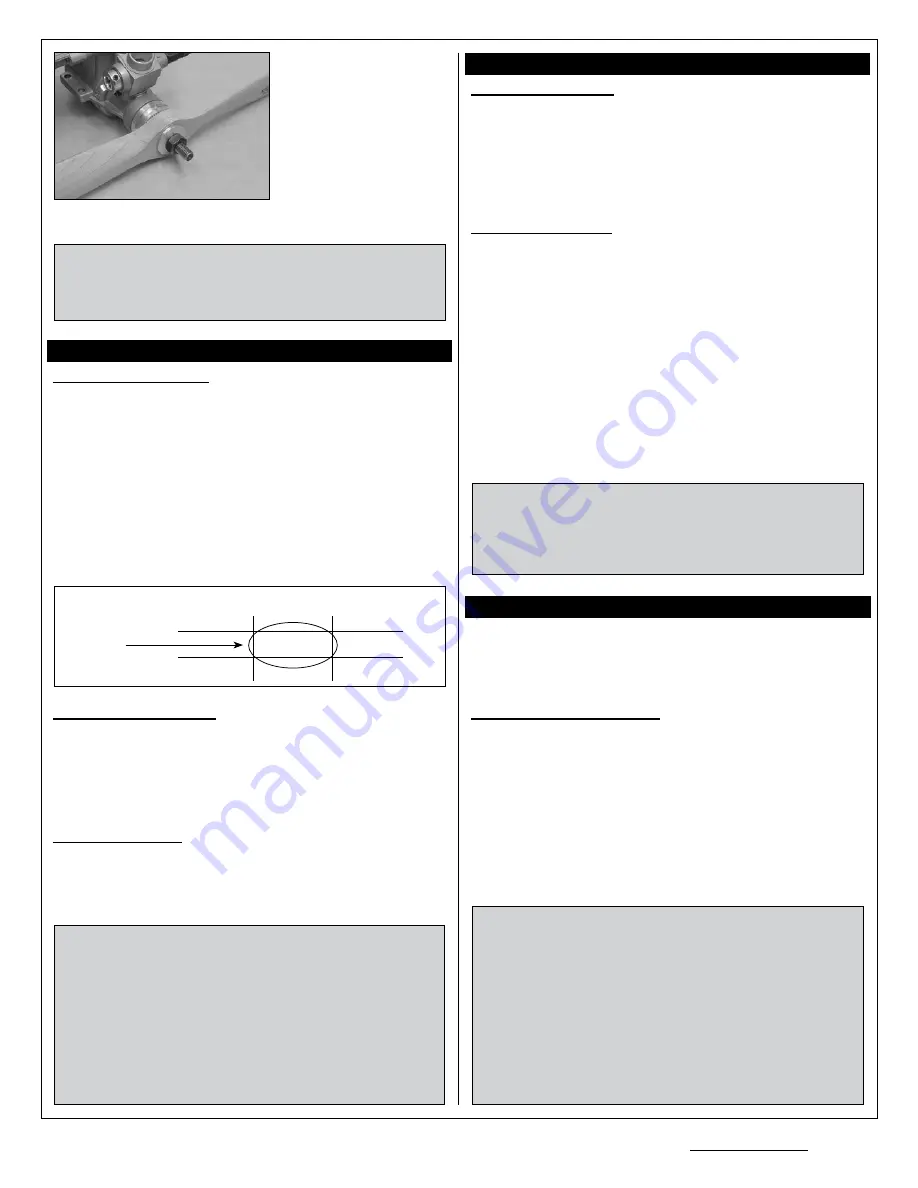
Global Services
l
18480 Bandilier Circle
l
Fountain Valley, CA 92708
l
Phone: (714) 963-0329
l
Fax: (714) 964-6236
l
Email: [email protected]
Using a 1/4" drill bit or a propeller
reamer, enlarge the hole in the
propeller hub to fit the crankshaft.
Slide the propeller onto the
crankshaft, up against the drive
washer, then slide the propeller
washer up against the propeller
and thread the propeller nut into
place. Tighten the propeller nut
firmly to secure the propeller into place. When tightening the propeller nut,
use an adjustable wrench or a 4-way wrench. Do not use pliers.
WARNING
If you are installing a spinner onto your engine, the spinner
cone must not rub against the propeller. Allowing the spinner cone to
rub against the propeller could lead to propeller damage and eventual
propeller failure.
Your XLS series engine can be started using an electric starter or it can
be started by hand. For safety and ease of starting, especially when the
engine is new, we recommend using an electric starter.
The following
two procedures should be done with the power to the glow plug off.
