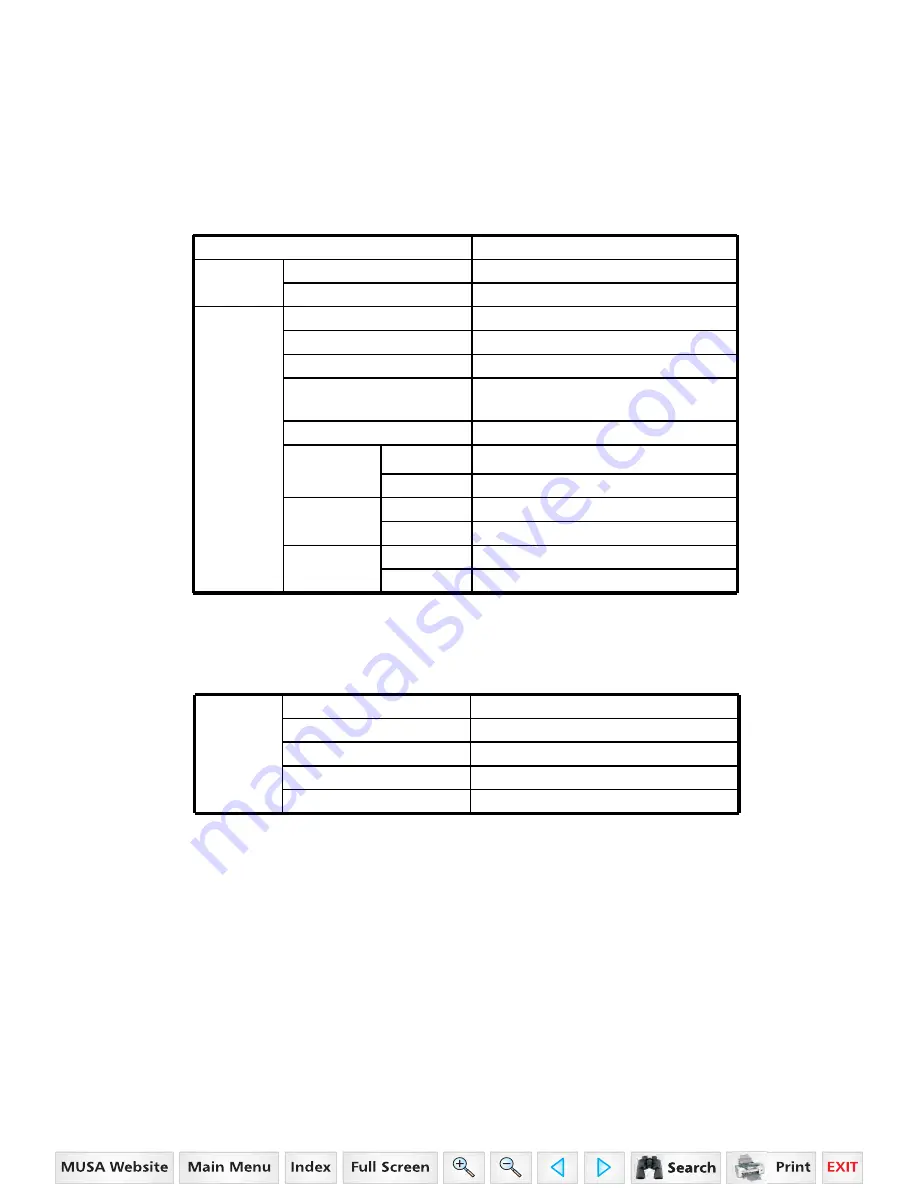
MODEL
4010 HST
Clutch
Main
Damper
PTO
Multiple wet disk
Dimensions
Overall length(mm)
3030 (119.3”)
Overall width (mm)
1520 (59.8”)
Overall Height (mm)
2400 (94.5”)
Wheel base (mm)
(Distance between shafts)
1680 (66.1”)
Min. Ground Clearance (mm)
323 (12.8”)
R1
Front
8.0-16
Rear
12.4-24
R4
Front
10-16.5
Rear
43x16.00-20
Axle type
Front
Center pin
Rear
Central axle
Implement
Operation
Hydraulic
Mounting method
3-Point hitch
Drawing method
Trailer hitch
3-Point hitch category
Category 1
Hydraulic-control
Position
79
Summary of Contents for 4010 HST
Page 2: ... Mahindra USA Inc 5203 Aeropark Drive Houston TX 77032 281 449 7771 www mahindrausa com ...
Page 33: ...DECALS ON THE CHASSIS 31 ...
Page 34: ...32 DECALS AROUND THE SEAT ...
Page 49: ... OPERATING THE 3 POINT LINKAGE TPL 47 ...
Page 89: ... POWER TRAIN 87 38PS ...
Page 91: ...DATE TRACTOR HOURS NATURE TYPE OF REPAIR SERVICE CARRIED OUT SERVICE RECORD 89 ...
Page 93: ...PART REPLACEMENT RECORD DATE PART DESCRIPTION Q TY COST DATE PART DESCRIPTION Q TY COST 91 ...
Page 103: ......
Page 105: ......
Page 106: ...1 SAFETY PRECATIONS PRECAUTIONS BEFORE OPERATION 1 2 1 ...
Page 112: ...2 EXTERIOR VIEW 2 2 SERVICING 2 3 PRECAUTIONS BEFORE OPERATION 2 ...
Page 115: ......
Page 121: ......
Page 122: ...4 DAILY CHECKS 4 2 BREAK IN 4 2 PERIODIC CHECKS 4 3 BREAK IN AND CHECKS 4 ...
Page 125: ......
Page 141: ......
Page 149: ......
Page 150: ...7 SPECIFICATIONS 7 2 SPECIFICATIONS 7 ...
Page 155: ......
Page 156: ...8 INDEX 8 2 INDEX 8 ...
Page 159: ......