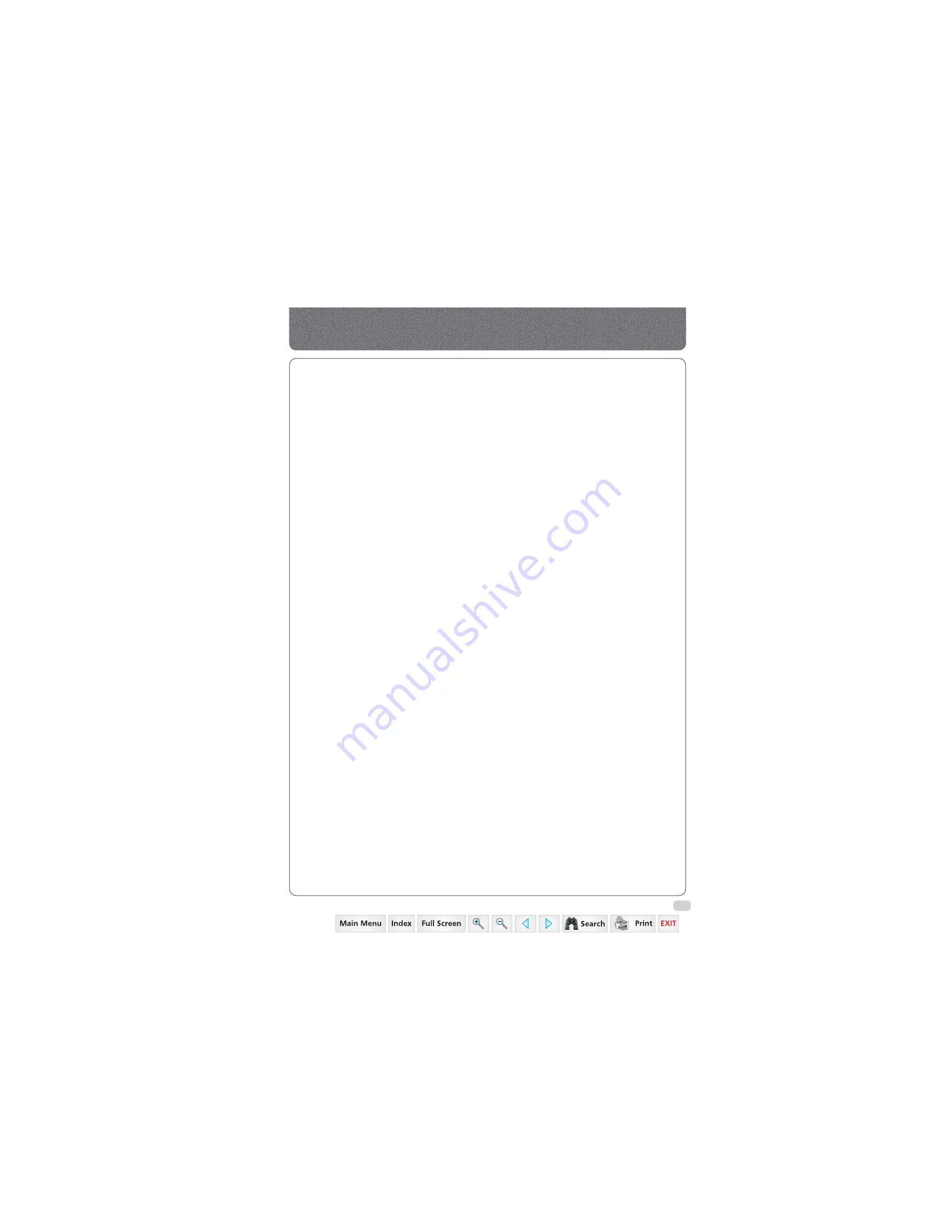
A-11
35 Series 4WD, Model - 3535, 4035, 4535 and 5035 SM June’08
General Recommendation for
disassembly and assembly operations
Before the tractor is accepted in the workshop, all
external surfaces must be thoroughly cleaned.
The service station must be clean and well lit. Strict
cleanliness must be observed when engine,
transmission and hydraulic systems are repaired.
A tractor repair shop should not be without at least
one good lifting crane so that engines and
transmissions can be removed and installed without
hazard. Suitable wooden mounting blocks, easily
accessible from all sides, on which engines and
transmissions can be placed, should be available.
They can easily be made locally.
Before dismantling, drain all water, fuel and oil from
the tractor.
It is good practice to check compression of each
cylinder before dismantling the engine to get
general ideal on the condition of the compression
building elements, such as pistons, sleeves, gaskets,
etc.
A comparison of compression readings of these
figures will disclose errors or show improvements.
Whenever reference is made to “Cleaning” in the
various sections of this book it should be taken
mean thorough cleaning i.e. complete removal oil,
grease, impurities, foreign matter and burr etc.
Even the smallest contaminants may cause serious
trouble!
Follow the disassembly and assembly procedures
in this book. They are based on years of practical
experience and provide the quickest reliable repair
procedure.
After removing oil, grease, etc., arrange parts on
a clean table in the order in which they belong to
prevent confusion later. A suitable installation to
remove oil, grease, dirt etc. from parts should be
available in every tractor repair shop.
A small boiler and a good solvent are ideal for this
purpose.
