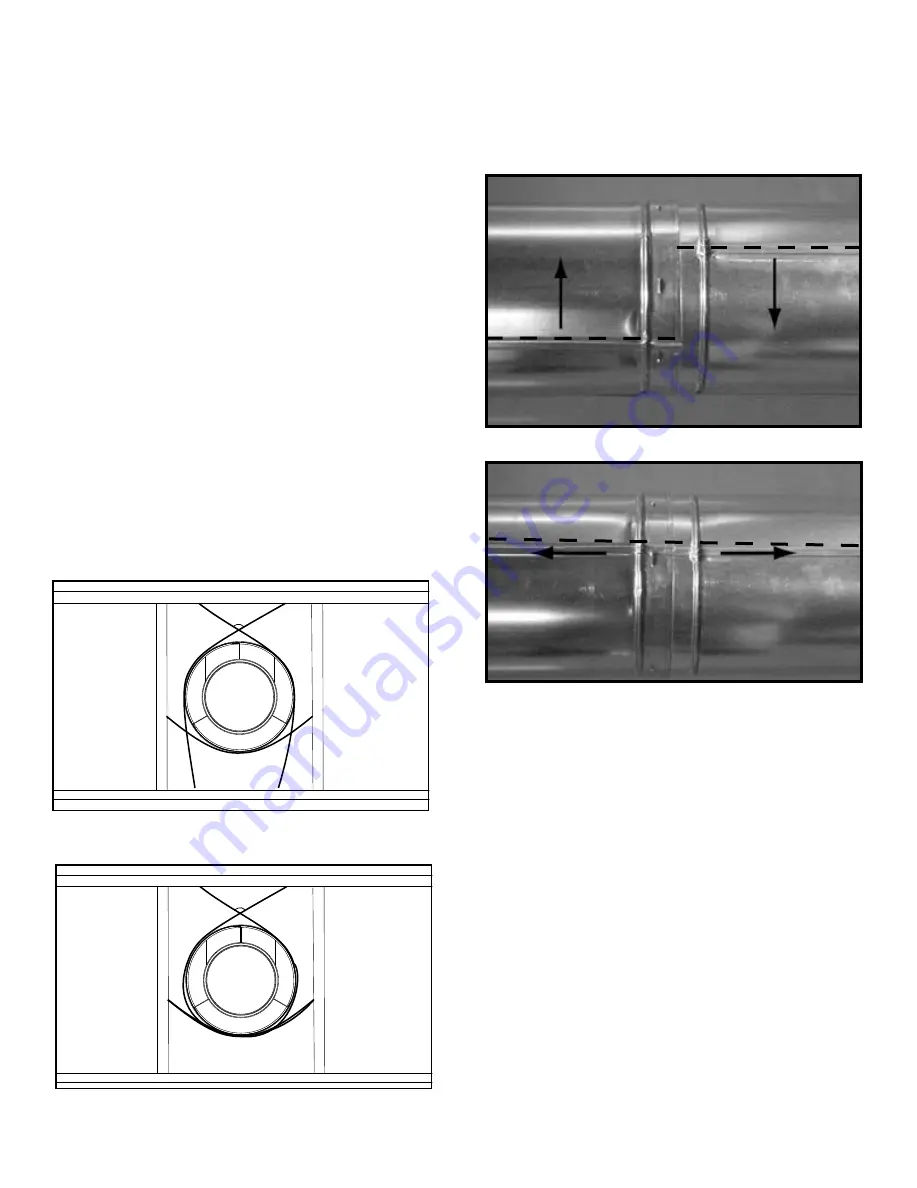
Majestic • MER36MN, MER42MN Installation Manual • 2599-980 Rev. B • 5/23
48
120º
Figure 7.8 Securing Vertical Pipe Sections
120º
Figure 7.9 Securing Horizontal Pipe Sections
D. Disassemble Vent Sections
• Rotate either section (see Figure 7.10) so the seams on
both pipe sections are aligned as shown in Figure 7.11.
• Pull carefully to separate the pieces of pipe.
Figure 7.11 Align and Disassemble Vent Sections
Figure 7.10 Rotate Seams for Disassembly
C. Secure the Vent Sections
WARNING!
Risk of Fire, Explosion or Asphyxiation!
Improper support could allow vent to sag and separate.
Use vent run supports and connect vent sections per in-
stallation instructions.
DO NOT
allow vent to sag below
connection point to appliance.
• Vertical runs originating off the top of the appliance, with
no offsets, must be supported every 8 feet (2.44 m) after
the maximum allowed 25 feet (7.62 m) of unsupported
rise.
• Vertical runs originating off the rear of the appliance, or
after any elbow, must be supported every 8 feet (2.44
m).
• Horizontal runs must be supported every 5 feet (1.52 m).
• Vent supports or plumbers strap (spaced 120º apart)
may be used to support vent sections. See Figures 7.8
and 7.9.
Note:
Figures 7.8 and 7.9 are to be used for reference
only. Method of strap installation could vary by
configuration of vent system.
• Wall shield firestops may be used to provide horizontal
support to vent sections.
• SLP ceiling firestops have tabs that may be used to
provide vertical support.