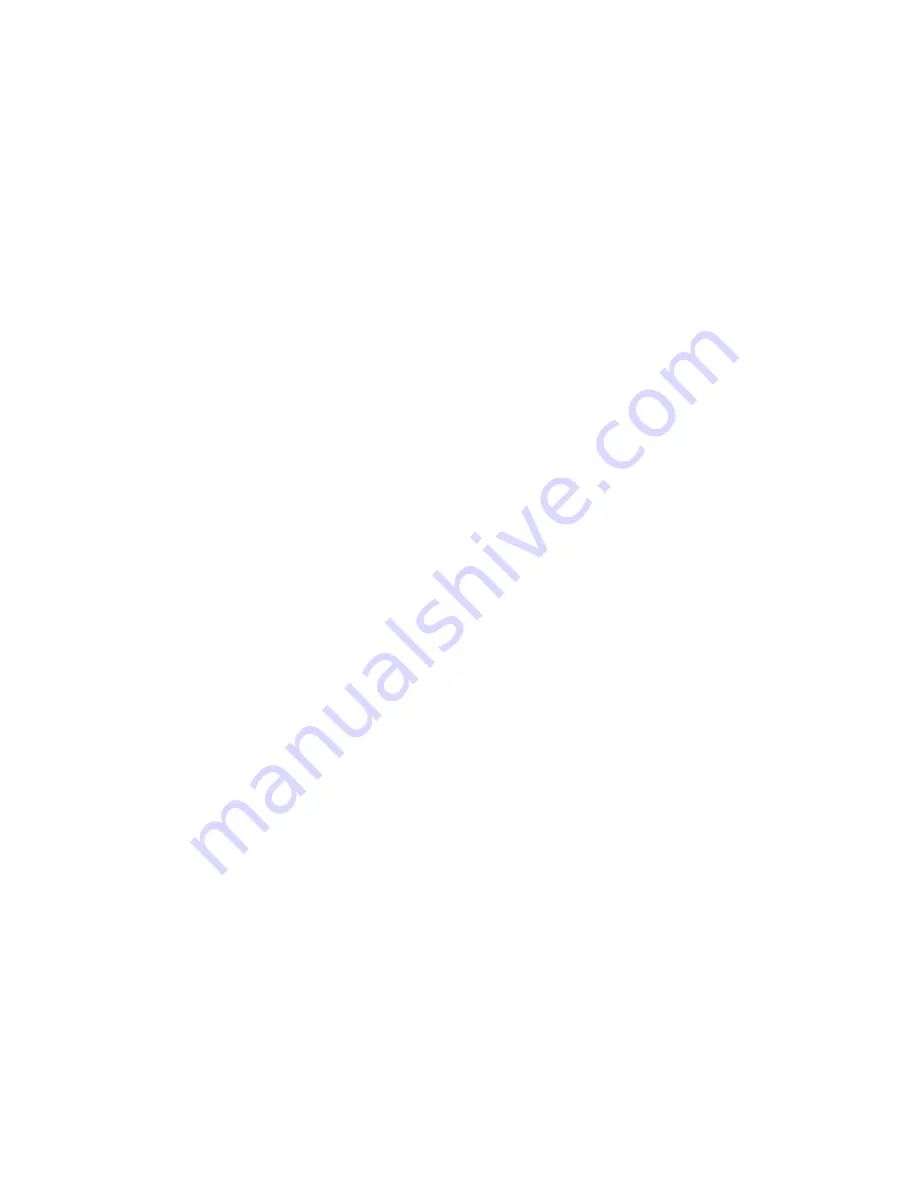
Page 16 of 19
507388-03
Issue 2127
Burner Orifices
Orifices are threaded into the gas manifold. To remove
them:
1. Remove the burner & manifold assembly as described
previously.
2. Remove the four screws securing the gas manifold to
the burner assembly.
3.
Remove the orifices by unscrewing them. Do not use
any pipe thread sealant during reassembly.
4. For reassembly, follow the above steps in reverse
order.
Combustion Inducer
The combustion inducer can be removed for inspection,
replacement, or to access the heat exchanger and flue
tube extension for cleaning. To remove the combustion
inducer:
1. Remove the control board mounting bracket as
described previously.
2. Disconnect the black inducer motor leads.
3. Disconnect the inducer prover switch tubing at the
switch.
4. Remove the two screws on the combustion inducer
plate.
5. Pull the combustion inducer and plate toward you until
it is free of the dilution air box that supports it. Lower
the inducer and plate and rotate to pull the assembly
out of the compartment.
6.
The flue tube extension can be cleaned if necessary.
Leave it in place; do not remove it from the unit.
7. For reassembly, follow the above steps in reverse
order.
Heat Exchanger
The heat exchanger should be inspected periodically and
cleaned if necessary. When cleaning use a stiff brush with
a wire handle to remove scale and soot. To access the
heat exchanger tubes for cleaning:
1. Remove the burner & manifold assembly as described
previously.
2. Remove the combustion inducer as described
previously.
3. Remove the four screws securing the dilution air box
to the flue collector box.
4. Remove the nine or twelve screws (depending on
model) securing the flue collector box to the vest panel.
5. Using the wire brush, brush out the inside of each heat
exchanger tube from the burner assembly end and
from the flue collector box end.
6.
Brush out the inside of the flue collector box.
7.
Brush out the inside of the flue tube extension.
8. If soot buildup is excessive, clean the combustion
inducer wheel and housing.
9. When brushing is complete, blow all brushed areas
with air. Vacuum as needed.
10. For reassembly, follow the above steps in reverse
order.
Cooling Chassis
The refrigeration system contained in the cooling chassis
normally requires no maintenance since it is a closed,
self-contained system. System is charged with R410A
refrigerant. Periodic maintenance is limited to:
•
Cleaning the air filter. Follow directions noted on the
filter and label attached to the access panel.
• Cleaning the condenser coil if covered with any foreign
material, lint, leaves, or other obstructions.
If servicing or major repairs are required, the complete
chassis can be removed from the unit. To remove the
chassis:
1.
Shut off the main power supply.
2.
Remove filter access panel and panel covering cooling
controls.
3. Remove drain hose from the drain pan.
4. Disconnect the plug-in electrical connections.
5. Disconnect two power leads at contactor (leads come
from grommet in unit partition).
6. Remove screws from panel directly in front of blower
and remove panel. Also remove additional screws
located near top edge of control panel.
7. Drape power wires and wire harnesses out of cabinet
and tape to upper panel.
8. Slide out the chassis, being careful not to damage any
seals or parts. Particular care should be taken to insure
wiring is not damaged during removal/reinstallation
process.
NOTE:
Tubing is not to be used as a handle.
To reinstall the chassis, reverse the procedure outlined
above. Be sure that the chassis is inserted as far back as
it will go before replacing the screws. Side flanges on the
chassis must be engaged with sealing strips on the unit
sides to prevent water and air leakage. Reconnect the
wire harness, reconnect the power leads, and replace both
access panels before turning on the main electrical power.