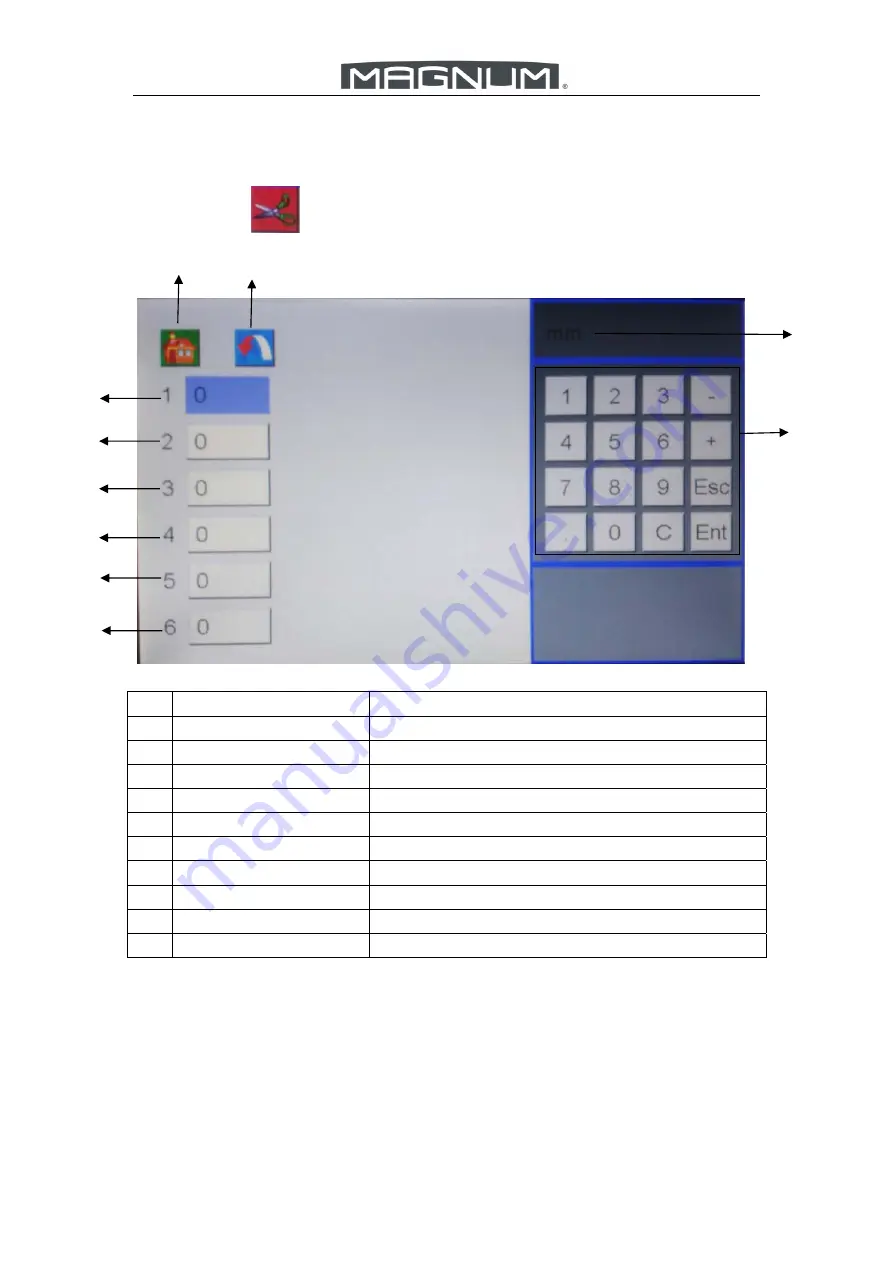
M C C - 3 5 A S
19
5.5.2.2
Slit
Setting
Press the icon
, entering slit data setting screen.
No. Description
Remark
1
Home
Back to Main Screen.
2
Return
Return to the last page
3
Unit
Data unit mm or inch.
4
Keyboard
Input all data according local request.
5
Slitter #1 Data
Set slitter #1 data
6
Slitter #2 Data
Set slitter #2 data
7
Slitter #3 Data
Set slitter #3 data
8
Slitter #4 Data
Set slitter #4 data
9
Slitter #5 Data
Set slitter #5 data
10 Slitter #6 Data
Set slitter #6 data
1
2
3
5
6
7
8
9
10
4