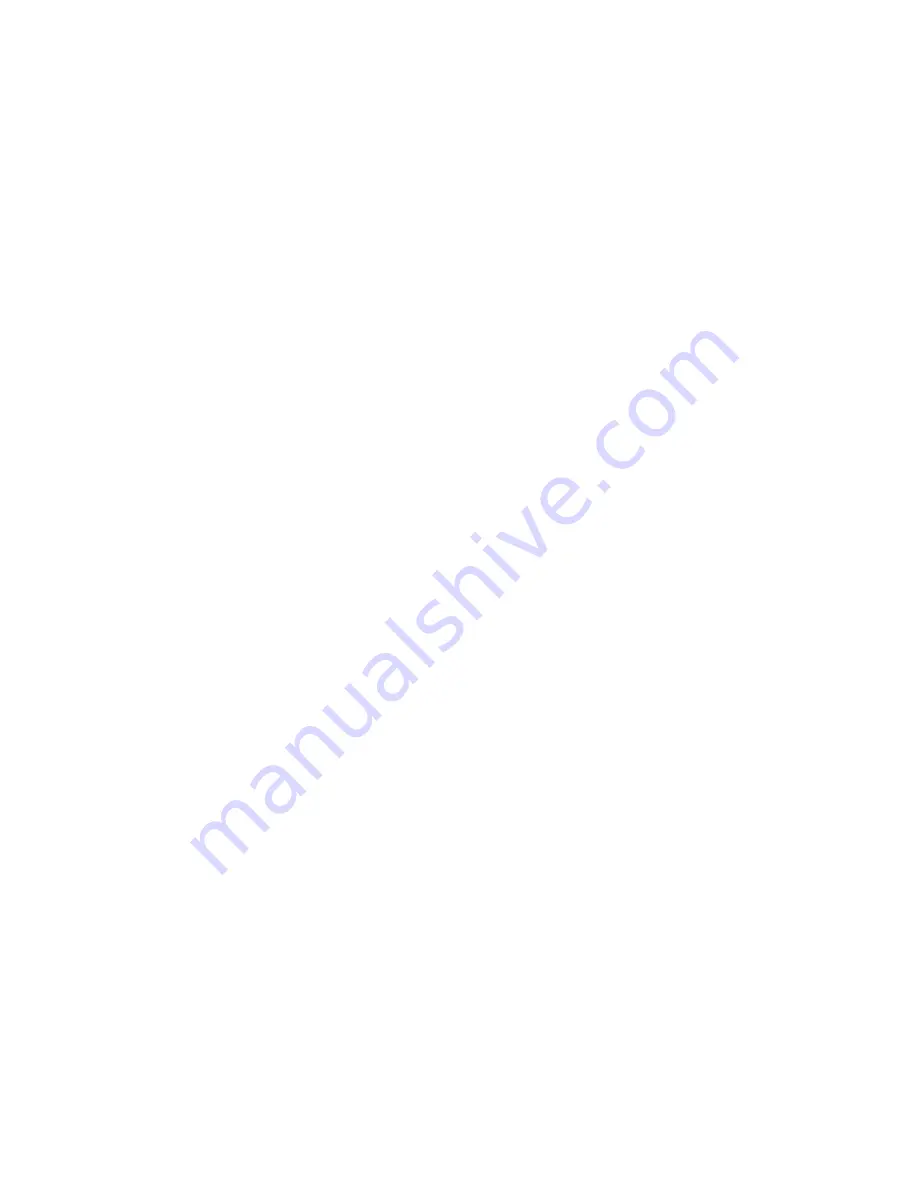
14. Maintain tools with care
–
Keep cutting tools sharp and clean for better
and safer performance.
–
Follow instructions for lubricating and changing
accessories.
–
Inspect tool cords periodically and if damaged
have them repaired by an authorized service
facility.
–
Inspect extension cords periodically and replace
if damaged.
–
Keep handles dry, clean and free from oil and
grease.
15. Disconnect tools
–
When not in use, before servicing and when
changing accessories such as blades, bits and
cutters. disconnect tools from the power supply.
16. Remove adjusting keys and wrenches
–
Form the habit of checking to see that keys
and adjusting wrenches are removed from the tool
before turning it on.
17. Avoid unintentional starting
–
Ensure switch is in”off” position when plugging in.
18. Use outdoor extension leads
–
When the tool is used outdoors,use only
extension cords intended for outdoor use and
so marked.
19. Stay alert
–
Watch what you are doing use common sense
and do not operate the tool when you are tired.
20. Check damaged parts
–
Before further use of tool,it should be carefully
checked to determine that it will operate properly
and perform its intended function.
–
Check for alignment of moving parts, binding of
moving parts ,berakage of parts, mounting and any
other conditions that may affect its operation.
–
A guard or other part that is damaged should be
properly repaired or placed by an authorized
service center unless otherwise indicated in this
instruction manual.
–
Have defectives switches replaced by an authorized
service center.
–
Do not use the tool if the switch does no turn it on
and off.
21. Warning
–
The use of any accessory or attachment other than
one recommended in this instruction manual may
present a risk of personal injury.
–
Use push-sticks or push blocks to feed the work-piece
past the saw blade.
–
Use and correct adjustment of the riving knife,
–
Use and correct adjustment of the upper saw blade
guard.
–
Rebating or grooving should not be carried out unless
suitable guarding, such as a tunnel guard, is fitted
above the saw table.
–
Saws shall not be used for slotting(stopped groove).
–
Use only saw blades for which the maximum possible
speed is not less than the maximum spindle speed
of the tool and the tool and the material to be cut.
–
When transporting the machine use only transportation
devices and do never use guards for handling or
transportation.
–
During transportation the upper part of the saw blade
should be covered; for example by the guard.
–
Do not use saw blades which are damaged or
deformed.
–
Replace table insert when worn.
–
Use only saw blades recommended by the
manufacturer, which conform to EN847-1.
–
Take care that the selection of the saw blades is
suitable for the material to be cut.
–
Wear respiratory protection to reduce the risk of
inhalation of harmful dust.
–
Saw blades shall be carried in a holder whenever
practicable;
–
Connect circular saws to a dust-collecting device when
sawing wood.
–
Do not use High speed steel(HS) blades.
–
The push-stick or push block should always be stored
with the machine when not in use.