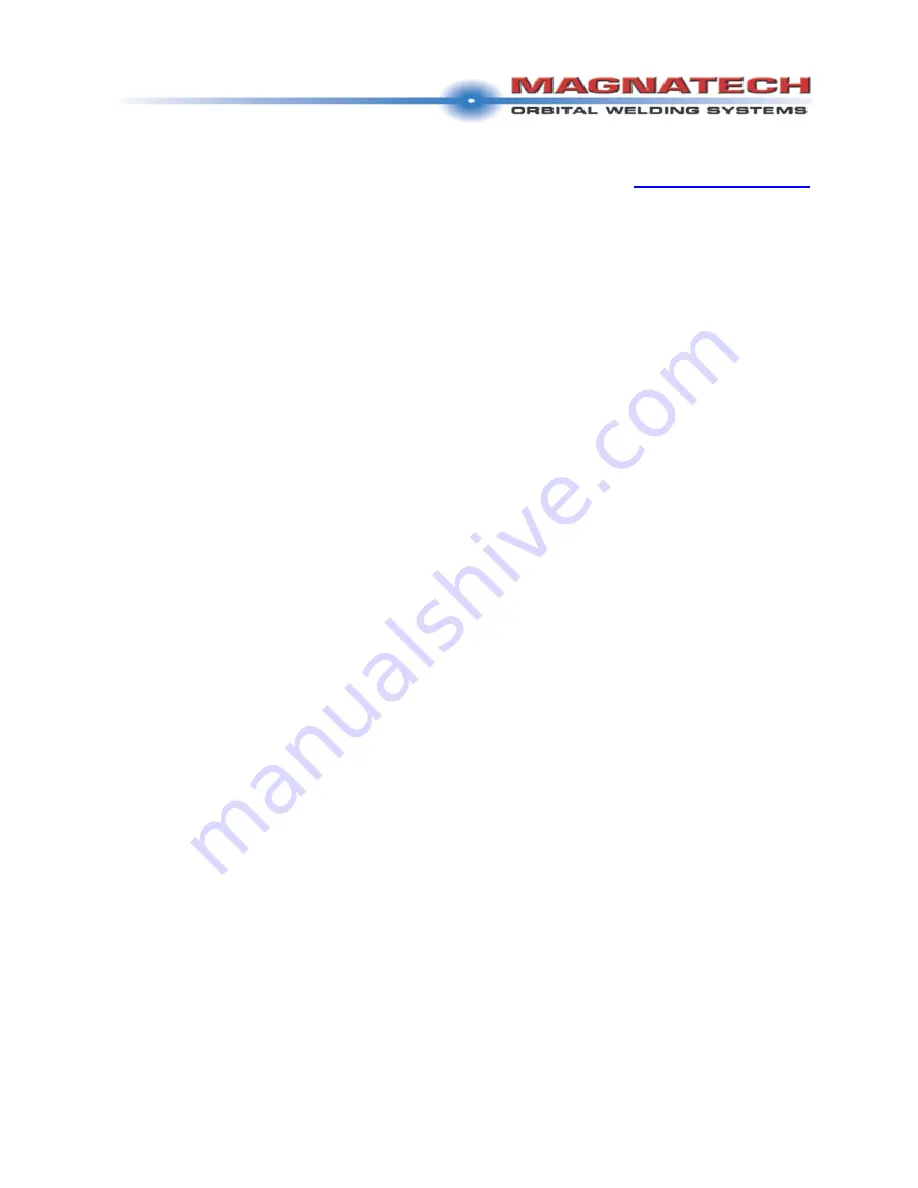
6 Kripes Road - PO Box 260 - East Granby, CT 06026 USA
Fax: (860) 653-0486
E-Mail: [email protected]
Phone: (860) 653-2573
Web:
www.magnatech-lp.com
Operating and Maintenance
Instruction Manual
For
Pipeliner II Model 609A
Orbital Weld Head
- Wire Feed on Floor (WFOF) version
- Wire Feed on Hand (WFOH version
- Wire Feed Push-pull (WFPP) version
For Use With
MPS 4000 Power Source & Model 712 Controller
(See Separate Manual)
Rev 01-14-2009
Summary of Contents for Pipeliner II 609A
Page 12: ...9...
Page 13: ...10...
Page 27: ...24...
Page 34: ...31...
Page 40: ...37 Undercutting 1 Reduce power 2 Reduce welding speed 3 Shorten arc length...
Page 43: ...40 Remote Pendant...
Page 46: ...43 14 0 ELECTRODE EXTENSION OFTEN NEGLECTED WHEN USING SELF SHIELDED CORED WIRES...
Page 47: ...44...
Page 48: ...45...
Page 49: ...46 15 0 PREVENTING THE EFFECTS OF MOISTURE CONTAMINATION OF FLUX CORE WIRE...
Page 50: ...47...