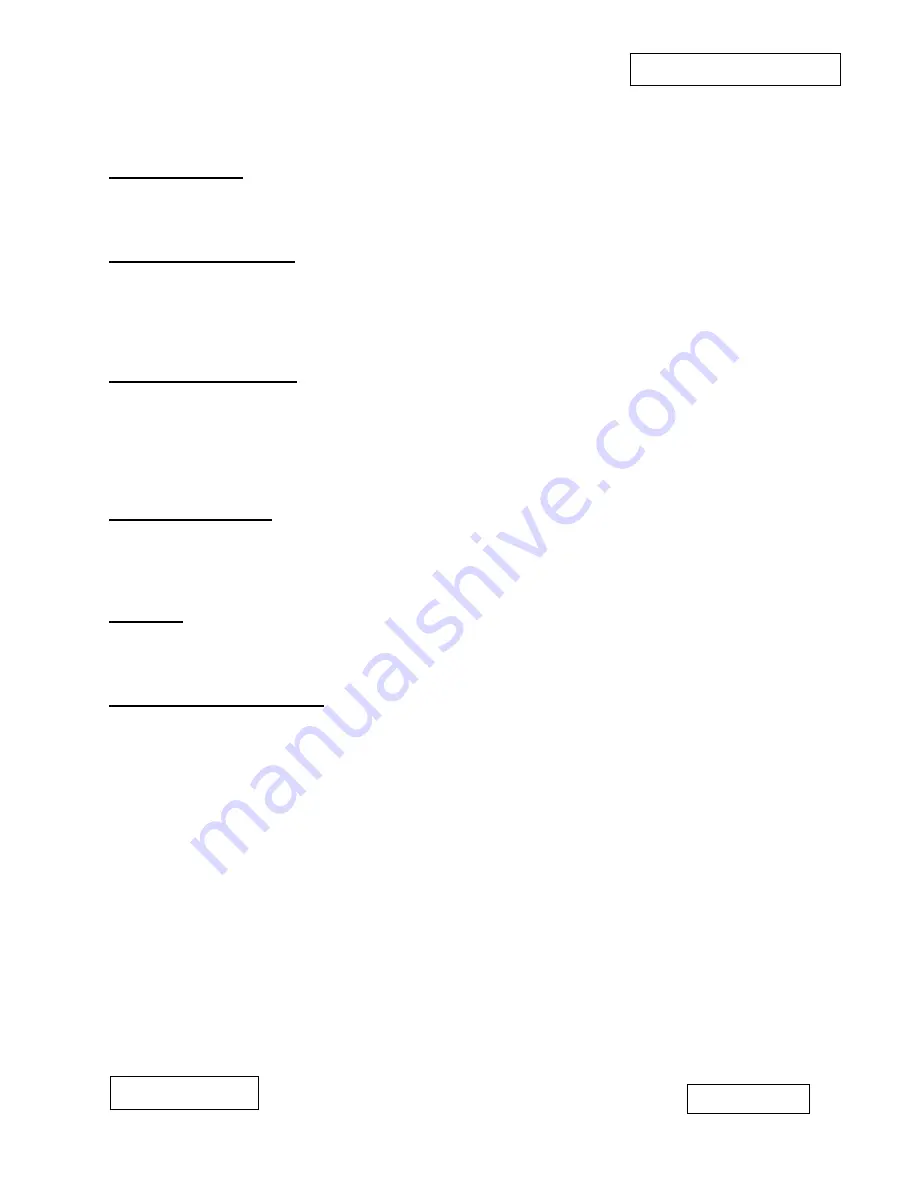
MADILL 1200
GENERAL DESCRIPTION
POWER UNIT
The Madill 1200 is powered by a Isuzu 285 HP diesel engine. The engine is direct cou-
pled to a main pump set which provides hydraulic power for all machine functions.
UNDERCARRIAGE
The crawler type undercarriage features compact variable speed hydraulic drive motors
“Plugged In” to 3 stage planetary gearboxes. Track rollers and idlers are lifetime lubri-
cated. Shock loading is absorbed by pre-loaded idler recoil springs and track tension is
maintained by grease cylinder tensioners.
OPERATOR’S CAB
Positioning of the cab provides the operator with excellent visibility while steel plate con-
struction provides safety. Simple layout and hands on controls facilitate simultaneous
functions. Standard features include air conditioning and an AM/FM/CD Player. Batteries,
circuit breakers and relays are conveniently located in a slide out tray in the bottom of the
cab.
MACHINE DECK
A clean and simple machine deck features twin frame rails with integrated underdecking.
The counterweight is at the rear under the deck. The fuel and hydraulic oil tanks are in
the center of the deck, providing a barrier between the engine and the hydraulic valves.
HOUSE
Two large swing out doors provide easy maintenance access. The hood is hydraulically
tilted via a hand pump. Large punched plate grills provide ventilation.
HYDRAULIC SYSTEM
The machine is equipped with four pumps and two valve block assemblies.
Pump #1 (Main Pump) powers the track drive, swing drive, boom cylinder, stick cylinder
and head tilt cylinder through six hydraulically piloted valves located on the main valve
assembly attached to the front of the hydraulic tank.
Pump #2 (Grab Arm Pump) powers the sawhead grab arm cylinders, accumulator arm
cylinders and the rotate through three electrically piloted valves located on the secondary
valve assembly attached to the mainframe web near the operator’s cab.
Pump #3 (Saw Disc Pump) powers the sawhead motor directly through an electrically
piloted saw on/off valve attached above the secondary valve assembly near the opera-
tor’s cab.
Pump #4 (Fan Drive Pump) is a closed loop pump that powers the hydraulically operated
fan through a fixed displacement motor. The fan speed is computer controlled with an
adjustable automatic purge cycle that provides reverse air flow for purging of debris build
up on the cooler package.
Section One
Page 3a
RETURN TO INDEX
Summary of Contents for 1200
Page 1: ......
Page 2: ......
Page 12: ...MADILL 1200 JOYSTICK CONTROL FUNCTIONS 1200 FLAT Page 5a Section One RETURN TO INDEX ...
Page 13: ...MADILL 1200 JOYSTICK CONTROL FUNCTIONS 1200 TILT Section One Page 5b ...
Page 20: ......
Page 21: ......
Page 22: ......
Page 23: ......
Page 24: ......
Page 25: ......
Page 26: ......
Page 27: ......
Page 28: ......
Page 29: ......
Page 30: ......
Page 31: ......
Page 32: ......
Page 34: ......
Page 35: ......
Page 38: ...MADILL 1200 ENGINE DIAGNOSTICS Page 13a Section One RETURN TO INDEX ...
Page 41: ......
Page 42: ......
Page 43: ......
Page 44: ......
Page 45: ......