Before reassembly, carefully inspect all parts whether
they can be re-used. Ball and roller bearings must
be washed in kerosene. Before reassembly, carefully
inspect all parts to see whether they can be re-used.
Replace if necessary.
Ball bearings must be thoroughly cleaned and well
dried before inspection. To determine the degree
of wear on a ball bearing, hold the inner race with
your hand and spin the outer race. The sound
emitted by a good ball bearing is very weak and
similar to that of finger tips gliding over glossy
paper. A badly worn bearing makes a rattling,
chain-like noise.
Do not remove the original oil paper wrapping from
new ball bearings until just before sliding them on
shafts. The grease coating applied by the bearing
factory must not be removed unless this is necessary
for cleanliness reasons.
Warm press-fit ball bearings in clean 80
0
C (175
0
F)
oil and slide them on shafts as quickly as possible.
When assembling, apply some transmission oil to
all moving parts, especially to bearings, to provide
an oil film until the regular pressure feed lubrication
takes over.
In order to eliminate errors all steps, such as
adjustments, settings, and the various phases of
assembly and disassembly procedures, must be
considered without haste and with common sense.
It is better to check three times than commit one
error.
Put all new felt seals and gaskets in 50
0
C. (122
0
F)
warm oil and allow to soak before installing them.
Apply some soft soap or soap solution to all rubber
hose connections before installation.
Always install oil seal with the sealing lip towards
the oil side. Prior to assembly apply some engine
oil to the sealing lip. Generally oil seals are a press
fit in their bores and the steel casing is slightly
compressed in assembly. Used oil seals have lost
tension and the required pressfit can no longer be
obtained. For this reason, never reuse oil seals even
though the sealing lip may still be in good
condition. Should an emergency arise, install the
reused oil seal with some liquid sealer.
Expansion plugs should be oil tight. Use some
sealing compound and fit the plug with its concave
side out. Spread the plug by driving carefully on
its center with suitable installing tool.
General
Summary of Contents for 3535
Page 1: ...Click here to go on INDEX SERVICE MANUAL 3535 4035 4535 5035 GEAR 35 Series 4WD Main Page ...
Page 5: ......
Page 6: ...35 Series 4WD Model 3535 4035 4535 and 5035 SM June 08 Group A G e n e r a l General A1 A21 ...
Page 7: ......
Page 26: ......
Page 58: ......
Page 59: ...35 Series 4WD Model 3535 4035 4535 and 5035 SM June 08 CHAPTER 1 INTRODUCTION ...
Page 60: ......
Page 74: ......
Page 76: ......
Page 86: ......
Page 88: ......
Page 96: ......
Page 97: ...35 Series 4WD Model 3535 4035 4535 and 5035 SM June 08 CHAPTER 4 LUBRICATION SYSTEMS ...
Page 98: ......
Page 102: ......
Page 104: ......
Page 110: ......
Page 112: ......
Page 124: ......
Page 126: ......
Page 133: ...35 Series 4WD Model 3535 4035 4535 and 5035 SM June 08 CHAPTER 8 COOLING SYSTEM ...
Page 134: ......
Page 143: ...35 Series 4WD Model 3535 4035 4535 and 5035 SM June 08 CHAPTER 9 AIR CLEANER ...
Page 144: ......
Page 149: ...35 Series 4WD Model 3535 4035 4535 and 5035 SM June 08 CHAPTER 10 FUEL SYSTEM ...
Page 150: ......
Page 168: ...35 Series 4WD Model 3535 4035 4535 and 5035 SM June 08 Group D C l u t c h Clutch D1 D10 ...
Page 169: ......
Page 179: ......
Page 180: ...35 Series 4WD Model 3535 4035 4535 and 5035 SM June 08 CHAPTER 1 TRANSMISSION ...
Page 181: ......
Page 200: ...35 Series 4WD Model 3535 4035 4535 and 5035 SM June 08 CHAPTER 2 REAR AXLE ...
Page 201: ......
Page 208: ...35 Series 4WD Model 3535 4035 4535 and 5035 SM June 08 CHAPTER 3 DIFFERENTIAL ...
Page 209: ......
Page 222: ...35 Series 4WD Model 3535 4035 4535 and 5035 SM June 08 CHAPTER 4 DIFFERENTIAL LOCK SYSTEM ...
Page 223: ......
Page 227: ......
Page 228: ...35 Series 4WD Model 3535 4035 4535 and 5035 SM June 08 CHAPTER 5 REAR PTO COVER ...
Page 229: ......
Page 231: ......
Page 232: ...35 Series 4WD Model 3535 4035 4535 and 5035 SM June 08 CHAPTER 6 WET CLUTCH PTO ...
Page 233: ......
Page 236: ...35 Series 4WD Model 3535 4035 4535 and 5035 SM June 08 CHAPTER 7 BRAKES ...
Page 237: ......
Page 243: ......
Page 245: ......
Page 270: ......
Page 296: ...Wiring Diagram 35 Series G 28 35 Series 4WD Model 3535 4035 4535 and 5035 SM June 08 ...
Page 298: ......
Page 303: ...H 7 35 Series 4WD Model 3535 4035 4535 and 5035 SM June 08 STEERING SYSTEM CIRCUIT Steering ...
Page 316: ......
Page 318: ......
Page 358: ......
Page 359: ......
Page 367: ...Range Section Transmission ...