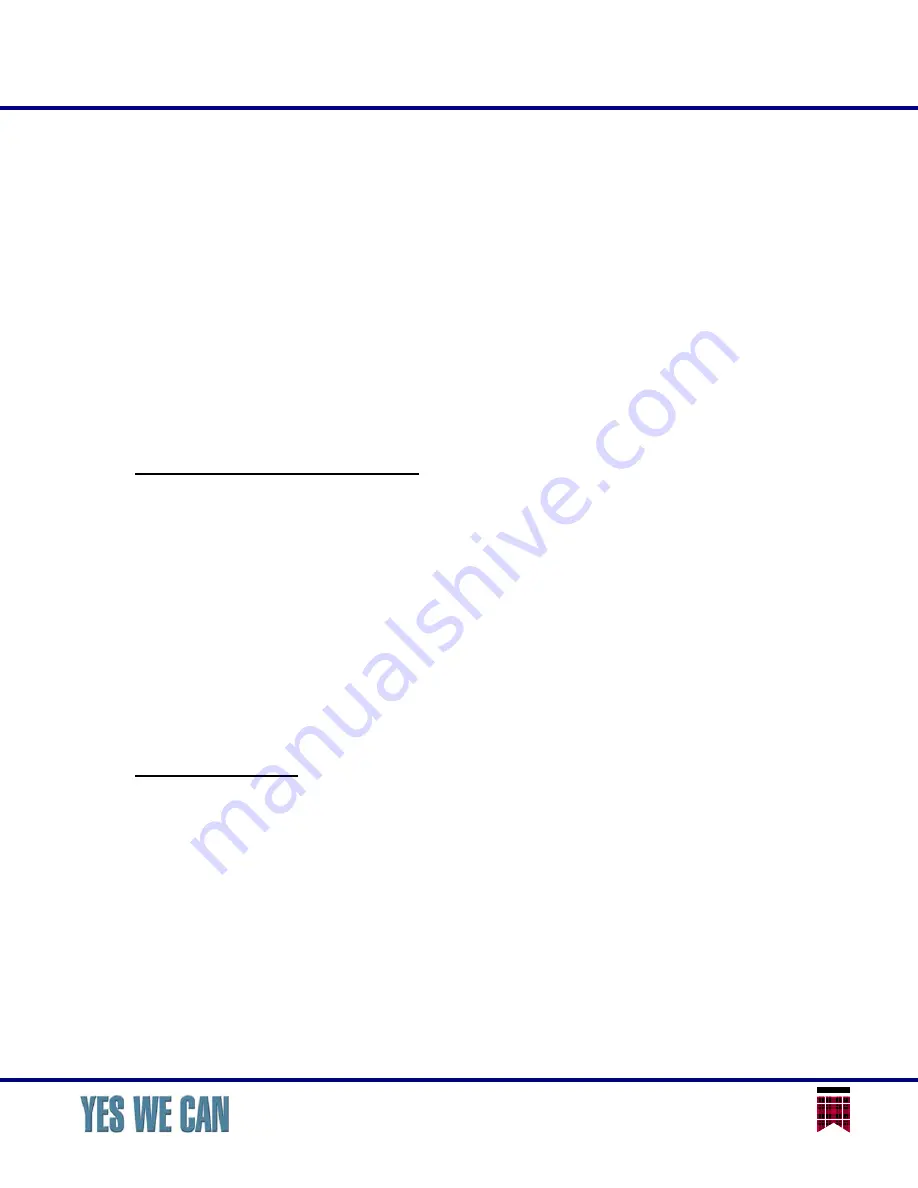
thickness of the media. To accommodate media thicknesses up to one inch, the entire
rail assembly is moved up and down by a pair of lift motors. The carriage assembly rides
along with the rail and is positioned precisely above the media by the aid of a sensor that
determines media thickness. Based on the detected thickness of the media, the rail is
moved to an appropriate height so that the carriage achieves the desired head height
above the surface of the media.
The standard or default head height is 0.085" above the surface of the media. The
standard head height will accommodate the majority of media with a good compromise
between minimized overspray and safe distance from the media to avoid headstrikes.
The maximum head height is 0.120" and the minimum is 0.065". Head height is set
through the control panel, requiring no tools or other operator intervention. The bidirec-
tional registration (see section IV) is automatically recalculated for different head heights,
no recalibration is required.
Automated Head Maintenance
Regular printhead maintenance (cleaning) is essential to long life and quality output. The
5400 printer uses an automated system to clean the printheads, requiring no operator
contact. The printhead cleaning routine is called the Purge. The printer uses a real-time
clock to track its usage and cleaning history, and will automatically initiate a Purge in
order keep the printheads in good condition. The operator can also command the printer
to Purge at any time by using a button on the control panel.
The Purge consists of two stages. First, air is pumped into the printheads to force ink out
through the nozzles, clearing any blockages. The service station then wipes the nozzle
orifices and conveys the expelled ink to a receptacle within the printer. For more difficult
blockages, more than one Purge may be necessary. A Purge can be performed on pairs
of adjacent heads only or on all heads together. (The pairs are dictated by the construc-
tion of the service station wiping assembly.)
UV Lamp System
Ultraviolet light energy is delivered by a pair of lamps on the carriage. Each lamp has
a shutter mechanism that opens and closes to regulate the output of the lamps. When
the lamp leaves the printable area of the media, the shutter closes to prevent light from
escaping; this prevents accidental curing of the ink on the printheads through reflection
of light onto the carriage. The shutters also can be configured to be partially closed while
over the media, which reduces the amount of heat transferred to the media. Excess heat
can cause some media to change shape (i.e., bow), leading to increased possibility of
head strikes.
Each lamp has two fans and a temperature sensor that control cooling of the bulb. The
lamps have a warm-up and cool-down cycle. If unused for a length of time, the lamps
will turn off the bulb and begin the cool-down cycle. If a print job is sent to the printer
during cool-down, the cycle must complete before the warm-up can begin. The control
5400 Technical Training Manual
MacDermid ColorSpan Confidential
Page 5 of 39
MacDermid, Inc. 11311 K-Tel Drive, Minnetonka, MN 55343
Phone: 952-944-9457 Fax: 952-944-8507