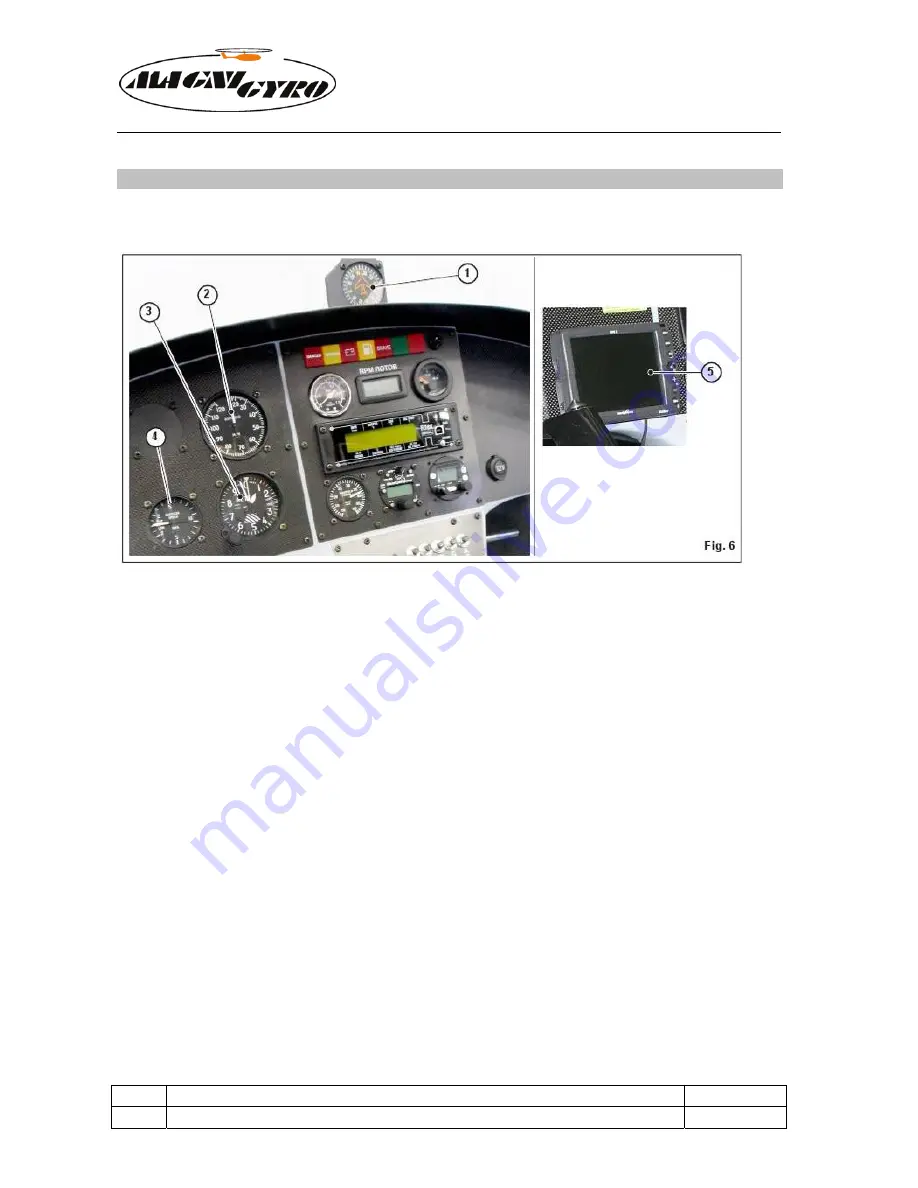
M24C_AUS
M24C FLIGHT MANUAL
.
PAGE
ISSUE B
24
December
2011
2.6 INSTRUMENTS AND CONTROLS
2.6.a INSTRUMENTS (Fig.6)
COMPASS (1)
A standard magnetic compass is installed on the upper part of the instrument panel, in the panel’s centre
line.
AIR-SPEED INDICATOR (ASI) (2)
The air-speed indicator has a range between 0 and 120 mph. (20-120 Kn when in Knots) The indicated
speed is derived from the difference between dynamic pressure and static pressure.
The Pitot tube is located at the front of the fuselage.
The static intake is connected to the two static ports located on the side of the fuselage.
ALTIMETER (ALT) (3)
Three-pointer altimeter with 0 - 20.000 ft scale.
The indicator is supplied with a barometric scale (in
millibar) to adjust for atmospheric pressure.
Pressure is monitored through the static port.
VERTICAL SPEED INDICATOR (VSI) (4) (Optional)
The vertical speed indicator is an optional instrument. It is positioned next to the altimeter. This instrument
is calibrated in ft/min. It is connected to the static head port.
GPS EQUIPMENT (Optional) (5)
The position and type of GPS equipment (global positioning system) is left to the user’s discretion.
The operator manual of the GPS is supplied together with the equipment.
Summary of Contents for M-24C Orion
Page 9: ...M24C_AUS M24C FLIGHT MANUAL ISSUE B PAGE December 2011 9 SECTION INTRODUCTION 1 ...
Page 37: ...M24C_AUS M24C FLIGHT MANUAL ISSUE B PAGE December 2011 37 SECTION OPERATING LIMITS 3 ...
Page 39: ...M24C_AUS M24C FLIGHT MANUAL ISSUE B PAGE December 2011 39 ...
Page 44: ...M24C_AUS M24C FLIGHT MANUAL PAGE ISSUE B 44 December 2011 INTENTIONALLY LEFT WHITE ...
Page 45: ...M24C_AUS M24C FLIGHT MANUAL ISSUE B PAGE December 2011 45 SECTION FLIGHT PROCEDURE 4 ...
Page 72: ...M24C_AUS M24C FLIGHT MANUAL PAGE ISSUE B 72 December 2011 ...
Page 89: ...M24C_AUS M24C FLIGHT MANUAL ISSUE B PAGE December 2011 89 SECTION EMERGENCY PROCEDURES 5 ...
Page 94: ...M24C_AUS M24C FLIGHT MANUAL PAGE ISSUE B 94 December 2011 ...
Page 96: ...M24C_AUS M24C FLIGHT MANUAL PAGE ISSUE B 96 December 2011 ...
Page 101: ...M24C_AUS M24C FLIGHT MANUAL ISSUE B PAGE December 2011 101 SECTION APPENDIX 7 ...
Page 102: ...M24C_AUS M24C FLIGHT MANUAL PAGE ISSUE B 102 December 2011 INTENTIONALLY LEFT WHITE ...
Page 106: ...M24C_AUS M24C FLIGHT MANUAL PAGE ISSUE B 106 December 2011 INTENTIONALLY LEFT WHITE ...
Page 107: ...M24C_AUS M24C FLIGHT MANUAL ISSUE B PAGE December 2011 107 7 3 APPENDIX 3 ENGINE PARAMETERS ...
Page 108: ...M24C_AUS M24C FLIGHT MANUAL PAGE ISSUE B 108 December 2011 ...
Page 111: ...M24C_AUS M24C FLIGHT MANUAL ISSUE B PAGE December 2011 111 7 5 APPENDIX 5 PERFORMANCE DATA ...
Page 112: ...M24C_AUS M24C FLIGHT MANUAL PAGE ISSUE B 112 December 2011 INTENTIONALLY LEFT WHITE ...
Page 114: ...M24C_AUS M24C FLIGHT MANUAL PAGE ISSUE B 114 December 2011 INTENTIONALLY LEFT WHITE ...
Page 116: ...M24C_AUS M24C FLIGHT MANUAL PAGE ISSUE B 116 December 2011 ...