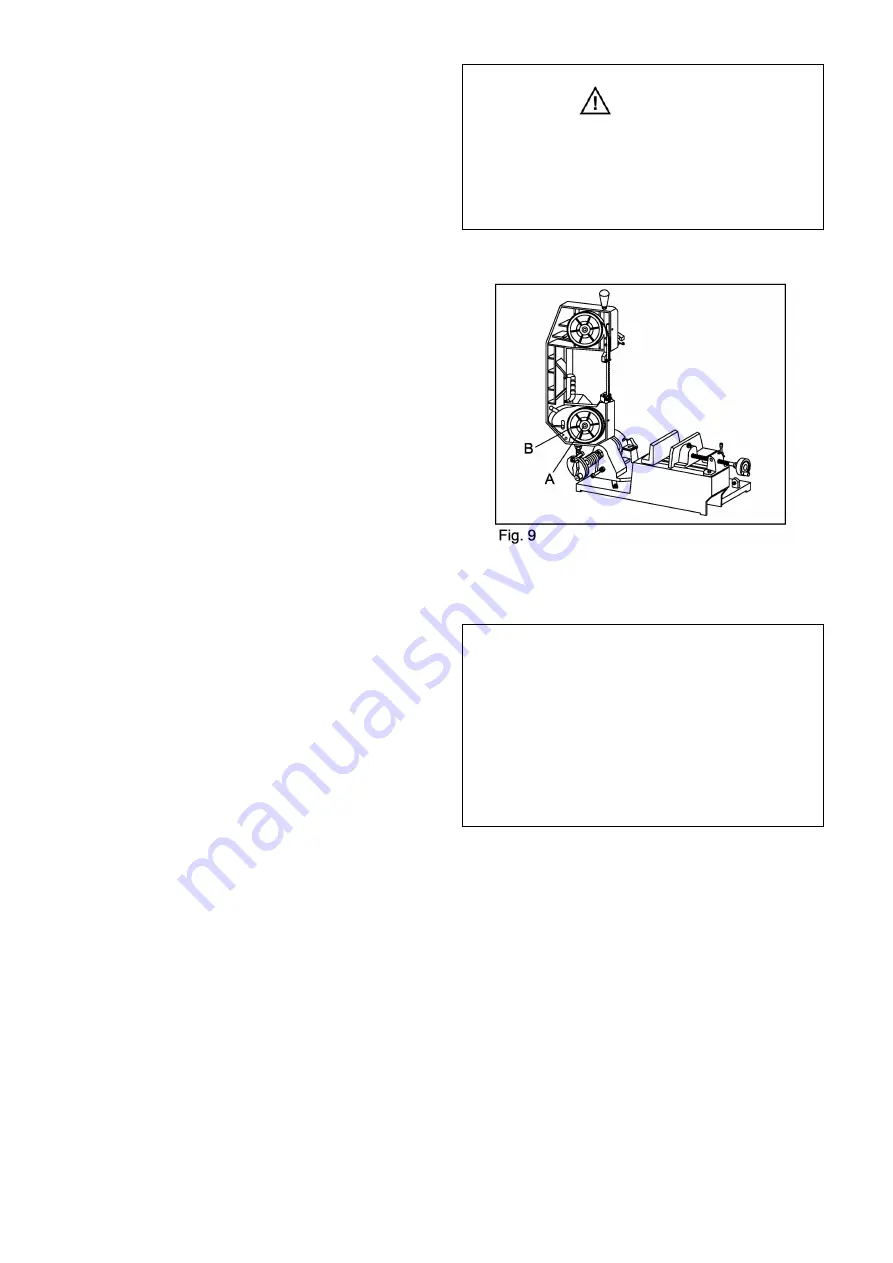
- 15 -
Maintain Gear Transmission
The gears of the transmission system
equipped with this machine are made of a
special kind of steel.
The quality insures that the gears will be
more sturdy and durable. In order to keep the
performance as perfect as they are designed
for. We suggest that a lubricant shall be
required for them every three months. To
fulfill the job, follow the steps as below.
1. Loosen the screw (A) in Fig.9 with a 8
mm Hex wrench.
2. Remove the wheel (B), then lubricate the
gears with Anti-high heat grease.
3. Replaces this wheel with care, then
tighten the screw (A) properly.
Blade Tension Adjustment
The tension device of this machine is
designed for the ready service basis. All you
have to do is hold the handle (B) in Fig.8 to
control blade tension by giving turn to
increase or decrease tension as you wish
during machine in operation. The major
function of it is to present a perfect cut,
because it can make the blade work on
constant tension. Furthermore, attached with
the tension system, there are a couple of
compression springs which are made for
decreasing the blade backlash.
Consequently, it is for sure to extend life of
the blade.
WARNING
SHUT OFF THE POWER SOURCE
BEFORE THIS MACHINE IS IN
ADJUSTMENT, MAINTENANCE, OR
REPAIRMENT.
BEFORE STARTING
MAKE SURE UNHOOK THE LOCK
CHAIN BETWEEN THE SAW ARM AND
BED TO RELEASE THE SAW. AFTER
SERVICE, REMEMBER IT MUST BE
REPLACED BACK FOR SAFETY AND
EASY CARRYING.
Summary of Contents for MI-93050
Page 4: ...2 Electrical Schematic Wiring Diagram Toggle Switch Single Phase...
Page 21: ...19...
Page 22: ...20...