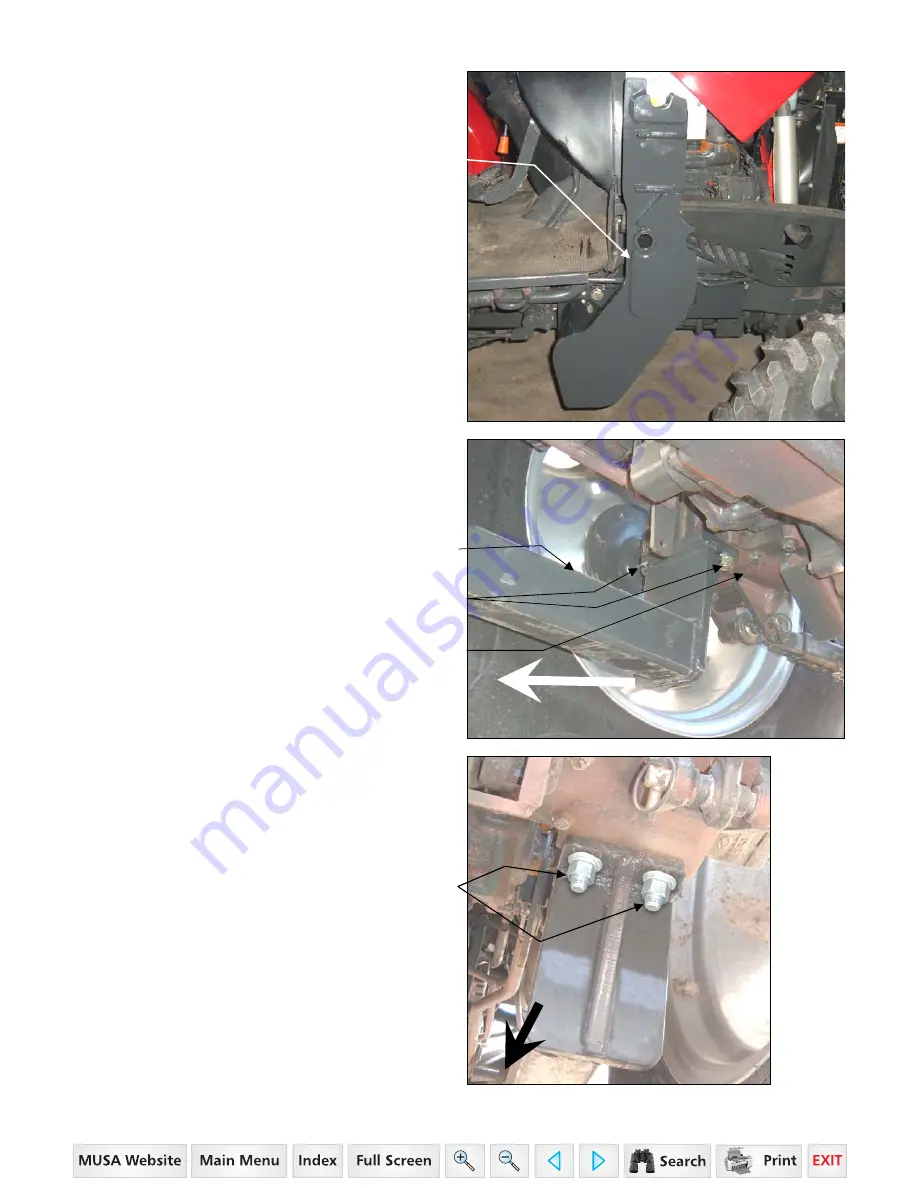
20
Photo shows overall view of installed right hand
center bracket
3.2.6. Remove nuts and lockwashers from front two
bolts on 3-point link plate located on the tractor right
rear axle housing. Install RH rear rail over two 3-point
link plate bolts and secure with hardened flatwasher
5/8” supplied with loader on slotted hole and link plate
hardware removed.
RH Rear Rail
Secure using Hardened Flatwasher 5/8” and
3-Point Link Plate hardware
3-Point Link Plate
Secure using Hardened Flatwasher
supplied with loader and 3-Point Link Plate
hardware
Front of tractor
Front view
Rear view
Front of tractor
35 Series 4WD, Model - 3535 & 4035 Loader June’08