WARNING ABOUT ENGINE HYDRO-LOCKING
If the engine becomes hydro-locked, do not force the propeller through the
compression stroke. The excess fuel should be expelled from the engine.
l
Completely close the high speed needle valve until it bottoms out, then
remove the glow plug from the cylinder head.
l
With a rag over the top of the engine, turn the crankshaft several times,
using your electric starter or flipping the propeller by hand. The excess
fuel will be expelled out of the engine and into the rag.
l
Check to make sure that the glow plug has not been fouled, then reinstall
it and reset the high speed needle valve.
Low Speed Needle Valve
The low speed needle valve is preset from the factory for initial starting and
break-in.
Do not adjust it until after the engine is broken in.
The low speed
needle valve regulates the air/fuel mixture at idle and during transition from
idle to full throttle. Turn the needle valve clockwise to lean the mixture or
turn the needle valve counterclockwise to richen the mixture. The low speed
needle valve is preset from the factory, but minor adjustments may need
to be made after the engine is broken in.
To reset the low speed needle
valve to the factory setting, follow these procedures:
l
Open the throttle barrel completely.
l
While holding the throttle barrel open, turn the low speed needle valve
clockwise GENTLY until it stops. From this point, while still holding the
throttle barrel open, turn the low speed needle valve counter-clockwise 3
full turns. This is the factory setting.
WARNING
It is possible to adjust the low speed needle valve so lean
that the engine will not draw fuel. The low speed needle valve should not
need to be adjusted more than one full turn in either direction from the
factory setting. If the engine does not idle or transition, reset the low speed
needle valve to the factory setting.
STARTING PROCEDURE
Starting Using an Electric Starter
It's best to use an electric starter only when your engine as a spinner installed.
Prior to use, make sure that the electric starter is turning counter-clockwise.
When using an electric starter it is not necessary to prime the engine. The
starter turns the engine over fast enough that the engine draws fuel on its
own. Priming the engine prior to using an electric starter can cause the
engine to hydro-lock (flood).
Turning the engine over with an electric
starter while the engine is flooded can cause extreme damage to the
engine and/or cause the propeller assembly to come loose. Turn the
propeller through the compression stroke one time by hand to check
for a hydro-locked state before applying the starter.
3
PROPELLER, GLOW PLUG AND FUEL
Propeller Recommendation
The diameter and pitch of the propeller needed for the XLS .52A engine will
vary greatly depending on the application the engine is used in. The weight,
drag, and the type of model and how you intend to fly it are all factors
in determining the correct size propeller to use. Experimentation will be
necessary to find the optimal size propeller for your particular application.
Ideally you want a propeller that the engine will turn in the 10,000 - 15,000
rpm range on the ground, yet power the aircraft sufficiently. Using a propeller
that is too small will cause the engine to run at too high an rpm. Using a
propeller that is too large will cause the engine to run at too low an rpm,
cause it to lug down too much and make tuning difficult. In both instances
this can lead to premature engine wear and eventual failure.
PROPELLER SIzE RECOmmENDATIONS
Use for
Break-In
10 x 6
9 x 6
10 x 5 - 8
11 x 4 - 8
12 x 3 -6
Glow Plug Recommendation
Glow plugs can make a big difference in the performance of your engine.
We recommend using a long-reach, hot heat-range glow plug intended
specifically for high-performance two-stroke engines. Do not use a cold
heat-range plug and do not use glow plugs that use an idle bar. This can lead
to erratic engine runs, difficult tuning and eventual engine wear and failure.
Fuel Recommendation
Fuel can make a big difference in the way your engine performs. We
recommend using a fuel containing 10%~20% nitro and 18%~20% castor
oil/synthetic oil blend lubricant. The same fuel can be used for both break-in
and normal running. Do not use a fuel containing less the 18% oil.
IMPORTANT
We highly recommend that the first gallon of fuel run
through the engine contains either a castor oil/synthetic oil blend, or all
castor oil. Do NOT use an all-synthetic oil fuel for the break-in period.
After the first gallon of fuel, you can switch to an all-synthetic oil fuel, but
only if the fuel is of high quality. For example, some 'sport' all-synthetic
fuels use low-grade oils or oils with the wrong thermal properties (they
do not transfer heat well), and do NOT work well in Magnum engines.
If there is any question, it's always safe to use a castor oil/synthetic oil
blended fuel, regardless of brand, as long as the oil content matches what
is specified above.
HIGH AND LOW SPEED NEEDLE VALVES
High Speed Needle Valve
The high speed needle valve is used to meter the air/fuel mixture at full
throttle. Turn the needle valve clockwise to lean the mixture or turn the
needle valve counterclockwise to richen the mixture. When you start the
engine for the very first time the needle valve should be turned in completely,
then backed out 2-1/2 turns. When you start the engine after that, leave the
needle valve in the same position it was in when you shut down the engine.